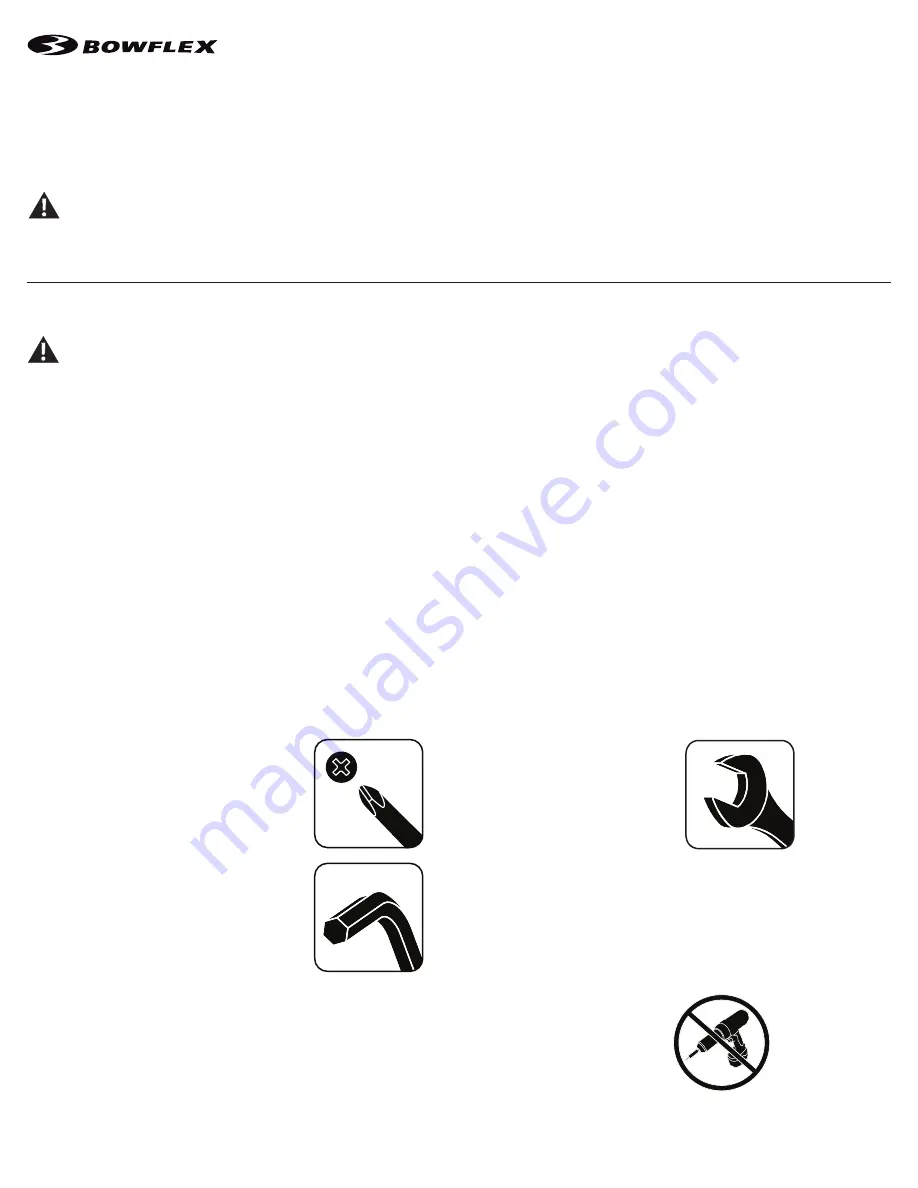
40
Tools Required (not included)
#2
Phillips
screwdriver
8mm
wrench
10mm
wrench
2.5mm hex wrench
Tape, any type (only used as a place holder)
Replace the Brake Assembly on the
Bowflex
™
Max Total
™
machine / Max Total
™
16/40 / Max Trainer
™
M9
Skill Level: II
8023623.071522.D
Replacement Procedure
NOTICE:
This document provides instructions for the replacement of the Brake Assembly on the Bowflex™ Max Total™ machine / Max Total™ 16/40 / Max
Trainer™ M9
.
If you need assistance, please contact Customer Service (if purchased in US/Canada) or your local distributor (if purchased outside US/Canada). To find your local
distributor, go to: www.nautilusinternational.com
This icon means a potentially hazardous situation which, if not avoided, could result in death or serious injury. Read and understand all
Warnings on this machine.
™
™
Important Safety Instructions - Before servicing or using this equipment, obey the following warnings:
This icon means a potentially hazardous situation which, if not avoided, could result in death or serious injury. Read and under-
stand all Warnings on this machine.
• Read and understand the Part Replacement Procedure before working on the machine. Failure to obey the instructions and safety warnings could cause
injury to the service technician or bystanders.
• Keep bystanders, children and pets away from the product being serviced at all times.
• Make sure that the repair is done in an appropriate work space away from foot traffic and exposure to bystanders.
• Disconnect all power and allow to sit for 5 minutes before you service this machine.
• Some components of the equipment can be heavy or awkward. Enlist the service of a second person when you do maintenance steps involving these
components. Do not try to do heavy or awkward steps on your own.
• If replacement parts are necessary, use only genuine Nautilus replacement parts and hardware. Failure to use genuine replacement parts can cause a
risk to users, keep the machine from operating correctly and will void the warranty.
• Be sure that all warning stickers and instructional placards applied to the product stay present and in good condition when doing maintenance or
replacing components. If at any time the Warning labels become loose, unreadable or dislodged, replace the labels. If purchased in US/Canada, contact
Customer Service for replacement labels. If purchased outside US/Canada, contact your local distributor for them.
• Do not try to change the design or functionality of the machine being serviced as this can adversely effect user safety and will void the warranty.
• Do not use the machine until all shrouds, instructions, warning labels and correct functionality have been verified and tested for correct performance.
•
SAVE THESE INSTRUCTIONS.
Nautilus, Inc., www.NautilusInc.com, 5415 Centerpoint Parkway, Groveport, OH 43125 U.S.A. - Customer Service: North America (800) 605-3369, [email protected] | outside U.S. www.nautilusinternational.com | Printed
in China | © 2019 Nautilus, Inc. | Bowflex, the B logo, Max Total, and Max Trainer are trademarks owned or licensed by Nautilus, Inc., registered or otherwise protected by common law in the United States and other nations. |
ORIGINAL DOCUMENT - ENGLISH VERSION ONLY