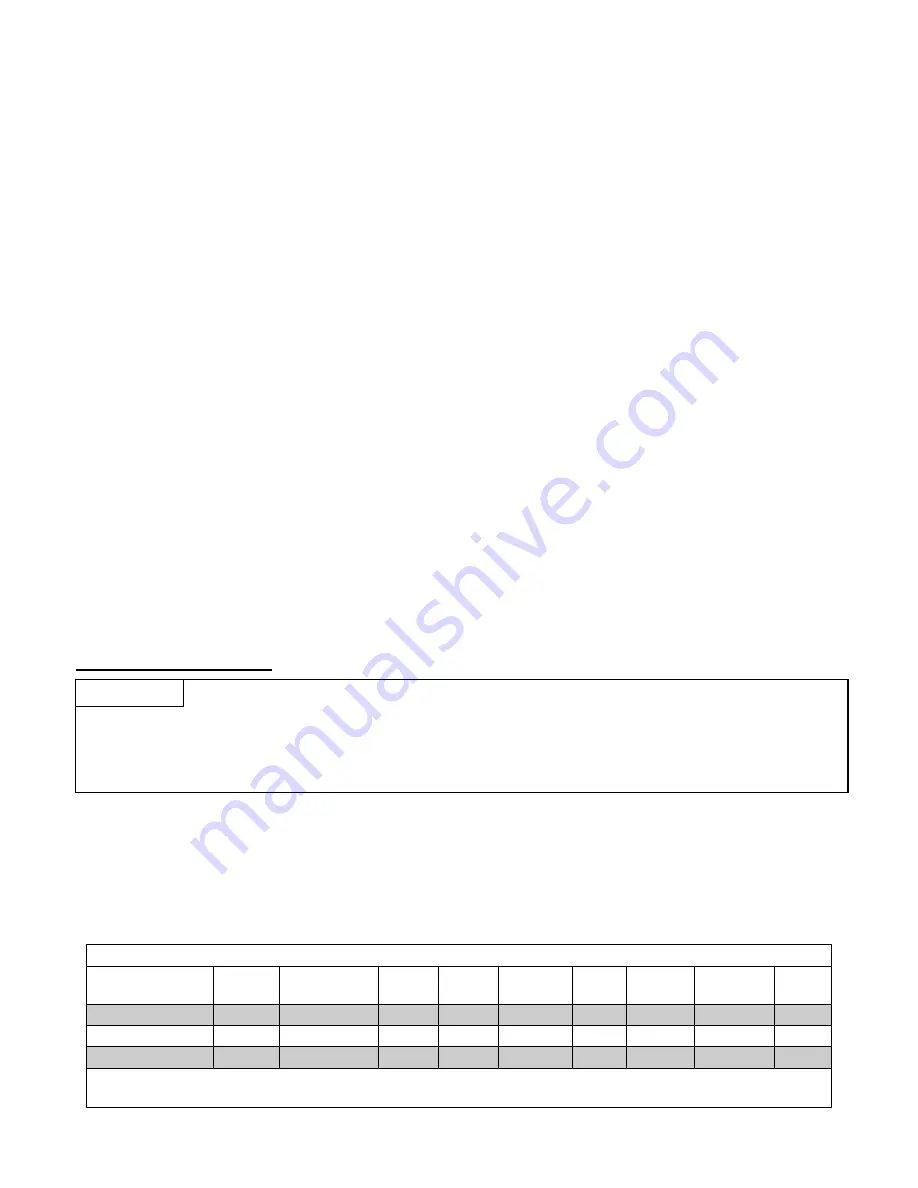
15
safely. The furnace room must be well ventilated to allow sufficient make-up air to support
combustion.
Inadequate combustion air may result in erratic operation of the burner, noisy combustion or fuel
odors in the air. NEVER BLOCK THE FURNACE FROM THE SUPPLY OF COMBUSTION AIR.
Remember, your need for outside air will be greatly increased if you have a vented dryer in the
basement or other venting fans in the home. Do not install an exhaust fan in the same room as the
furnace.
In unconfined spaces in buildings of conventional construction, infiltration is adequate to provide air
for ventilation and combustion. If the unconfined space is within a building having insufficient air
because of tight construction, the air required for combustion and ventilation shall be obtained from
outdoors or from spaces freely communicating with the outdoors. In this situation, permanent
openings having a total free opening area of not less than 1 square inch per 5000Btu/Hr of total input
of all appliances must be provided.
If the furnace is located in a confined space (A space whose volume is less than 50 cubic feet per
1000Btu/Hr of the combined input ratings of all appliances installed in that space) the confined space
shall have two permanent openings, one 6 inches from the top of the space and one 6 inches from the
bottom of the space. Each opening shall have a free area opening of not less than 1 square inch per
1000Btu/Hr of total input rating of all appliances in the enclosure freely communicating with interior
areas having adequate infiltration with the outside.
If adequate infiltration air is not available the confined space shall be fitted with two openings, one 6
inches from the top of the enclosure and one 6 inches from the bottom of the enclosure. Each opening
shall have a free area of at least 1 square inch per 2000Btu/Hr of the total input of the appliances in
the enclosure.
In calculating free area, consideration must be given to the blocking effect of louvers, screens or grills
protesting the opening. Screens used shall not be less than ¼” mesh and shall be readily accessible for
cleaning.
Burner Installation
Remove the oil burner from its shipping carton and inspect thoroughly. Verify that the
correct burner combination and nozzle is installed in the burner as shipped.
Read the oil burner manual included in the shipping carton and follow the instructions for preparing
and installing the burner. Refer to the tables for the burner specifications for your unit.
On units which can be multi fired, a nozzle change may be required. Follow the oil burner manuals
instructions for the proper installation of the nozzle.
Verify that the electrode settings match the manufacturers recommended settings.
The oil burner is to be bolted to the front plate in the proper rotation using the burner mounting flange
gasket and the nuts supplied. Refer to the wiring section of this manual for the correct wiring
connections to the furnace and to the oil burner manual for fuel piping.
Table 9 Beckett Burner Specifications
Furnace Model
Burner
Model
Delavan
Nozzle
Pump
Press.
Air
Band
1
Air
Shutter
1
Head Tube
Length
Insertion Static
Plate
RSM 500
AFG
3
0.40X60
º
W
175
0
5
L2
9”
4-1/4”
3-3/8
RSM 600
AFG
3
0.50X60
º
W
150 0 7 L2
9” 4-1/4”
3-3/8
RSM 750
AFG
3
0.60X60
º
B
150
2
10
L2
9”
4-1/4”
3-3/8
Notes: 1. Approximate air settings, see start up procedures for final adjustments.
2. Stainless Air Tube. 3. Low Firing Rate Baffle installed.
NOTICE
Summary of Contents for RSM 500
Page 20: ...20 Furnace Wiring PSC Motors ...