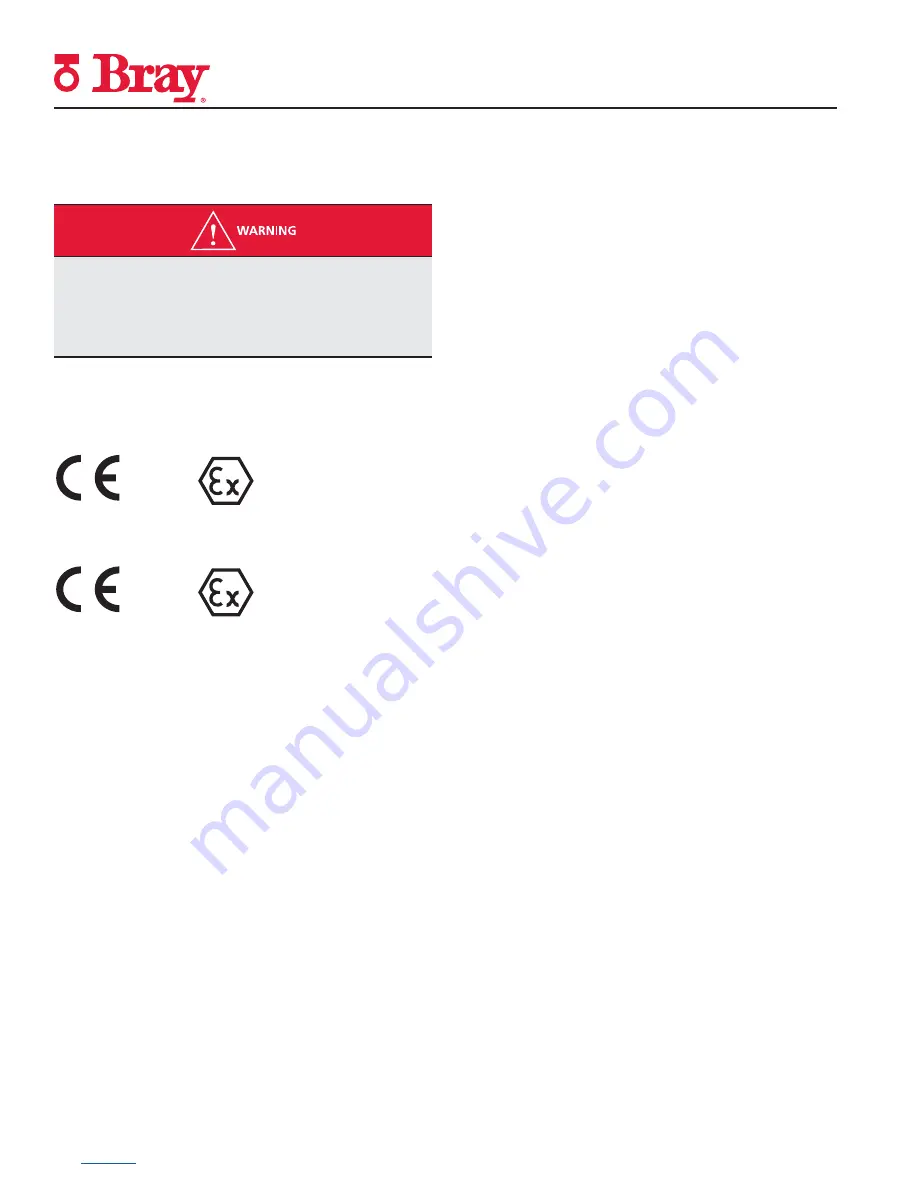
Tri Lok
®
Cryogenic Valve
Installation, Operation and Maintenance Manual
3 |
2.0 SAFETY INFORMATION
2.1 ATEX Directive 2014/34/EU
When using this product in hazardous environments, the
national directives and laws which apply in your country for
hazardous areas must be followed The specifications of the
examination certificate valid in country of operation must be
also observed
2.1.1 Marking
Certification Code:
Non-Mining Applications
0343
2813
II 1G Ex h IIC Tx Ga
Mining Applications
0343
2813
I M1 Ex h Tx Ma
Ambient Range:
TX See Special Conditions for Safe Use
Serial Number:
As appropriate
2.1.2 Special Conditions for Safe Use
The following factors must be carefully considered in order
to ensure the valve is compatible with the atmosphere in
which it is applied The system designer and/or end user
should formally address each item and carefully document
the reasoning behind specific measures taken to ensure
continued compliance throughout the life of the Tri Lok
valve
Material Considerations
Titanium is not to be used in Group I mining applications
and Group II Category 1 equipment, due to the potential of
ignition from sparks caused by mechanical impacts Please
consult factory for details regarding material limitations
Temperature Considerations
The surface temperature of the Tri Lok valve is wholly
dependent on the ambient temperature in combination
with the temperature of the process medium The
maximum surface temperature of the Tri Lok valve may
be calculated from the maximum ambient temperature
plus the maximum process medium temperature as shown
below:
Equation 1 - Surface Temperature Calculation
T
s(max)
= T
a(max)
+ T
p(max)
The system designer is responsible for ensuring the
maximum temperature, either inside the valve body or on
the external surface, will remain well below the ignition
temperature of the atmosphere Additional protective
devices may be required to ensure a sufficient thermal
safety margin, including but not limited to: thermal shut-
off devices and cooling devices
For operating temperatures above 200° C (392°F) Bray
recommends thermal insulation of the valve body.
Static Electricity Considerations
Where the process medium is a liquid or semi-solid material
with a surface resistance in excess of 1 G-ohms, special
precautions should be taken to ensure the process does
not generate electro-static discharge This may be done
through ensuring the flow rate of the process media
remains below 1 m/s or providing sufficient discharge
points along the process path to eliminate electrostatic
build-up Consultation to EN 50404 is recommended
Appropriate grounding may be necessary through the use
of grounding straps or other means
Stray Electric Current Considerations
When the Tri Lok valve is used near sources of high current
or magnetic radiation, a secure bonding to earth ground
should be made so as to prevent ignition due to inductive
currents or a rise in temperature due to these currents
Filtration of Process Medium Considerations
Special consideration should be made regarding the
filtration of the process medium if there is a potential for
the process medium to contain solid particulates The
process medium is recommended to be filtered to allow
particles no greater than 1 0 mm in diameter through the
valve assembly where there is a high probability of solid
particulates Larger particulate sizes may be deemed
appropriate based on the possibility of particulates within
the process medium and the area classification The
decision regarding filtration levels and limits should be well-
documented by the system designer and/or end user to
ensure continued compliance through the life of the valve