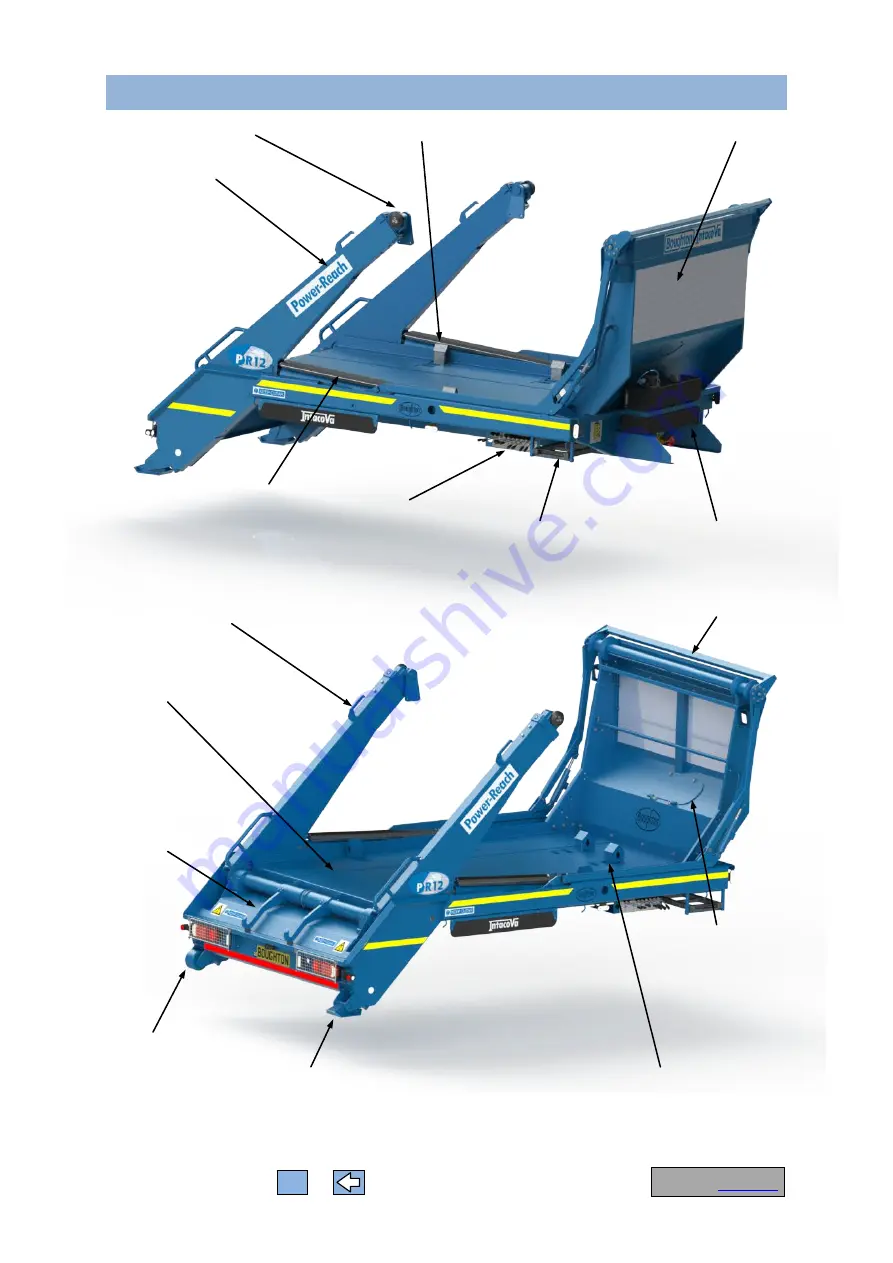
5.
Previous Page – Press
+
Alt
2. Skiploader General Arrangement
* All skiploaders will have flat feet (Pad) rear stabilisers fitted unless the chassis is fitted with front axle
parking brakes, in which case, roller stabilisers can be fitted
Access Cover
Main Control
Valve Block
Hydraulic Fluid Tank
Intacova Sheeting System
(Optional)
Telescopic Lifting Arm
Main Lifting Arm
Stabiliser – Option Roller*
Access Ladder (Both Sides)
Lift Chain Stowage
Tiphooks
Adjustable Skip Stops - Front
Adjustable Skip Stops - Lateral
Main Lift Arm Hydraulic
Cylinder
Cab Guard
Load Bed
Stabiliser – Option Pad*