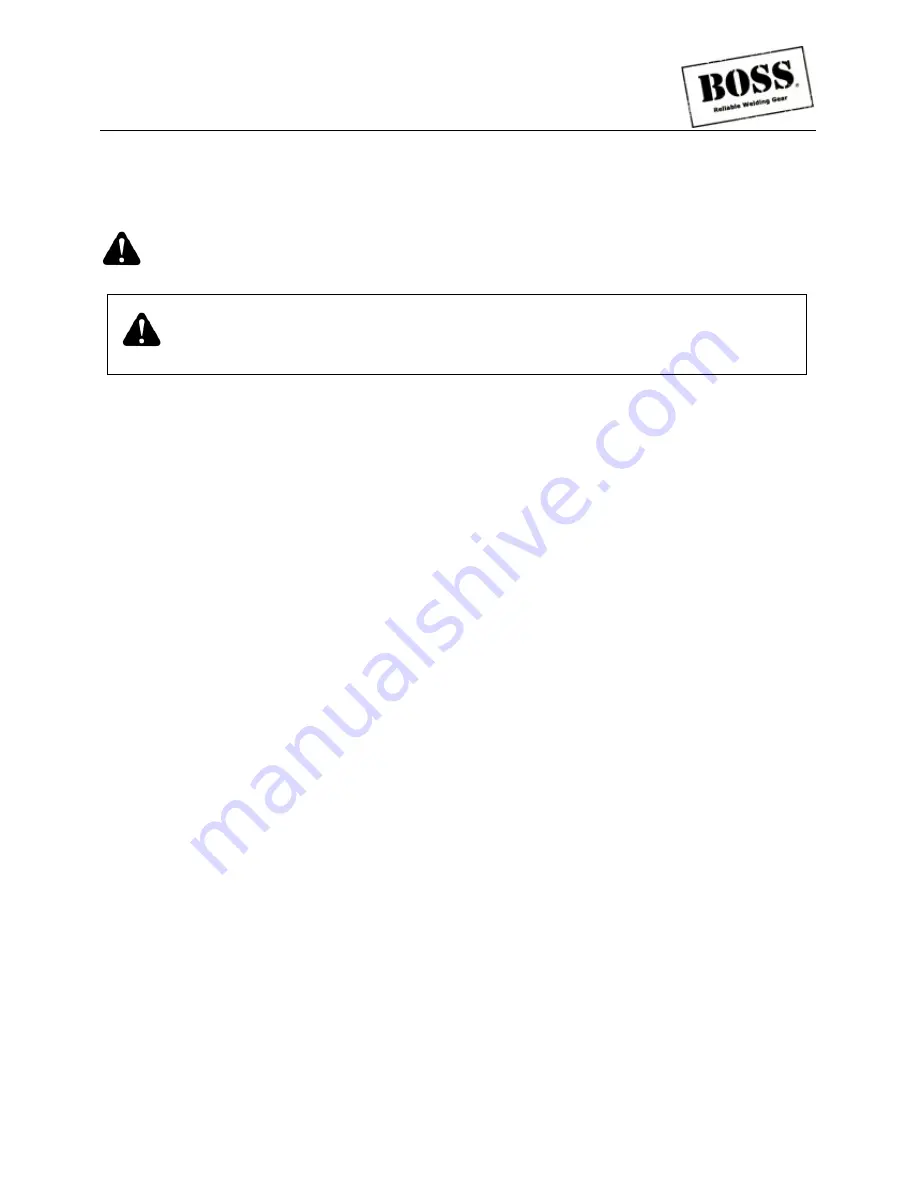
- 6 -
BOSS Inverter Mig 250 Operating Manual
1.03 Transporting methods
These units are equipped with a handle for carrying purposes.
WARNING: ELECTRIC SHOCK can kill.
DO NOT TOUCH live electrical parts. Disconnect input power conductors from de-energized supply
line before moving the welding power source.
WARNING:
FALLING EQUIPMENT can cause serious personal injury and
equipment damage.
l
Lift unit with handle on top of case.
l
Use handcart or similar device of adequate capacity.
l
If using a fork lift vehicle, place and secure unit on a proper skid before transporting.