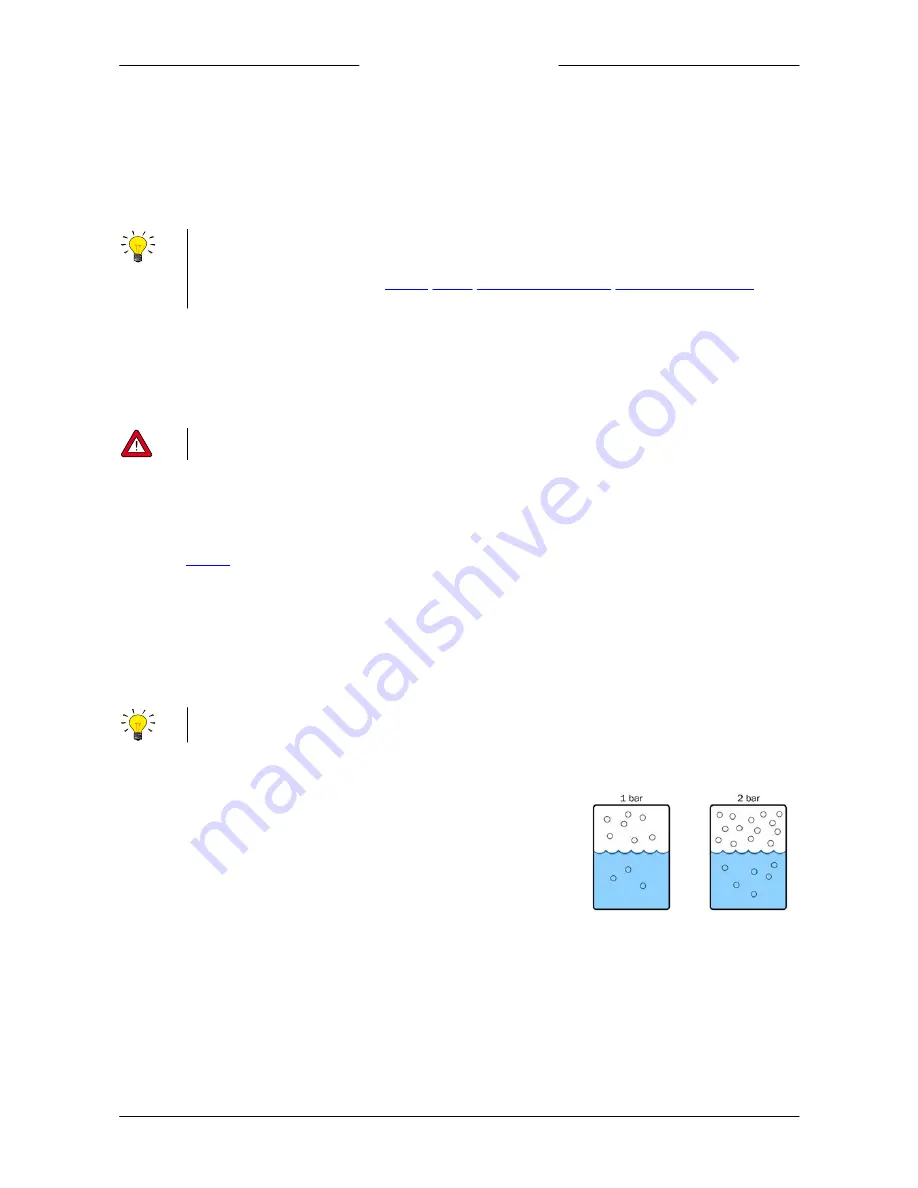
Bronkhorst®
Instruction Manual Controlled Evaporator and Mixer
9.17.126A
13
2.4.3
Working under vacuum
Depending on the used media and ambient conditions (temperature and pressure), draining and purging under vacuum
can shorten the time that is needed to have all components of the fluidic system clean and dry.
For draining and purging under vacuum, extending the fluidic system with some additional tubing and valves is strongly
recommended. This will facilitate easy and flexible deployment of the vacuum process, without sacrificing the accuracy and
reliability of the instrumentation of the CEM system.
·
To prevent leakage from the main fluidic path and the process to the vacuum lines, the vacuum lines should be
separated from the main line with leak proof shut-off valves
·
Additional components needed to enable vacuumising of the system may also require additional steps to be taken when
performing operational procedures (
bleeding
,
purging
,
starting vapour production
,
stopping vapour production
)
·
If necessary, contact your Bronkhorst representative for more information and assistance
2.5
Fluid supply
The recommendations in this section will help reduce risks of clogging and improve vapour flow stability.
2.5.1
Carrier gas
The carrier gas must be clean and dry. Impurities or particles in the gas can cause unwanted chemical reactions with the
liquid and/or clogging of the fluidic system.
·
If the presence of particles in your process media cannot be ruled out, installing a particle filter in the carrier gas supply
line (upstream from the flow controller) is strongly recommended.
·
If necessary, install a de-humidifier in the carrier gas supply line (upstream from eventual filters). Humidity in the carrier
gas can cause chemical reactions in the mixing valve in combination with certain liquids.
·
Purging the fluidic system before each use will reduce the presence of contaminants and remove moisture from the gas
lines. See
Purging
for instructions.
2.5.2
Liquid purity
·
If the presence of particles in your process media cannot be ruled out, installing a particle filter in the liquid supply line
(upstream from the flow controller) is strongly recommended.
·
Select a suitable filter size, to minimize the pressure drop, to prevent a degassing effect and instability of the liquid
supply.
·
For hydrophobic liquids use a hydrophobic filter.
Note that a filter will not stop dissolved matter like minerals and chemical stabilizers.
2.5.3
Minimizing gas dissolution
Henry's Law
Typically, the CEM will be supplied with liquid from a pressurized container.
However, pressurizing a liquid with a gas makes a portion of the gas dissolve in the
liquid. The higher the gas pressure, the more gas will be dissolved in the liquid
(Henry's Law: the solubility of a gas in a liquid is directly proportional to the partial
pressure of the gas above the liquid). When the temperature rises or the pressure
drops further down the line, the gas will come out of solution and form bubbles in
the liquid, which makes it unstable.