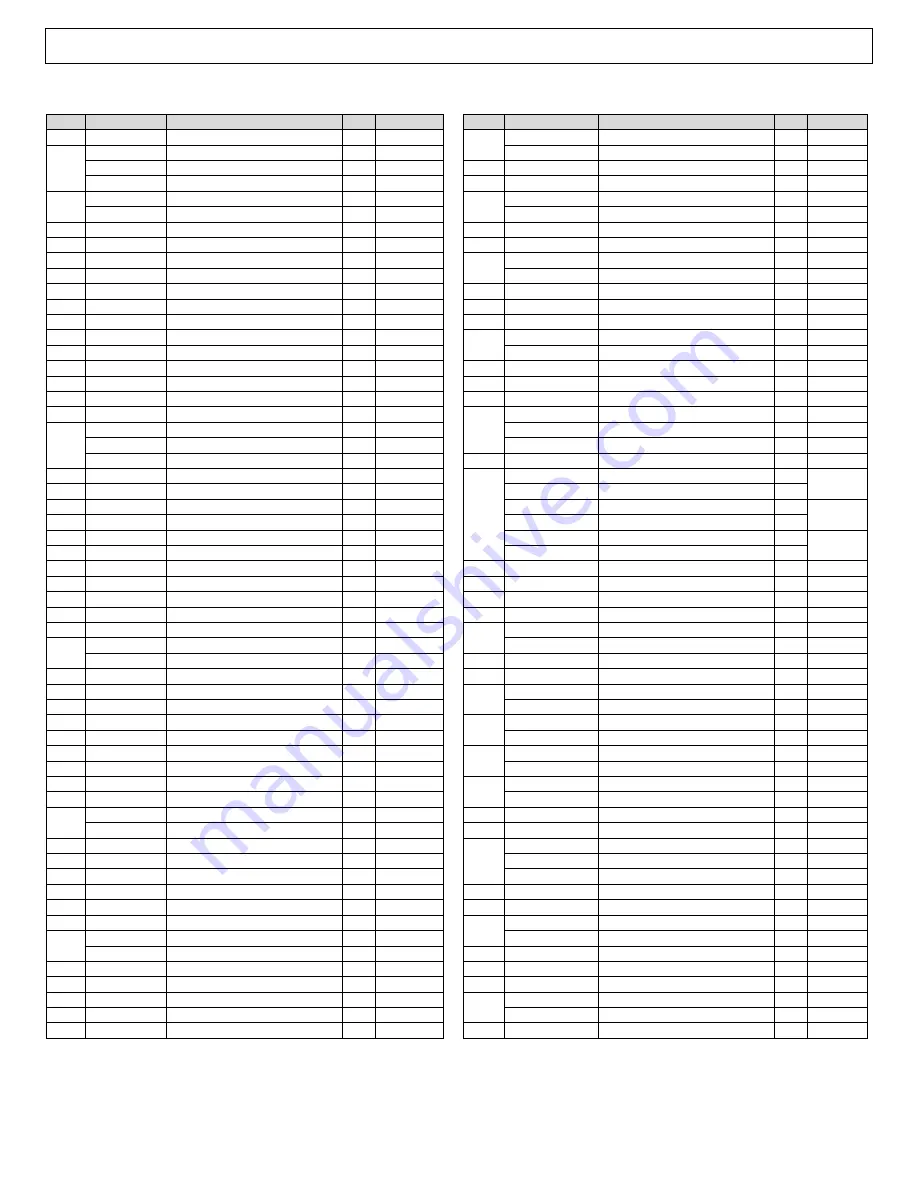
31
Parts Breakdown – Exploded View – Rev A
Unit Key: A = VH1724GC, B = VH1730GC, C = VH1737GX
Ref
Part
Description
#
Unit
Ref
Part
Description
#
Unit
1
17141
3/4" Hose Clamp
2
All
52
788243
Latch Rod, Short
1
B,C
2
GC160
Honda GC160 Engine
1
A
790897
Latch Rod, Long
1
A
GC190
Honda GC190 Engine
1
B
53
788244
Latch Rod Pin
1
All
GX270
Honda GX270 Engine
1
C
54
788245
Latch Spring
1
All
3
82087
5/16” - 18 x 3/4” HHCS
4
A,B
55
778829
MNPT x Hose Barb Elbow
1
A
82089
5/16” - 24 x 3/4” HHCS
4
C
788504
1"NPT X 1" HB Elbow
1
B,C
4
82601
5/16” - 24 x 1” HHCS
4
All
56
791219
12 MOR-8 FP X 45 Forged
1
All
5
82100
5/16” Split Lock Washer
8
All
57
787711
1/2” Magnetic Hex Plug
1
All
6
82201
M10 Washer
1
All
58
791244
Filter Head
1
All
7
778844
Axle Washer
2
All
BR001113
Filter Canister
1
All
8
82266
M10-1.5 x 80 HHSF
1
All
59
BR008301
Wheel Assembly
2
All
9
82270
M10-1.5 Nyloc Nut
1
All
60
791869
Valve
1
All
10
782689
18” Lanyard
3
All
BR004101-SK
Valve Seal Kit
1
All
11
82642
M12-1.75 Nyloc Nut
16
All
61
4011
3/4” Strainer
1
A
12
82280
M8-1.25 x 40 HHSF
4
All
790470
1” Strainer
1
B,C
13
82281
M8-1.25 Ser. Flange Nut
21
All
62
790471
Manual Tube
1
All
14
82292
M8-1.25 x 20 HHCS
8
All
63
790472
Pivot Pin
1
All
15
82528
M14-2 x 85 HHSF
1
All
64
790488
Straight Fitting
1
All
16
82529
M6 x .75 Self Tapping Screw
2
All
65
790677
13 GPM Pump
1
B
17
796119
Decal, Beam Logo, VH1722
2
A
791861
16 GPM Pump
1
C
796132
Decal, Beam Logo, VH1730
2
B
791862
11 GPM Pump
1
A
796133
Decal, Beam Logo, VH1737
2
C
66
791187
Valve Plate
1
All
18
82546
M8-1.25 x 70 HHSF
1
All
67
794825R
5” x 24” Cylinder w/ Decals
1
C
19
82551
M12-1.75 x 1 1/4 HHSF
4
All
783888
Cylinder Seal Kit
1
20
82561
M8-1.25 x 25mm Flange bolt
9
All
794826R
4.5”x 24” Cylinder w/ Decals
1
B
21
82562
M6-1 x 35 BHCS
3
All
794826K
Cylinder Seal Kit
1
22
82563
M6-1 Nyloc NUT
3
All
794827R
4” x 24” Cylinder w/ Decals
1
A
23
82564
M8 Flat Washer
13
All
783885
Cylinder Seal Kit
1
24
82569
M12 - 1.75 x 80 HHSF
4
All
68
794721
Right Log Cradle Mount
