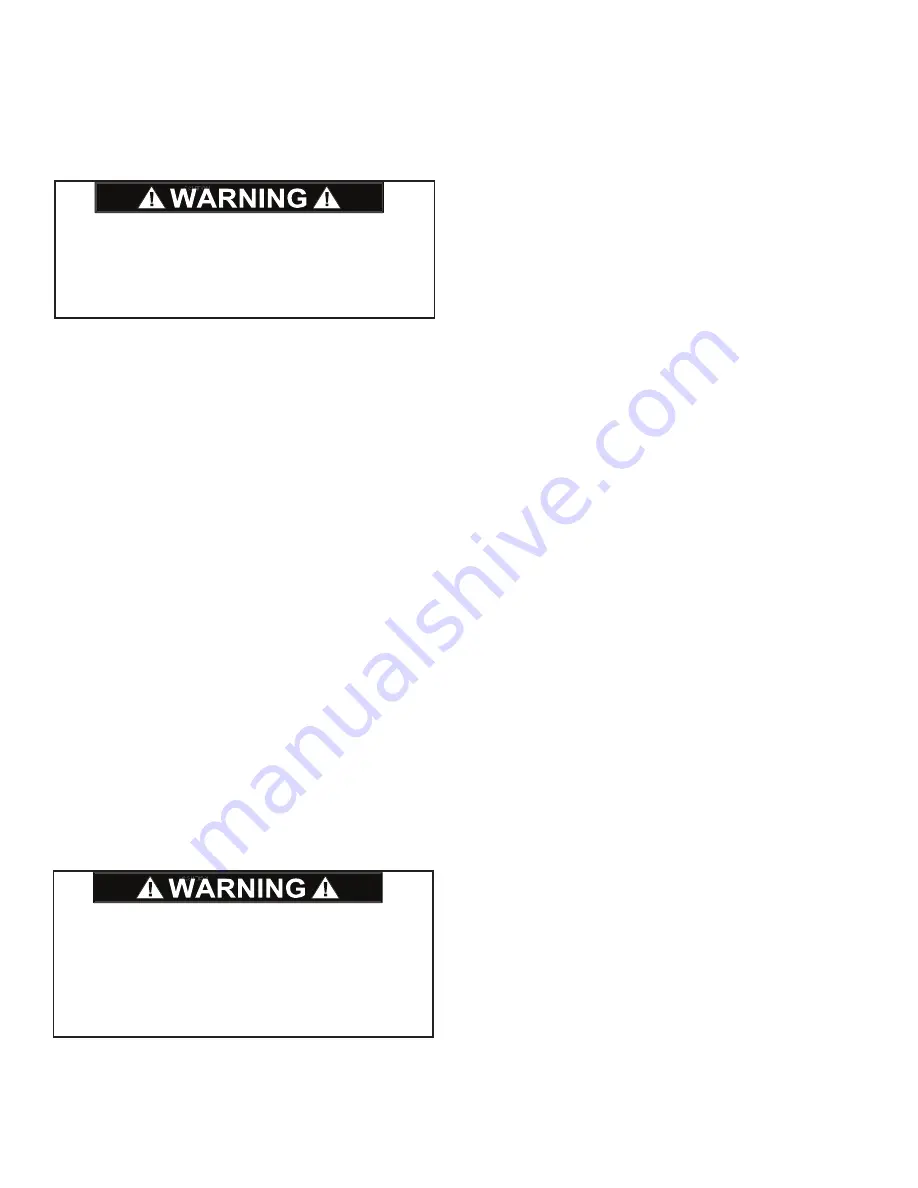
8
HOIST INSTALLATION
GENERAL REQUIREMENTS
1. The hoist should be mounted with the centerline of the
drum in a horizontal position. The mounting plane can
be rotated to any position around this centerline.
2. When mounting the CH210A hoist, BRADEN recom-
mends using 4 one-inch Grade 8 bolts and nuts, using
both mounting holes in each end plate. The CH280A
requires 1-1/4-inch bolts because the side plate hole is
1-3/8 inches.
