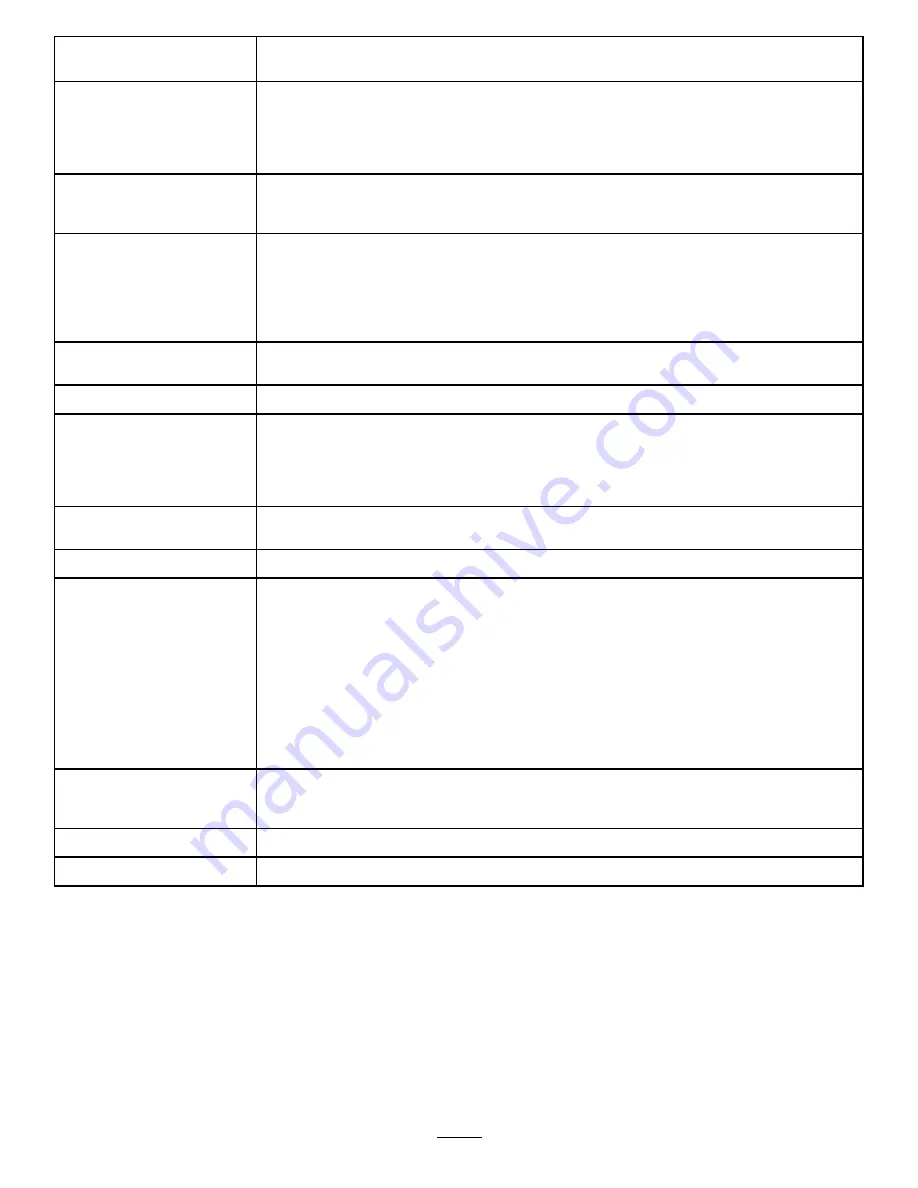
Maintenance Service
Interval
Maintenance Procedure
Before each use or daily
• Inspect the air-cleaner elements.
• Check the engine-oil level.
• Check the kill cord and operator presence sensor.
• Check the hydraulic-fluid level.
• Check the cutting edge for wear.
After each use
• Empty the sprayer tank.
• Flush the sprayer system.
• Condition the sprayer system.
Every 40 hours
• Check the hydraulic hoses and fittings for leaks.
• Check the sprayer hoses and fittings for leaks.
• Check the spray gun for leaks or clogging.
• Check the in-line filter screen for clogging.
• Check the in-line filter rubber seal.
• Check the spray nozzle screens for clogging.
Every 50 hours
• Clean the air-cleaner elements.
• Check the tire pressure.
Every 80 hours
• Check the spray nozzle tips.
Every 100 hours
• Change the engine oil.
• Check the spark plug.
• Clean the fuel tank and filter.
• Clean the sediment cup.
• Check the battery.
Every 300 hours
• Replace the paper air-cleaner element.
• Replace the spark plug.
Every 500 hours
• Change the hydraulic filters and hydraulic fluid.
Before storage
• Grease the machine.
• Service the air cleaner.
• Change the engine oil.
• Check the spark plug.
• Check the tire pressure.
• Check and tighten all fasteners.
• Lightly sand and use touch-up paint on painted areas that are scratched, chipped,
or rusted.
• Loosen the trip-return springs.
• Condition the sprayer system.
• Close the fuel-shutoff valve.
Monthly
• Check the wheel-lug nuts.
• Check the hub castle-nut cotter pin.
• Check the sprayer valve.
Yearly
• Grease the motion controls.
Yearly or before storage
• Clean the fuel sediment cup.
Important:
Refer to your engine owner’s manual for additional maintenance procedures.
26
Summary of Contents for Snowrator SNR24001
Page 24: ...g294661 g294662 Figure 29 1 Front tie down point left side shown 2 Rear tie down points 24...
Page 45: ...Notes...
Page 46: ...Notes...
Page 48: ......