2
All
25
82570
M14 - 2 Nyloc Nut
1
All
69
794937
Left Log Cradle Mount
2
All
26
777124
Spindle Castle Nut
2
All
70
794722
Log Cradle Face Plate
2
All
27
777495
M8 - 1.25 Nyloc Nut
13
All
71
794528
Keeper
2
All
28
777835
13/16"-1 3/4" Hose Clamp
2
All
72
794529
Keeper Spacer, Small
2
B,C
29
3030
Pump Bracket, Small
1
A,B
794700
Keeper Spacer, Large
2
A
BR020110
Pump Bracket, Large
1
C
73
794474
Axle/Tank Weldment
1
All
30
794797
HP Supply Hose 1/2"x 62"
1
All
74
794487
Tow Bar
1
All
31
794798
LP Return Hose 3/4" x 67"
1
All
75
794479
Beam Weldment, Small
1
A
32
795052
Support Leg
1
All
794506
Beam Weldment, Large
1
B,C
33
BR008540
2" Trailer Coupler
1
All
76
BR006001B
L090/095 Coupling Insert
1
C
34
778459
Hand Grip
1
All
BR006002B
L075 Coupling Insert
1
A,B
35
1130
27" Chain w/ Hook
2
All
77
BR006001C
L095 x 1” Coupling
1
C
36
778592
Cylinder Pin
1
All
BR006002C
L075 x 3/4” Coupling
1
A,B
37
794939
Beam Rest
1
All
78
BR006001D
L095 x 1/2” Coupling
1
C
38
794924
Handle
1
All
BR006002D
L075 x 1/2” Coupling
1
A,B
39
794800
LP Suction Hose 1" x 22"
1
B,C
79
BR003017D
Exhaust Deflector
1
A,B
795038
LP Suction Hose 3/4" x 22"
1
A
80
785907
Exhaust Deflector Screw
2
A,B
40
778642
90 O-Ring x Barb
1
All
81
796120
24 Ton Decal
2
A
41
BR008301F
Cotter Pin
5
All
796121
30 Ton Decal
2
B
42
794794
M12-1.75 x 60 Carriage
8
All
796122
37 Ton Decal
2
C
43
794653
Log Dislodger
1
All
82
82157
Zip Tie
2
All
44
778827
O-Ring x FNPT Swivel Elbow
2
All
83
794722K
Cradle Kit (Left and Right)
1
All
45
778829
MNPT x Hose Barb Elbow
1
All
84
788243K
Latch Rod Kit, Short
1
B,C
46
82141
Key, 3/16 x 1-1/2
1
A,B
790897K
Latch Rod Kit, Long
1
A
82143
Key, 1/4 x 1-3/4
1
C
85
791869HK
Handle Kit
1
All
47
778498
Pin Catch, 5/16" x 3.5"
2
All
86
796084
Cylinder Clevis Cotter Pin
2
All
48
124A
Dust Cap
2
All
87
792778
Hairpin Cotter Pin
1
All
49
794799
HP Cylinder Ext. Hose
1
All
88
796117
Decal, Brave Logo
1
A, B
50
784455
LS Breather/Dipstick
1
All
796118
Decal, Brave Pro Logo
1
C
51
794647
Wedge
1
All
89
790564
Adapter Sleeve
1
A, B