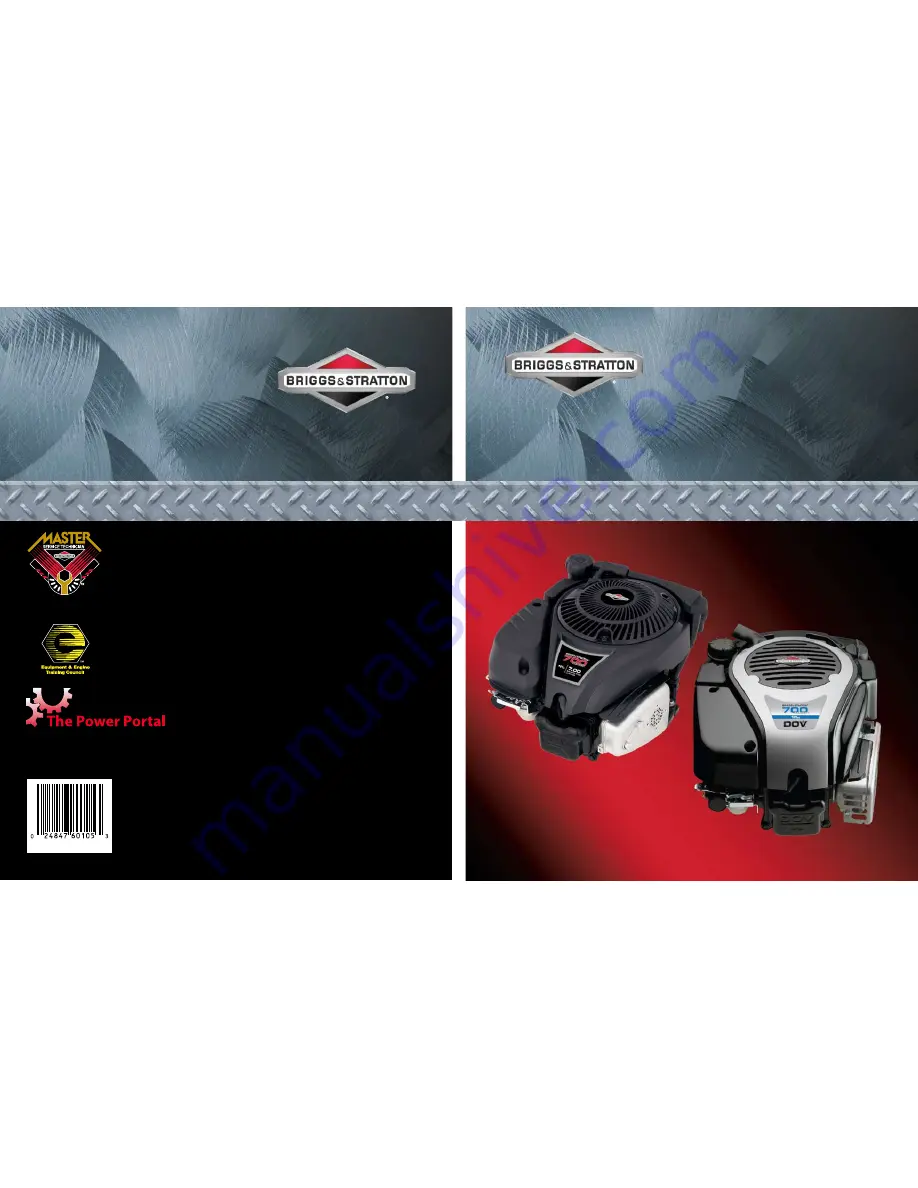
700/750
Serie
S
DOV
Air-C
OO
le
D
e
ngine
S
273521 Twin Cylinder OHV Air-Cooled Engines
276781 Single Cylinder OHV Air-Cooled Engines
271172 Twin Cylinder L-Head Air-Cooled Engines
270962 Single Cylinder L-Head Air-Cooled Engines
276535 Two-Cycle Snow Engines
CE8069 Out of Production Engines (1919-1981)
Repair Manuals for other
Briggs & Stratton Engines:
700/750 Series DOV
Air-Cooled Engines
Post office box 702
Milwaukee, wi 53201 usa
©2009 Briggs & Stratton Corporation
BRIGGS
&
STRATTON
coRPoRatioN
Part No. 277527-12/09
Quality Starts With A
Master Service Technician
www.thePowerPortal.com (Dealers)
bRiGGsandstRattoN.coM (consumers)
Briggs
&
Stratton
12/09
Summary of Contents for 700 DOV Series
Page 2: ......
Page 6: ...THISPROPER SERVICE AND REPAIR IS IMPORTANT TO THE SAFE ECONOMICAL AND RELIABLE...
Page 30: ...26 1 3 EXHAUST SYSTEM Figure 3 1...
Page 32: ...28 1 3...
Page 33: ...29 4 4 SECTION 4 FUEL SYSTEM AND CARBURETION FUEL TANK 30 CARBURETOR 32...
Page 34: ...30 4 4 FUEL TANK Figure 4 1...
Page 36: ...32 4 4 CARBURETOR Figure 4 2...
Page 38: ...34 4 4...
Page 40: ...36 4 5 GOVERNOR SYSTEM Figure 5 1...
Page 44: ...40 6 6 CYLINDER HEAD AND VALVES Figure 6 1...
Page 46: ...42 6 6...
Page 48: ...44 7 7 ELECTRIC STARTER Figure 7 1...
Page 50: ...46 7 7 REWIND STARTER Figure 7 2...
Page 52: ...48 7 7...
Page 54: ...50 4 8 LUBRICATION SYSTEM Figure 8 1...
Page 56: ...52 4 8...
Page 58: ...54 4 9 CYLINDER AND SUMP Figure 9 1...
Page 62: ...58 4 10 CRANKSHAFT Figure 10 1...
Page 64: ...60 4 10...
Page 66: ...62 4 11 PISTON RINGS AND CONNECTING ROD Figure 11 1...
Page 70: ...66 4 11...
Page 71: ...67 12 SECTION 12 ENGINE SPECIFICATIONS MODEL 090600 68 MODEL 100600 70 MODEL 100800 72...
Page 78: ...74 12...