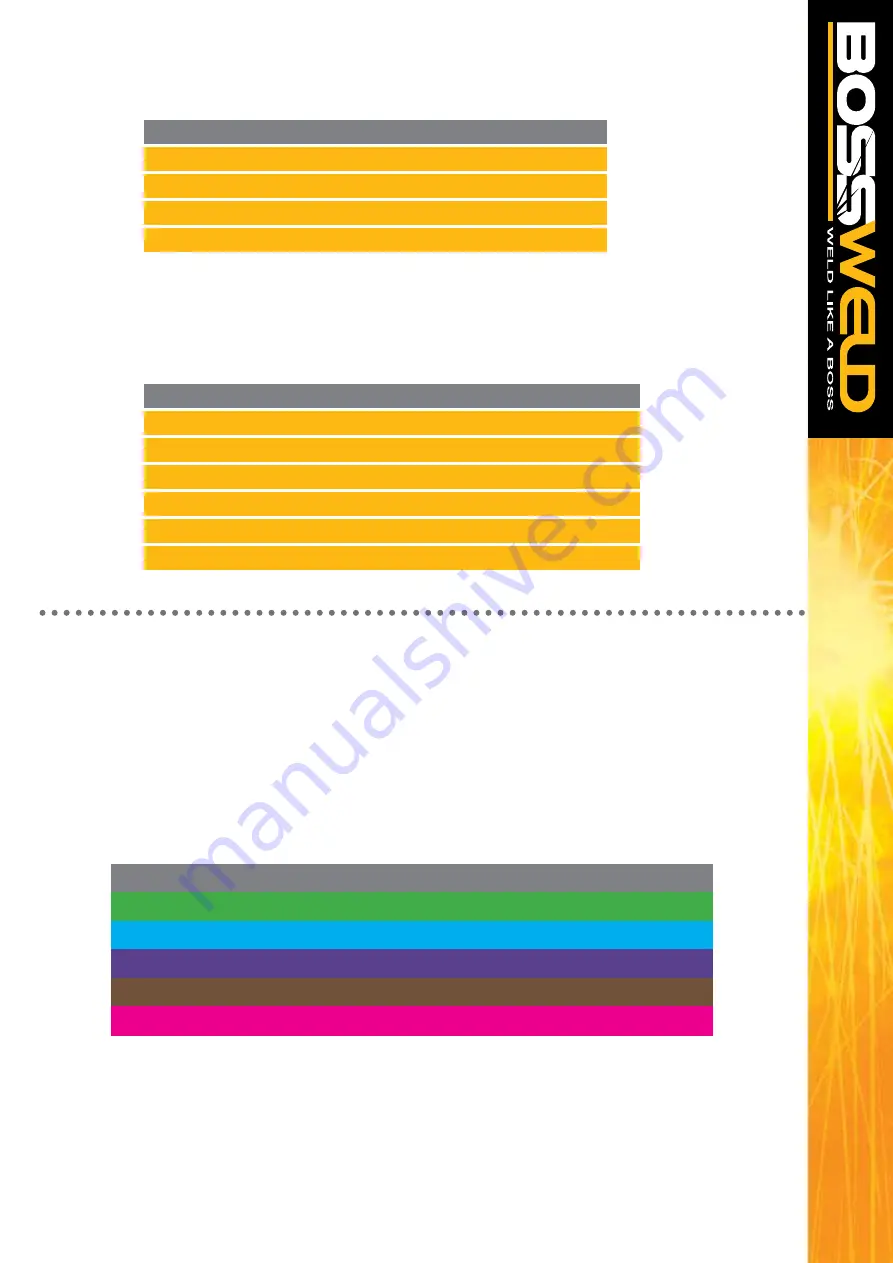
13
Amperage Selection Guide
Rod Size/ Gauge
Welding Current
1.6mm
40-50 Amps
2.0mm
50-75 Amps
2.5mm
75-105 Amps
3.2mm
105-140 Amps
4.0mm
140-160 Amps
WELDING CURRENT
Welding current level is determined by the size of electrode - the normal operating range and current are
recommended by manufacturers. Typical operating ranges for a selection of electrode sizes are illustrated in
the table. As a rule of thumb when selecting a suitable current level, an electrode will require about 40 Amps
per millimeter (diameter). Therefore, the preferred current level for a 4mm diameter electrode would be 160
Amps, but the acceptable operating range is 140 to 180 Amps. It is important to match the machine to the job
Average Metal Thickness
Electrode Size
1.0 - 2.0mm
2.0mm
2.0 - 5.0mm
2.6mm
5.0 - 8mm
3.2mm
8.0mm +
4.0mm
ELECTRODE SIZE SELECTION
Electrode size selection will be determined by the thickness of the section being welded. A thicker section will
need a larger diameter electrode. The table below shows the maximum size of electrodes for average
thicknesses of section (based on General Purpose 6013 Electrode).
MANUAL METAL ARC PROCESS (MMA WELDING)
When an arc is struck between the metal rod (electrode) and the workpiece, both the rod and workpiece
surface melt to form a weld pool. Simultaneous melting of the flux coating on the rod will form gas and slag
which protects the weld pool from the surrounding atmosphere. The slag will solidify and cool and must be
chipped off the weld bead once the weld run is complete (or before the next weld pass is deposited).
The process allows only short lengths of weld to be produced before a new electrode needs to be inserted in
the holder. Weld penetration is low and the quality of the weld deposit is highly dependent on the
skill of the welder.
TYPES OF ELECTRODES
Arc stability, depth of penetration, metal deposition rate and positional capability are greatly influenced by the
chemical composition of the flux coating on the electrode. There are many types of Electrodes, and these
are generally matched to the base metal. For example if welding Mild Steel then select a Mild Steel (General
Purpose Electrode). Electrodes are identified by a universal numbering system (AWS Type code).
Electrodes are often packed in sealed packaging to keep moisture out. However, if a pack has been opened
or damaged, it is essential that the electrodes are redried according to the manufacturer’s instructions.
ARC FORCE
Also called Dig and Arc Control. Gives a power source variable additional amperage during low voltage
(short arc length) conditions while welding. Helps avoid “sticking” stick electrodes when a short arc
length is used.
POWER SOURCE
Electrodes can be operated with AC and DC power supplies. Not all DC electrodes can be operated on AC
power sources; however AC electrodes may be used on either AC or DC
Base Metal
Electrode Type
Type
Mild Steel
Mild Steel General Purpose
6013
Stainless Steel
Stainless Steel 316L
316L
Dissimilar Metals
Dissimilar 680
312
Cast Iron
Nickel Arc 98
Ni99
High Strength Steel
Low Hydrogen
TC16