3. It is important that the hoist be mounted on a surface
that will not flex when the hoist is in use, because this
could bind the working parts of the hoist. Also, be sure
the hoist is mounted on a flat surface. If necessary, use
shim stock to ensure proper mounting. The mounting
surface should be flat within ±0.020 inch (0.5 mm).
4. Hydraulic lines and components that operate the hoist
should be of sufficient size to assure minimum back
pressure at the hoist. The gear motor manufacturer
recommends that the back pressure not exceed 100
PSI for maximum motor seal life. 150 PSI is the maxi-
mum allowable back pressure. The standard CH210A/
CH280 hoist is supplied with the motor internally
drained. If high back pressures are encountered, the
motor can be drained directly to tank to improve motor
seal life. To ensure adequate static brake load holding
ability, back pressure on the hoist should not exceed
150 PSI. For pressures exceeding 150 PSI, consult
BRADEN Engineering. For piston motors, the back
pressure must be 30 PSI.
5. Make certain that the hoist drum is centered behind the
first sheave and the fleet angle does not exceed 1.5
degrees. The hoist should also be mounted perpen-
dicular to an imaginary line from the center of the drum
to the first sheave to ensure even spooling.
6. The hoist directional control valve must be a three-
position, four-way valve with a motor spool such that
when the valve is in the center position both work ports
are opened directly to tank.
7. The hydraulic oil filter should have a 10-micron nomi
-
nal rating and be a full-flow type.
8. High-quality hydraulic oil is essential for satisfactory
performance and long hydraulic system component life.
Oil having 150 to 330 SUS viscosity at 100°F (38°C)
and viscosity index of 100 or greater will give good re-
sults under normal temperature conditions. The use of
an oil having a high viscosity index will minimize cold-
start trouble and reduce the length of warm-up periods.
A high viscosity index will minimize changes in viscos-
ity with corresponding changes in temperature.
Maximum cold weather start-up viscosity should not
exceed 5,000 SUS with a pour point at least 20°F (7°C)
lower than the minimum temperature.
Under continuous operating conditions, the tempera-
ture of the oil at any point in the system must not ex-
ceed 180°F (82°C). A temperature between 120–140°F
(49–60°C) is generally considered optimum.
In general terms: For continuous operation at ambi-
ent temperatures between 50–110°F (10–43°C), use
SAE 20W. For continuous operation between 10–90°F
(50–32°C), use SAE 10W. For applications colder than
10°F (12°C), contact the BRADEN Service Depart-
ment. The use of multiviscosity oils is generally not
recommended.
DO NOT weld hoist to mounting surface. Welding may not
provide adequate structural support for hoist loads. This
may cause loss of load control, which could result in prop-
erty damage, injury, or death. Welding may also damage
bearings and seals, resulting in premature failure.
WIRE ROPE INSTALLATION
The wedge and anchor pocket must be clean and dry. The
end of the wire rope being anchored to the drum must be
clean and dry and not frayed. Anything on the end of the
wire rope to keep it from fraying (tape or wire) must not
be in contact with the wedge when the installation is com-
plete. Consult the wire rope manufacturer on the proper
treatment of the dead end of the wire rope. Some rope
manufacturers recommend when using rotation-resistant
wire rope, that the rope end be seized, welded, or brazed
before inserting the wire rope into the wedge socket. This
prevents core slippage or loss of rope lay.
Take the free end of the wire rope and insert it through the
small opening on the cable drum. Loop the wire rope and
push the free end about 3/4 of the way back through the
pocket. Install the wedge as shown in Figure 7, then pull
the slack out of the wire rope. The dead end of the rope
needs to extend slightly beyond the end of the wedge as
shown in Figure 8.
THE CABLE ANCHORS ALONE ON HOISTS ARE
NOT DESIGNED TO HOLD RATED LOADS.
Hoist
loads applied directly to the wire rope anchor may
cause the wire rope to pull free and result in the sudden
loss of load control and cause property damage, injury,
or death. A minimum of 5 wraps of wire rope must be left
on the drum barrel to achieve rated load.