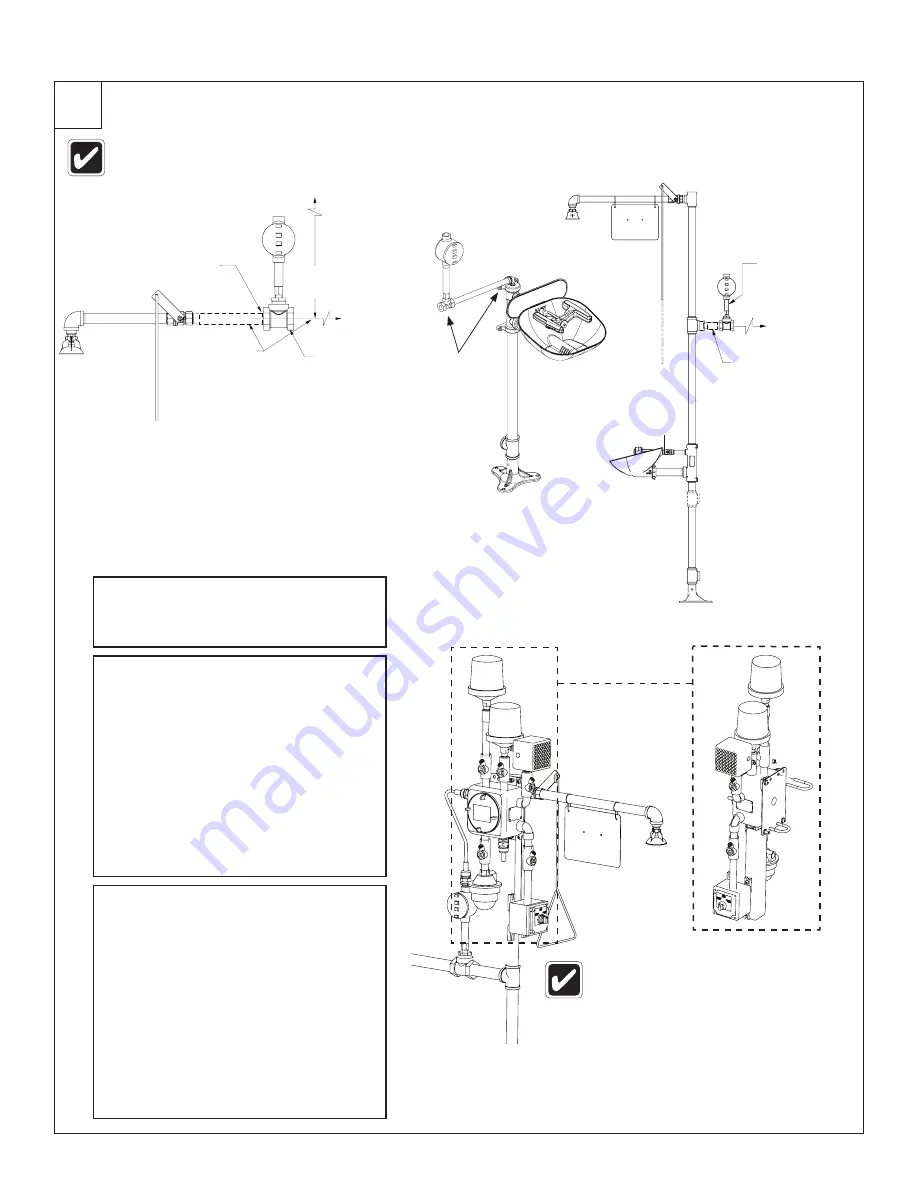
5
Installation
S19-324D2
Bradley •
215-1847 Rev. G: ECO 20-05-028
6/11/2020
1 Install the Flow Switch and Mount Signaling Assembly
The flow switch will attach to the mounted alarm via a 6, 12 or 50 foot waterproof cable.
Keep the location for mounting the alarm in mind when choosing the flow switch location.
A
Choose a location for mounting the
flow switch in a horizontal run of the
water supply line .
B
Mount the flow switch assembly in
the water supply line .
• The switch body must be in the
vertical position with the water
pipe horizontal .
• The water flow must be in the
direction marked by the arrow on
the flow switch body .
• Use teflon tape or pipe sealant
(supplied by installer) on all water
pipe connections .
C
Choose a location for mounting the
alarm . For best visibility, the signaling
system should be mounted at least 7'
above ground level .
• The signaling system may be
mounted directly to the drench
shower piping using the supplied
U-bolts and nuts .
• The signaling system can also be
bolted to a flat surface such as
a wall (hardware for this type of
installation is NOT supplied) .
NOTICE! If the water supply line will be exposed to
temperatures at or below freezing, the inlet supply
must be freeze-protected 6 inches above the flow
switch tee (freeze protection by others).
16" (406mm)
min . ceiling
clearance
To 1" Water
Supply
Flow Switch
1¼" to 1"
Reducing
Bushing
required
Piping supplied by
installer (must be
minimum 6 inches
from any fittings)
Flow Switch
optional location
(recommended
location for brass
flow switch is
inside of wall)
To 1¼" Water
Supply
Recommended Location
for Flow Switch
Piping supplied
by installer
(must be
minimum 6
inches from any
fittings)
Flow Switch
Clearances Needed
1/2" Piping
supplied by
installer (must be a
minimum 3 inches
from any fittings)
If multi-tone horn option is selected, it
must be mounted separately following
horn manufacturer's instructions.
Mounting hardware is supplied by
installer.