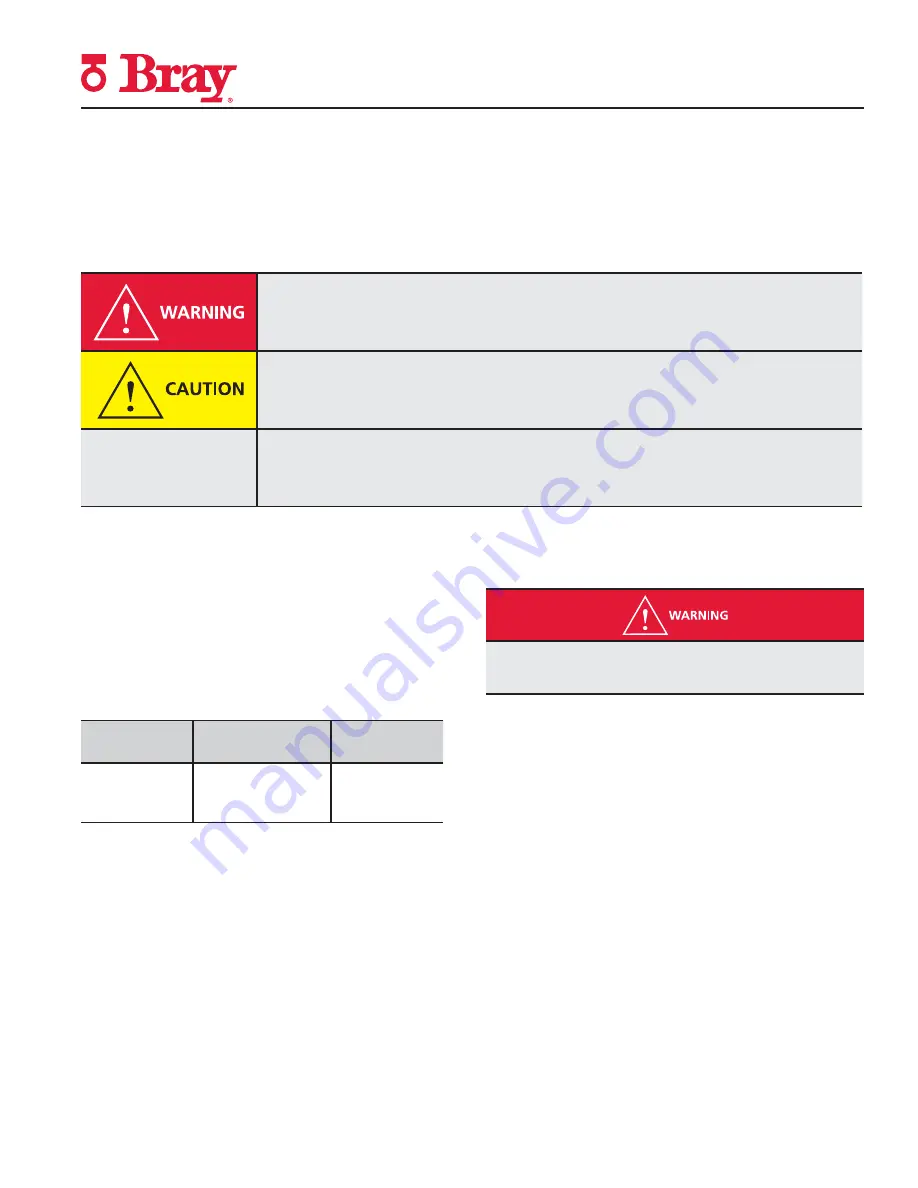
Tri Lok
®
Cryogenic Valve
Installation, Operation and Maintenance Manual
TRI LOK
®
CRYOGENIC TRIPLE OFFSET VALVE
| 2
DEFINITION OF TERMS
indicates a potentially hazardous situation which, if not avoided, could result in death or
serious injury
indicates a potentially hazardous situation which, if not avoided, may result in minor or
moderate injury
NOTICE
used without the safety alert symbol indicates a potential situation which, if not avoided, may
result in an undesirable result or state, including property damage
Read and Follow These Instructions
Save These Instructions
1.0 INTRODUCTION
Information provided in this manual is for cryogenic
Tri Lok configuration only. Specific instructions for
non-standard materials of construction, temperature
range, etc. should be referred to the factory.
This manual covers Tri Lok valves in the following range:
ASME
Class
Size
Body Style
150, 300,
and 600
3” - 48”
(80mm - 1200mm)
Wafer
Lug
Double Flange
The Tri Lok metal seated valve is fully rated to ASME
B16 34, and complies with API 609
Tri Lok is torque-seated Torque must be continually applied
by an actuation device (manual gearbox or power valve
actuator) to the valve stem to ensure the valve seals against
the line pressure
Do not remove or de-energize actuation devices while the valve
is under line pressure
The valve is inherently fire safe, and has been qualified to
ISO 10497 and API 607 standards
The preferred direction of valve installation is with the
upstream line pressure on the stem side and the body seat
on the downstream side
The preferred direction of flow is indicated by an arrow on
the valve nameplate