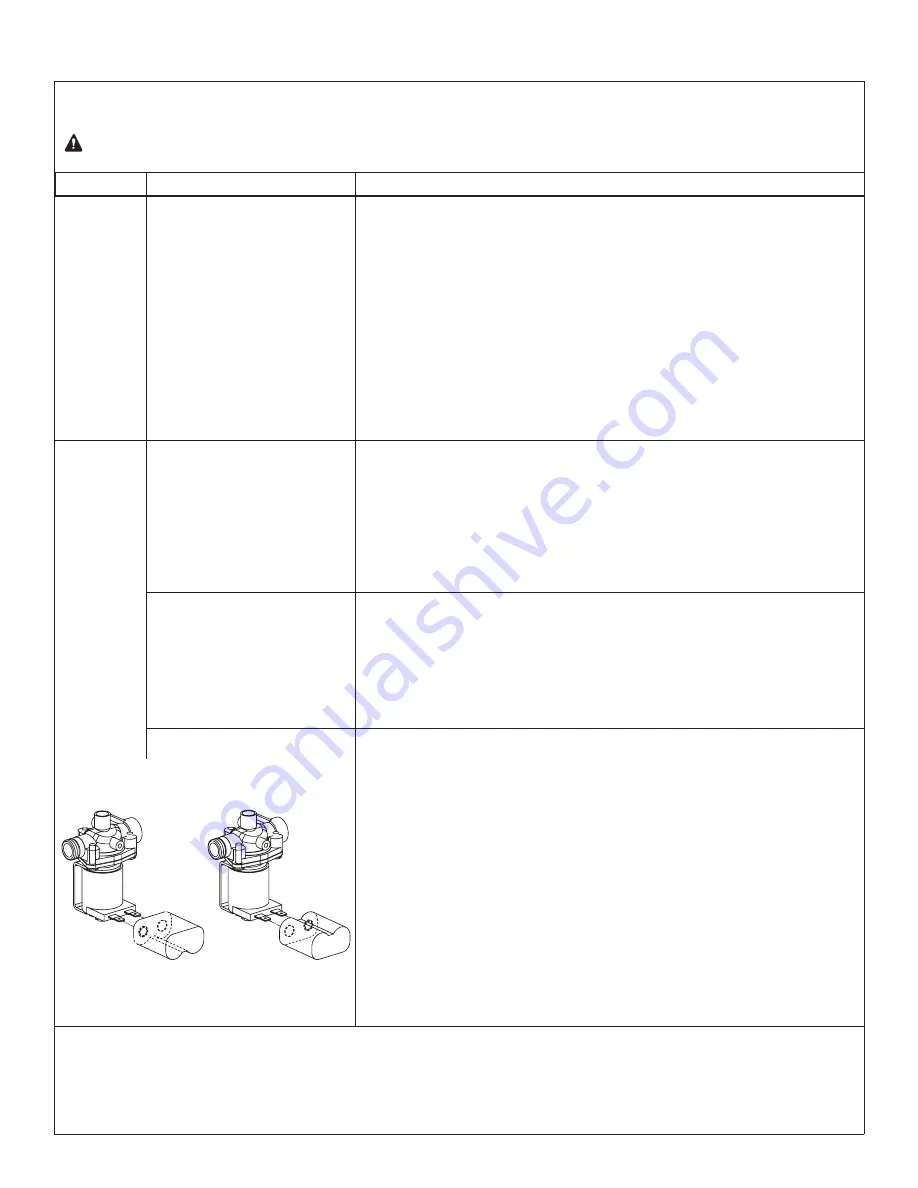
SS-3N/BIR3/STD, SS-3N/BIR3/WH
Installation
12
9/7/2018
Bradley
• 215-1496 Rev. J; ECN 17-08-026
Troubleshooting – BIR3 Components
Problem
Cause
Solution
An individual
operating
station fails
to shut off
and drips.
Debris is trapped between the
diaphragm and the valve seat.
Remove debris between diaphragm and the valve seat.
1. Disconnect the plug from the battery to the circuit board of the problem
valve.
2. Remove the three #8 Phillips-head screws that hold the solenoid valve
assembly together. Be careful not to lose the armature or spring.
3. Remove the diaphragm. Remove any particles that have been trapped
between the diaphragm and the valve seat. Rinse off the diaphragm and
inspect for damage. Make sure the center orifice and both small side orifices
are open.
4. Reassemble in reverse order (do not overtighten the Phillips-head screws
or the plastic valve body may crack). Tighten until the armature plate makes
contact with the plastic body.
5. Reconnect the battery plug. Turn on water supplies to the unit.
An individual
operating
station fails
to turn on or
off.
A dead or faulty battery.
Test the station to determine the cause and replace battery if required.
1. Disconnect the sensor cable from the circuit board of the problem valve.
Disconnect the sensor cable from the circuit board of an adjacent working
valve.
2. Connect the battery plug from the adjacent working valve to the problem
valve. Wait for ten seconds. Activate the problem station’s sensor ten times.
The station should turn on.
If the adjacent station turns on, and cycles normally, replace the battery.
Faulty sensor eyes.
Test the station to determine the cause and replace sensor eyes if required.
1. Disconnect the plug from the battery to the circuit board of the problem
valve. Disconnect the plug from the battery to the circuit board of an
adjacent valve.
2. Connect the sensor cable from the adjacent working valve to the problem
valve. Activate the problem station’s sensor. The station should turn on.
If the adjacent station turns on, and cycles normally, replace the sensor eyes.
Faulty solenoid valve.
Test the station to determine the cause and replace solenoid valve if required.
1. Remove the screw, circuit board and standoff from the problem valve.
Remove the battery holder.
2. With a good working battery, briefly contact the solenoid valve directly
with the battery. The contact should cause the valve to open. With the
battery holder removed, briefly contact the solenoid valve with the battery
in the position shown. This should cause the valve to close. If the valve
does not operate when directly contacted with a good battery, and the
solenoid valve has already been cleaned as outlined at the beginning of this
troubleshooting section, replace the solenoid valve.
If problems persist:
Pass your hand in front of the problem station, while at the same time looking to
see if the indicator light on the circuit board flashes (the indicator light is located
near the hole in the circuit board where the standoff is mounted). If it does not
flash, and the battery and sensor eyes have already been tested as outlined above,
the problem may be with the circuit board. Make a note of the numbers printed on
the circuit board, then contact your Bradley representative for assistance.
WARNING Turn off water supplies to the unit before troubleshooting.
CLOSED
VALVE
OPEN
VALVE