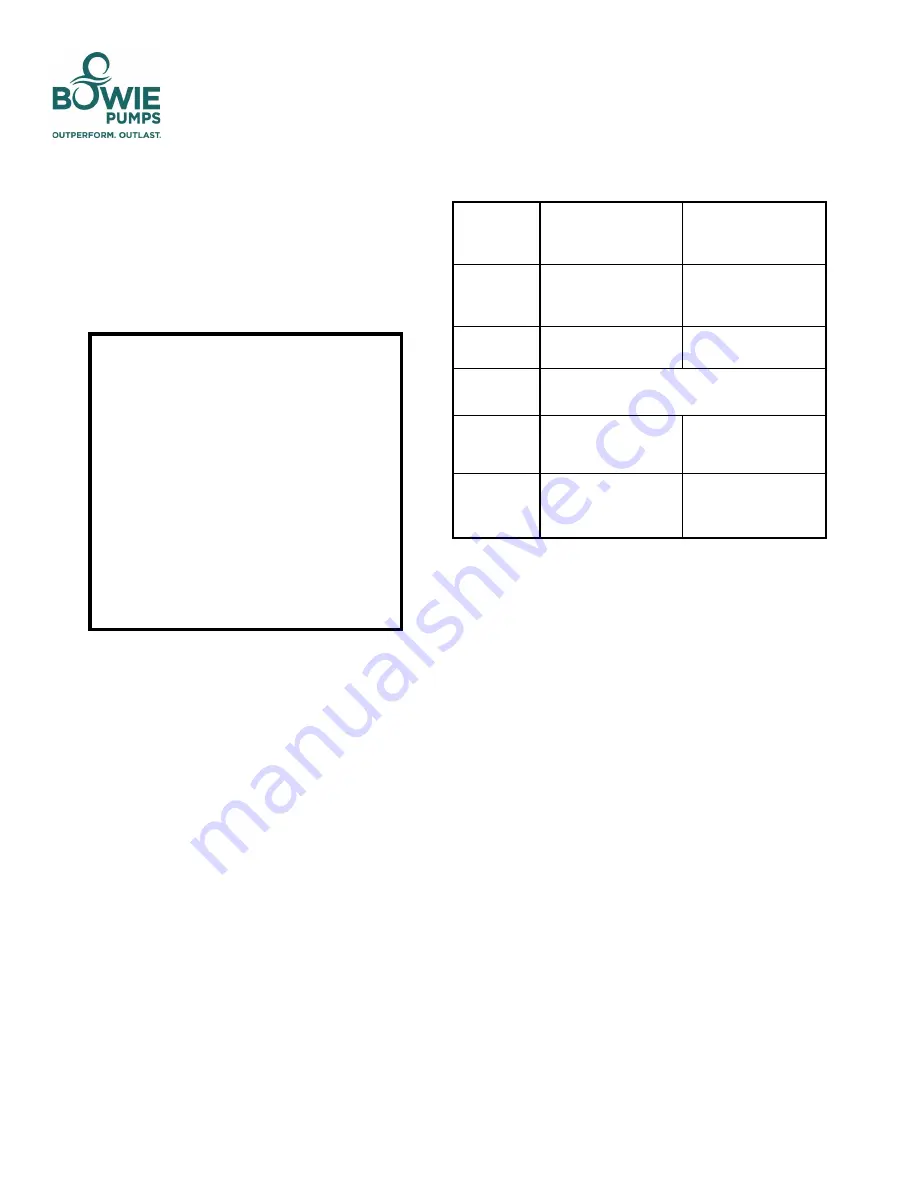
ES IOM Rev 1
-
5/13/2021
2
PUMP IDENTIFICATION
Pump serial number and model designation will be sup-
plied with each pump. It is recommended that this data
be recorded and filed for future reference. This data
should be supplied to a Bowie representative when re-
placement parts, repair work, or information pertaining
to the pump is required.
PUMP DATA
PUMP INFORMATION
Model No.: _____________________
Serial No.: _____________________
Date of Installation: _____________
PUMP DESCRIPTION
Eco
-
Seal pumps are based on our industry leading Signature Series of pumps but with one major difference:
the pumps are
engineered with a high performance lip sealing system for enhanced leak protection.
The result:
an affordable, long lasting,
low maintenance bushing
-
design pump which meets more stringent environmental and safety standards.
There are three lines of Eco
-
Seal Series pumps:
300 Eco
-
Seal –
the standard pump; 300 Eco
-
Seal S –
short drive neck for ac-
cess in tight spaces; 300 Eco
-
Seal ED –
extended duty.
PUMP DIMENSIONS, EXPLODED VIEWS, AND OTHER TECHNICAL INFORMATION
All technical information, including pump dimensional diagrams, exploded views with part listings, and other technical information
are available at www.bowiepumps.com.
Noise levels for all pumps will not exceed 95dB at a distance of one
meter from the pump.
TECHNICAL DATA
* Pressures must be measured no farther than
6”
from the discharge port.
Maximum operating limits are dependent on the materials of construction and
application design requirements.
Operating
Criteria
Buna
-
N
Rubber Gears
Progressive Helical Steel
Gears
Maximum
Operating
Temperature*
70°C
160°C
Maximum
Speed*
500 RPM
750 RPM
Maximum
Viscosity*
60000 SSU
Maximum
Differential
Pressure*
125 psi
150 psi
Maximum
Working
Pressure*
125 psi
150 psi