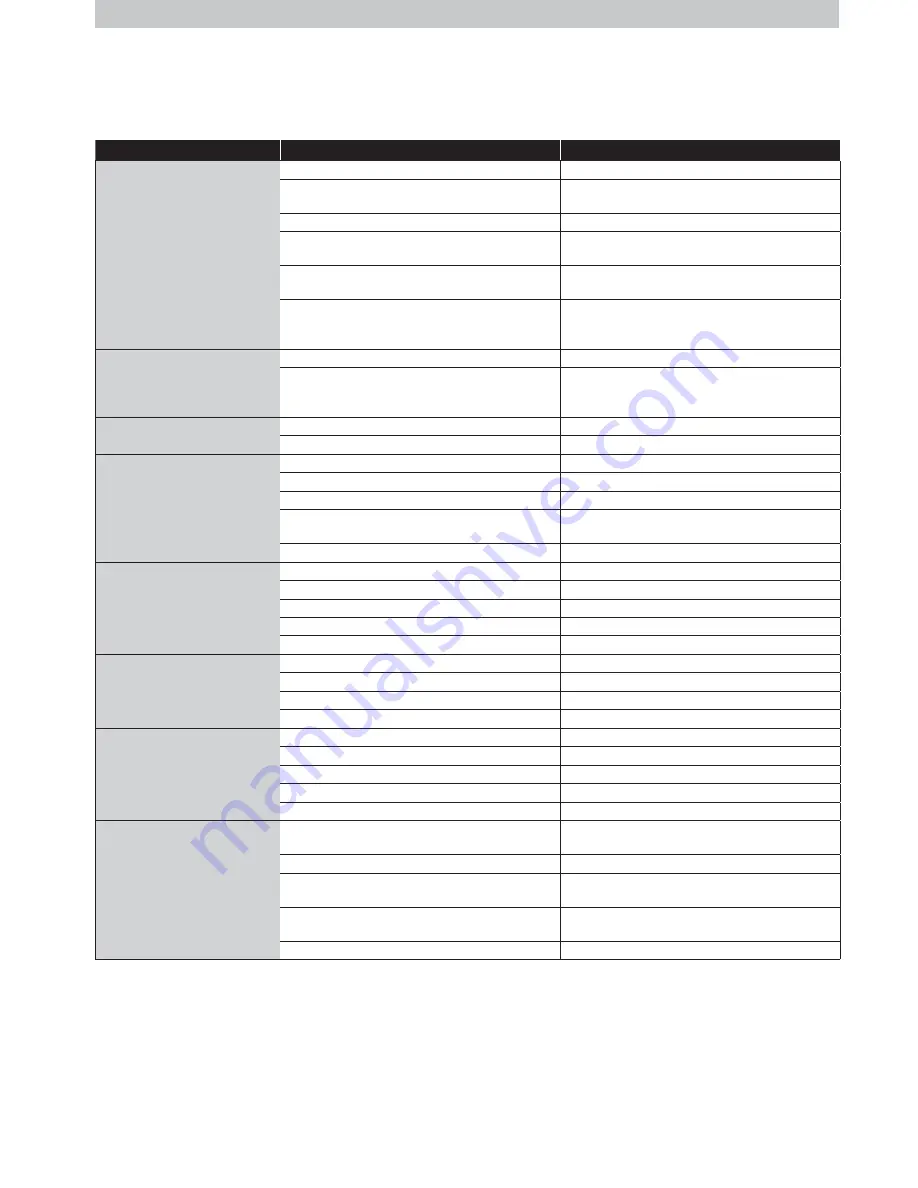
TBQ/TBS EVAPORATIVE COOLER INSTALLATION MANUAL
|
19
TROUBLE SHOOTING
Symptom
Cause
Action
Inadequate cooling
Under-sized cooler.
Replace with larger cooler.
Under-sized ducts.
Carry out cooling load design to determine correct size unit,
ducting and outlets required.
Clogged or dirty cooling pads.
Clean or replace pads.
Dry pads or lack of water while cooler is operating.
Check water distribution system for possible obstruction in
hoses. Check pump.
Insufficient air discharge openings or inadequate exhaust
from building, causing high humidity and discomfort.
Make sure there is adequate provision for exhausting stale
air from building (open windows and doors).
Excessive ambient humidity (see also item above re
inadequate exhaust).
On days during summer when ambient humidity is high the
cooler will not reduce the temperature as much as on drier
days. There is no remedy except to shut off the pump.
Noisy cooler
Fan out of balance due to dirt, etc.
Clean the fan.
Too much back pressure.
Tight duct bends.
Grilles too small.
Re-evaluate design; improve duct layout; change grille sizes.
Pump fails to operate.
Circuit breaker tripped.
Check pump for faults. Replace if necessary.
Pump motor failure.
Replace pump.
Fan fails to start.
Main power circuit breaker tripped.
Check cause of overload. Reset circuit breaker.
Fan motor burned out.
Replace motor.
Low system voltage.
Consult with power supply authority.
Check fault condition via the tri-colour LED on cooler
electronics module.
Rectify fault as indicated and restart the cooler.
MagIQtouch Controller failure.
Replace MagIQtouch Controller.
Pump runs but no water circulation
or Pump runs but pads lack water
Insufficient water in tank.
Adjust float level.
Water hoses blocked.
Check and clean out blockage.
Pump strainer blocked.
Clean pump strainer.
Insufficient water supply pressure
Check and confirm water supply pressure
Water solenoid is installed incorrectly
Check installed in the correct water flow direction
Continuous overflow of water.
Float valve adjustment not correct.
Adjust float valve.
Heavy pad deposits.
Clean or replace pads.
Drain Valve failure.
Replace Drain Valve.
Water solenoid is installed incorrectly
Check installed in the correct water flow direction
Water entering cooler outlet.
Loose water hose connections.
Tighten connections.
Water hose broken.
Replace cracked or broken hoses.
Cover not fitted on float valve.
Replace float valve.
Pads not fitted correctly into pad frames.
Install pad frame correctly.
Incorrect or damaged pads.
Replace with new Chillcel pads.
Unpleasant odour.
New cooler pads.
Drain tank, refill, run pump for a few hours. Odour will
dissipate after a number of hours of operation.
Cooler located near source of unpleasant odour.
Remove source of odour or relocate cooler.
Algae in tank water.
Drain pan, clean thoroughly with strong cleansing agent,
refill, change pads.
Pads remain wet after shut down.
Run fan on "vent" for 10 minutes after cooling cycle to dry
pads out.
Heavy pad deposits.
Clean or replace pads.