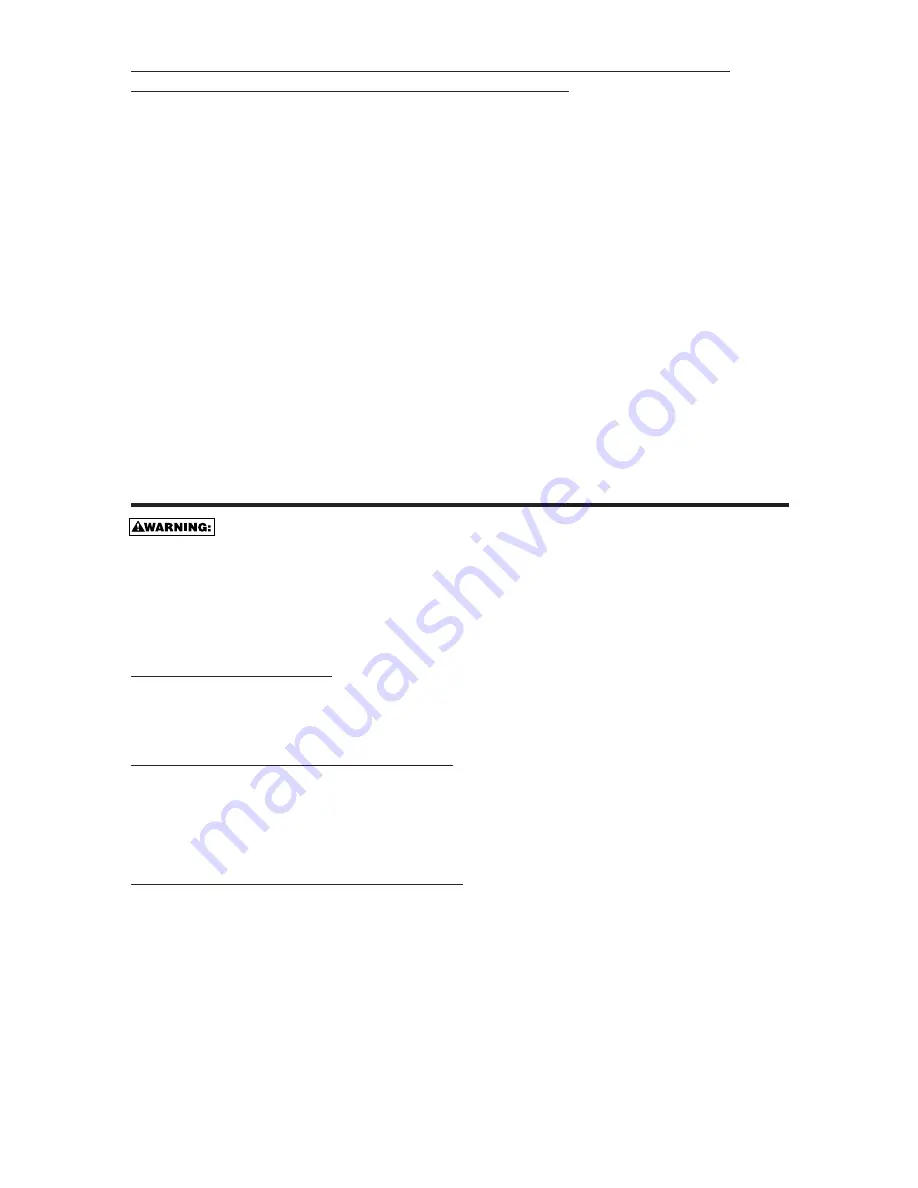
IN ADDITION TO THE OTHER WARNINGS CONTAINED IN THIS MANUAL
OBSERVE THE FOLLOWING FOR SAFE OPERATION
• Use the BOSTITCH pneumatic tool only for the purpose for which it was designed.
• Never use this tool in a manner that could cause a fastener to be directed toward the user
or others in the work area.
• Do not use the tool as a hammer.
• Always carry the tool by the handle. Never carry the tool by the air hose.
• Do not alter or modify this tool from the original design or function without approval
from BOSTITCH
• Always be aware that misuse and improper handling of this tool can cause injury to
yourself and others.
• Never clamp or tape the trigger or contact trip in an actuated position.
• Never leave a tool unattended with the air hose attached.
• Do not operate this tool if it does not contain a legible WARNING LABEL.
• Do not continue to use a tool that leaks air or does not function properly. Notify your
nearest BOSTITCH representative if your tool continues to experience functional problems.
-7-
MAINTAINING THE PNEUMATIC TOOL
When working on air tools, note the warnings in this manual and use extra care evaluating
problem tools.
CAUTION: Pusher spring (constant force spring). Caution must be used when working with the
spring assembly. The spring is wrapped around, but not attached to, a roller. If the spring is extended
beyond its length, the end will come off the roller and the spring will roll up with a snap, with a chance
of pinching your hand. Also the edges of the spring are very thin and could cut. Care must also be
taken to insure no permanent kinks are put in the spring as this will reduce the springs force.
REPLACEMENT PARTS:
BOSTITCH replacement parts are recommended. Do not use modified parts or parts which will not give
equivalent performance to the original equipment.
ASSEMBLY PROCEDURE FOR SEALS:
When repairing a tool, make sure the internal parts are clean and lubricated. Use Parker “O”-LUBE or
equivalent on all “O”-rings. Coat each “O”-ring with “O”-LUBE before assembling. Use a small amount of oil
on all moving surfaces and pivots. After reassembly add a few drops of BOSTITCH Air Tool Lubricant
through the air line fitting before testing.
AIR SUPPLY-PRESSURE AND VOLUME:
Air volume is as important as air pressure. The air volume supplied to the tool may be inadequate because
of undersize fittings and hoses, or from the effects of dirt and water in the system. Restricted air flow will
prevent the tool from receiving an adequate volume of air, even though the pressure reading is high. The
results will be slow operation, misfeeds or reduced driving power. Before evaluating tool problems for these
symptoms, trace the air supply from the tool to the supply source for restrictive connectors, swivel fittings,
low points containing water and anything else that would prevent full volume flow of air to the tool.