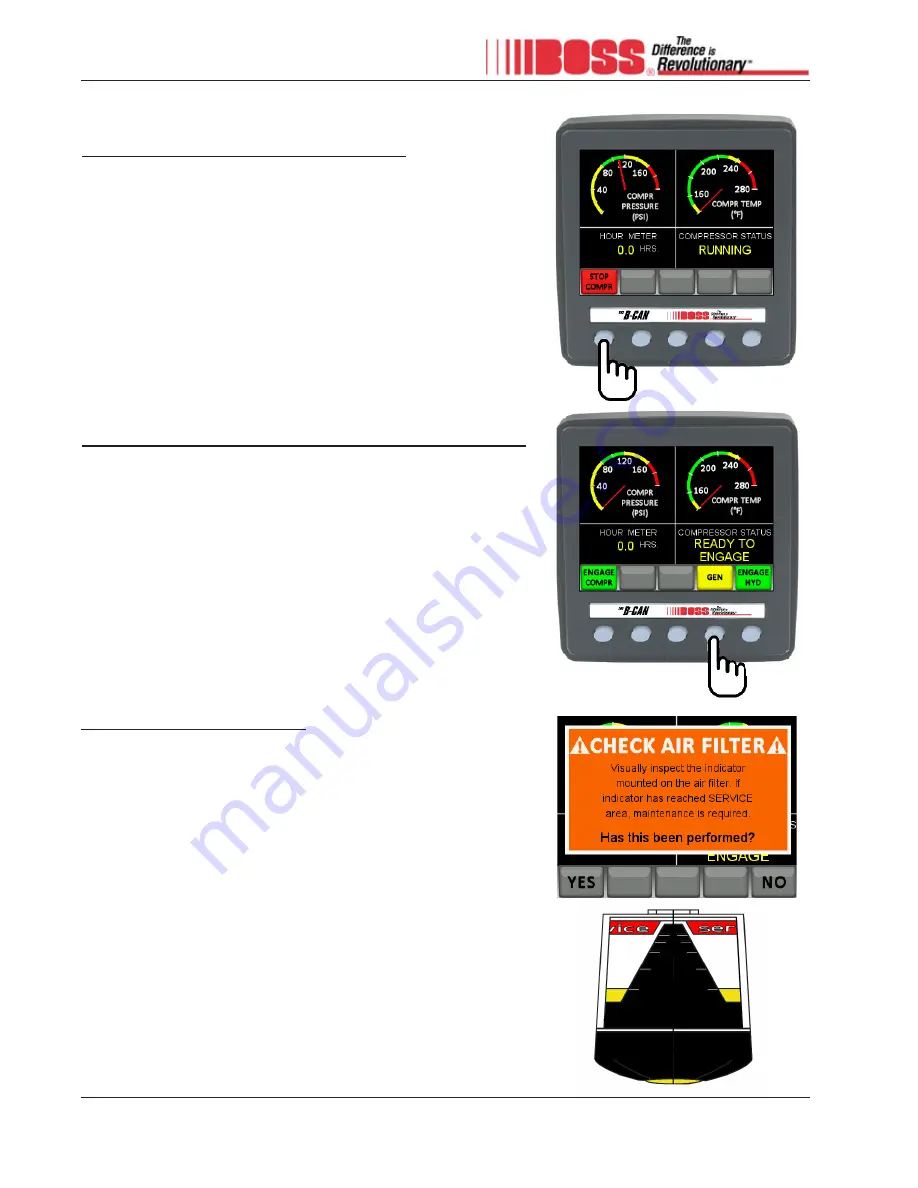
22
309743
Operation
Stopping the Compressor System
The following steps are for the routine shutdown of the 8060 UBI PTO
compressor system. This process is in addition to any company policies
and procedures.
1. Ensure all service valves are closed.
2. Press the red STOP COMPR button and the compressor system
will disengage. The compressor will begin blowing down
(releasing pressure). It will take approximately 30-60 seconds
until the compressor can be reengaged.
3. Check B-CAN for any warnings (third button label will be
flashing) and alert service personnel if any exist.
Operating Multiple Components (if equipped)
Operation of additional components is very similar to that of the compressor.
The second component will use the fifth button for control. If a third
component is installed, it will use the fourth button. The colors used for the
button will be the same as for the compressor. If the additional component is
gearbox or belt driven, the compressor must be engaged before the addi-
tional component will engage. If it has a separate PTO drive, it can be run
separately from the compressor. Follow on-screen instructions for starting
ancillary equipment controlled by the B-CAN.
Checking the Air Filter
Because the life of the Air Filter is dependent on the operating environment,
the B-CAN requires the operator to visually inspect the air filter service
indicator. After every 25 hours of compressor operation, the B-CAN will
prompt you to check the air filter indicator. If you are unable to locate the air
filter indicator, consult your service personnel for instructions on performing
this check. The procedure for checking the air filter is listed below:
1. Locate the air filter and check the indicator to see if the yellow
indicator section has reached the red SERVICE area.
2. If it has reached the red SERVICE area, notify your service
personnel for filter replacement.
3. After checking the indicator, select the YES button on the B-
CAN to hide the notification for another 25 hours.
4. Since the air filter element will have a service life that is heavily
based on the environment, the B-CAN notification is simply a
reminder to check the filter indicator. For this reason, the
decision to replace the air filter element should be based on the
filter indicator, not on the B-CAN notification.
Summary of Contents for 8060 UBI
Page 2: ...309743 ...
Page 5: ...5 309743 Safety Safety ...
Page 12: ...12 309743 Safety ...
Page 13: ...13 309743 Welcome Welcome ...
Page 15: ...15 309743 Description of Components Description of Components ...
Page 19: ...19 309743 Operation Operation ...
Page 26: ...26 309743 Operation ...
Page 27: ...27 309743 B CAN B CAN ...
Page 33: ...33 309743 Maintenance Maintenance ...
Page 38: ...38 309743 Maintenance ...
Page 39: ...39 309743 Warranty Warranty ...
Page 57: ...57 309743 5 4 3 5 6 1 2 7 8 OPTIONAL MOUNTING CONFIGURATIONS Drawings B CANAssembly cont ...
Page 59: ...59 309743 5 4 4 7 3 1 2 6 9 8 9 Drawings AirFilterAssembly cont ...
Page 67: ...67 309743 Drawings 10G RSC9 CoolerAssembly cont 10 6 1 7 5 6 5 8 4 5 11 9 2 3 ...
Page 69: ...69 309743 Drawings 14D CoolerAssembly cont 6 6 5 4 11 10 8 9 7 5 5 2 1 3 ...