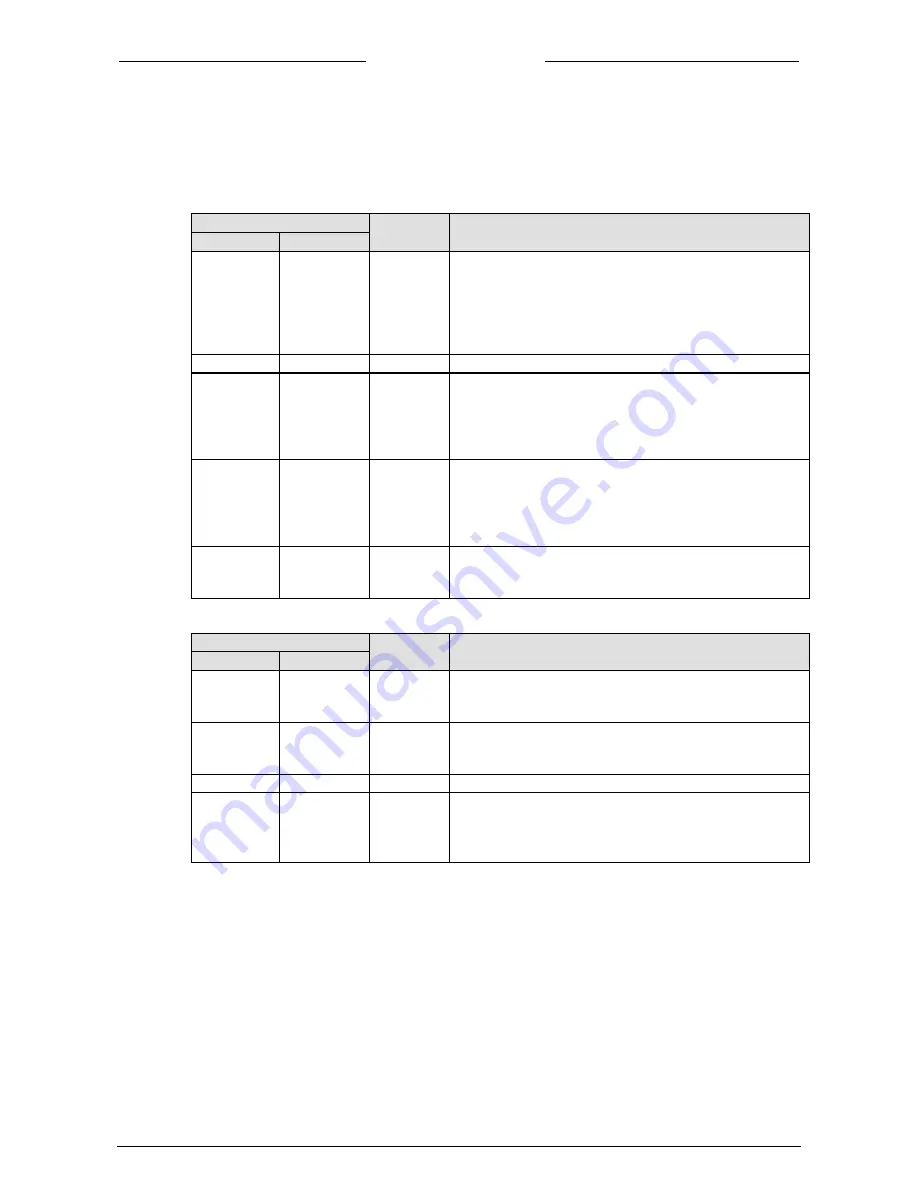
BRONKHORST®
Page 26
EL-FLOW
Base
Series Mass Flow Controllers
9.17.061
3.6 Push-button operation
By means of manual operation of the micro push-button switch some important actions for the
instrument can be selected/started. These options are available in both analog and digital operation
mode.
LED
’s
Time
Pushed
Indication
Green
Red
Off
Off
0 – 1 sec
Pressing a switch shortly by accident will not cause
unwanted reactions of instrument.
Pressing the switch 3x briefly with intervals of max. 1 sec.
will force instrument to indicate its bus-address/MAC-ID
and evt. baud rate. Check chapter 3.55, “Modbus RS485
operation” for more detials.
Off
Off
1 – 4 sec
Off
On
4 – 8 sec
Reset instrument
Instrument program will be restarted and all warning and
error message will be cleared
During (new) start-up instrument will perform a (new)
self-test
On
Off
8 – 12 sec
Auto-zero
Instrument will be re-adjusted for measurement of zero-
flow (not for pressure meter/controller)
NOTE: First make sure there is no flow and instrument is
connected to power for at least 30 minutes!
On
On
12 – 16 sec Prepare instrument for FLASH mode for firmware update.
Instrument shuts down and both LEDs turn off.
At next power-up instrument will be active again.
LED indications using micro-switch at normal running mode of an instrument
LED
’s
Time
Pushed
Indication
Green
Red
off
Off
0 – 4 sec
No action
Pressing a switch shortly by accident will not
cause unwanted reactions of the instrument
off
normal flash
4 – 8 sec
Restore parameters
All parameter settings (except field bus settings) will be
restored to situation of final test at BHT production
normal flash Off
8 – 12 sec
No action
normal flash normal flash
12 – 16 sec Manual install. The bus address and baudrate can be
changed by means of micro-switch en LEDs.
The procedure is described in 3.5.1 (
Change bus-
address/MAC-ID and baud rate
).
LED indications using micro-switch at power-up situation of an instrument