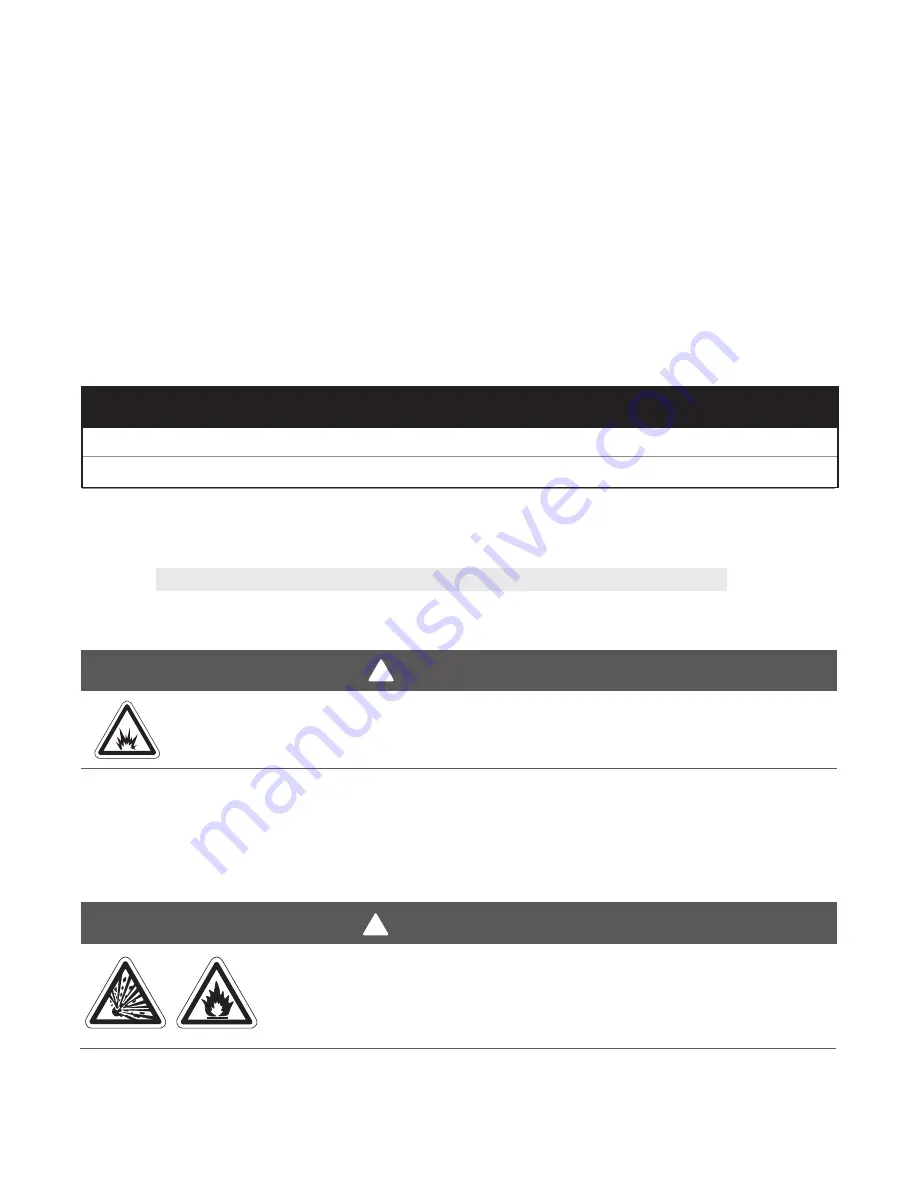
40
DET3
Series
3.0
Installation
•
Combustion Air Requirements
•
Gas Supply
Chart 3.7
•
Manifold Pressure
Pressure Equivalents:
1 inch W.C. equals .058 oz/sq. in. equals 2.49 mbar.
NOTE:
Check manifold pressure at the tap on the gas valve. Small variations in manifold pressure (actual
vs. published) may exist due to changing atmospheric conditions. Readings will be above atmospheric
pressure.
IMPORTANT!
Before connecting the gas supply to the burner control box:
• Verify that the heater’s gas type (as listed on the rating plate) matches that of your application and
the installation complies with national and local codes and requirements of the local gas
company.
• Unless otherwise noted on the rating plate, this infrared heater is designed and orificed to operate
on standard BTU gas. Contact the factory if utilizing non-standard BTU gas.
• Check that the gas piping and service has the capacity to handle the total gas consumption of all
heaters being installed, as well as any other gas appliances being connected to the supply line.
• Check that the main gas supply line is of proper diameter to supply the required fuel pressures.
• If utilizing used pipe, verify that its condition is clean and comparable to a new pipe. Test all gas
supply lines in accordance with local codes.
To connect the gas:
The DET3 Series heater is equipped to connect to the Type 1 rubber gas connector (Included).
Do not
connect the main gas line directly to the heaters gas inlet without the use of the flexible
connector.
All piping must be installed in accordance with the requirements outlined in the National Fuel
Gas Code ANSI/Z223.1 (latest edition) or CSA-B149.1. Support all gas piping with pipe hangers, metal
strapping, or other suitable material. Do not rely on the heater to support the gas pipe.
WARNING
!
Failure to install, operate or service this appliance in the approved manner may result in
property damage, injury or death. Only trained, qualified gas installation and service
personnel may install or service this equipment.
WARNING
!
Always use two (2) opposing wrenches to tighten mating pipe connections to
prevent excessive torque on the gas valve and manifold pipe. Excessive
torque can damage the valve and/or misalign the orifice, resulting in fire,
explosion, serious injury or death.
Natural 3.5 Inches W.C 5.0 Inches W.C 14.0 Inches W.C
Liquefied Petroleum 10.0 Inches W.C
11.0 Inches W.C 14.0 Inches W.C
Type of Gas
Required Manifold
Pressure
Minimum
Inlet Pressure
Maximum
Inlet Pressure