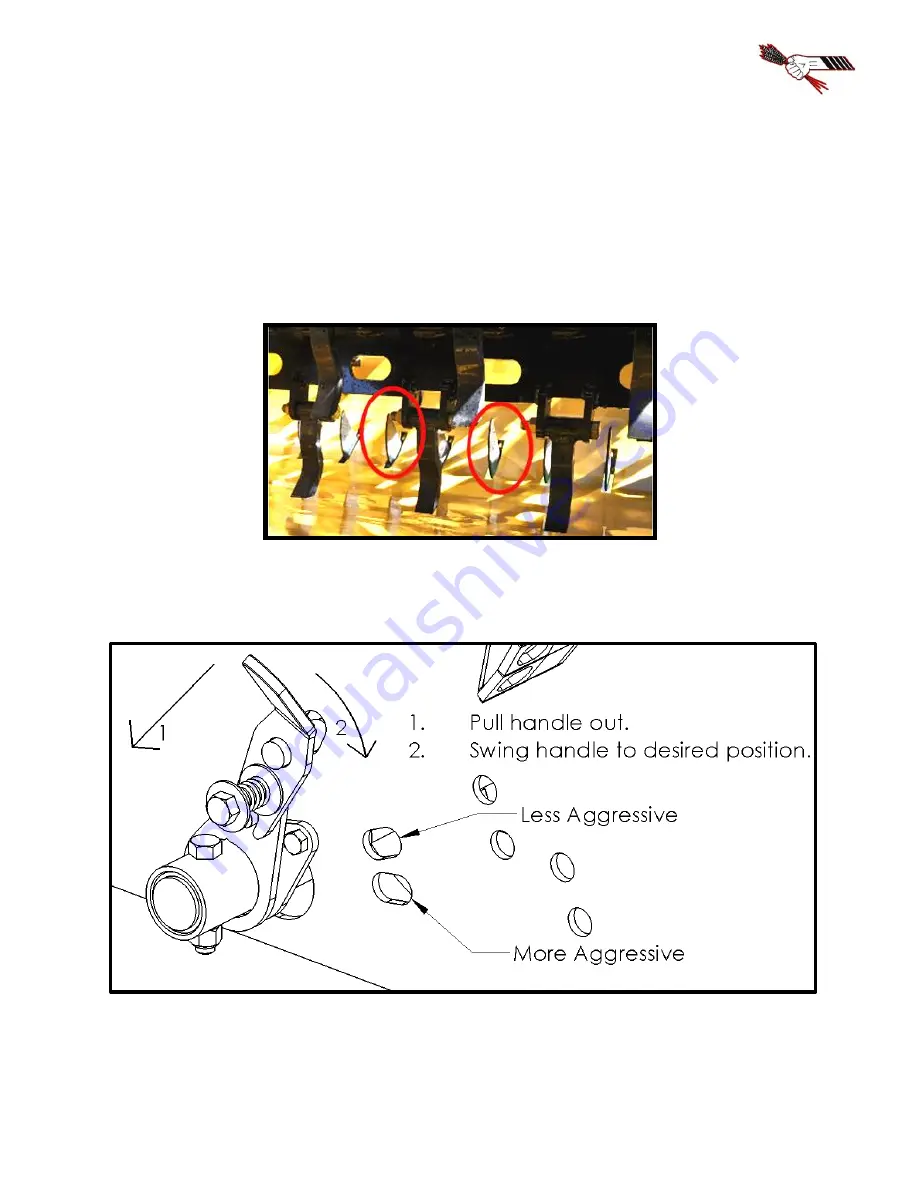
Bridgeview Manufacturing Inc.
18
Optional Fine Chop Kit
The Bale King 5300 processor has an optional fine chop knife kit
(BMI # 32117)
available to go
into the lower tub area. This option is available if you require a finer cut on the material which
you are processing such as slough hay and silage bales.
It is recommended that the knives be lowered when bedding straw as it will affect your
spread pattern. Adjust the machine as needed.
There are two settings for the fine chop, depending on how fine you wish to cut the
material. These settings achieved by pulling on the handle (towards the back of the machine), then
selecting the desired hole.
Summary of Contents for BALE KING 5300 Series
Page 46: ...Bridgeview Manufacturing Inc 42 Gearbox ...
Page 54: ...Bridgeview Manufacturing Inc 50 Rear Forks ...
Page 56: ...Bridgeview Manufacturing Inc 52 Deflector Hose Cover S N BK7168 Down ...
Page 58: ...Bridgeview Manufacturing Inc 54 S N BK7169 Up ...
Page 62: ...Bridgeview Manufacturing Inc 58 Hose Holder ...
Page 66: ...Bridgeview Manufacturing Inc 62 Left Arm ...
Page 68: ...Bridgeview Manufacturing Inc 64 Lockout Mechanism ...
Page 70: ...Bridgeview Manufacturing Inc 66 Center ...
Page 72: ...Bridgeview Manufacturing Inc 68 Right Arm ...
Page 74: ...Bridgeview Manufacturing Inc 70 TR Kit Option ...
Page 76: ...Bridgeview Manufacturing Inc 72 Tank Front ...
Page 78: ...Bridgeview Manufacturing Inc 74 Tank Rear ...
Page 80: ...Bridgeview Manufacturing Inc 76 Cross Auger ...
Page 82: ...Bridgeview Manufacturing Inc 78 Lid ...
Page 84: ...Bridgeview Manufacturing Inc 80 Fine Chop Option ...
Page 89: ...Bridgeview Manufacturing Inc 85 Hydraulics ...
Page 90: ...Bridgeview Manufacturing Inc 86 ...
Page 91: ...Bridgeview Manufacturing Inc 87 ...
Page 92: ...Bridgeview Manufacturing Inc 88 ...
Page 93: ...Bridgeview Manufacturing Inc 89 ...
Page 94: ...Bridgeview Manufacturing Inc 90 ...
Page 95: ...Bridgeview Manufacturing Inc 91 ...
Page 96: ...Bridgeview Manufacturing Inc 92 ...
Page 97: ...Bridgeview Manufacturing Inc 93 ...
Page 98: ...Bridgeview Manufacturing Inc 94 ...
Page 102: ...Bridgeview Manufacturing Inc 98 Lights Electrical Diverter Controls ...
Page 103: ...Bridgeview Manufacturing Inc 99 ...