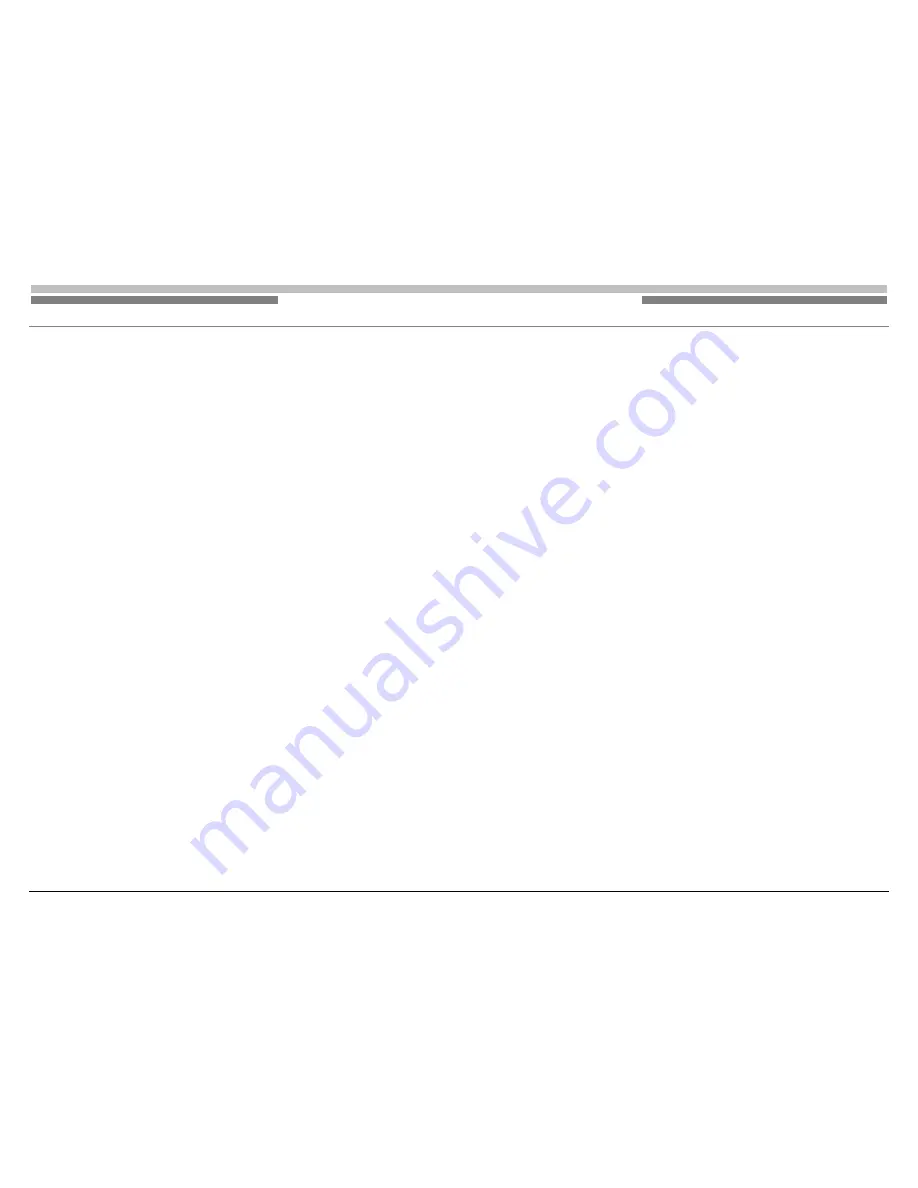
W
W
W
T
T
T
V
V
V
C
C
C
G
G
G
A
A
A
S
S
S
D
D
D
R
R
R
Y
Y
Y
E
E
E
R
R
R
R
R
R
E
E
E
P
P
P
A
A
A
I
I
I
R
R
R
I
I
I
N
N
N
S
S
S
T
T
T
R
R
R
U
U
U
C
C
C
T
T
T
I
I
I
O
O
O
N
N
N
1
SAFETY ........................................................ 2
2
INSTALLATION ............................................ 3
2.1
Basic installation ................................................................ 3
2.2
Exhaust vents...................................................................... 3
2.3
Feet (leveling legs).............................................................. 3
2.4
AQUASTOP
®
(aqua secure)................................................ 4
2.5
General installation warnings ............................................ 4
3
OPERATION ................................................. 5
3.1
Controls ............................................................................... 5
4
COMPONENTS............................................. 6
4.1
WTVC Gas Dryer Components .......................................... 6
4.2
Operation ........................................................................... 14
5
REPAIR....................................................... 15
5.1
Disassembly / Reassembly .............................................. 15
5.2
Kit Installation ................................................................... 25
5.3
Diagnosing (troubleshooting).......................................... 26
5.4
Dryer noise ........................................................................ 27
5.5
Customer diagnosing ....................................................... 27
5.6
Maintenance ...................................................................... 28
6
FAULT DIAGNOSTICS............................... 29
6.1
Overheating fault codes ................................................... 32
7
TECHNICAL SPECIFICATIONS ................ 33
7.1
Dryer ratings ..................................................................... 33
702_58300000143767_ara_en_a
Page 1 of 33