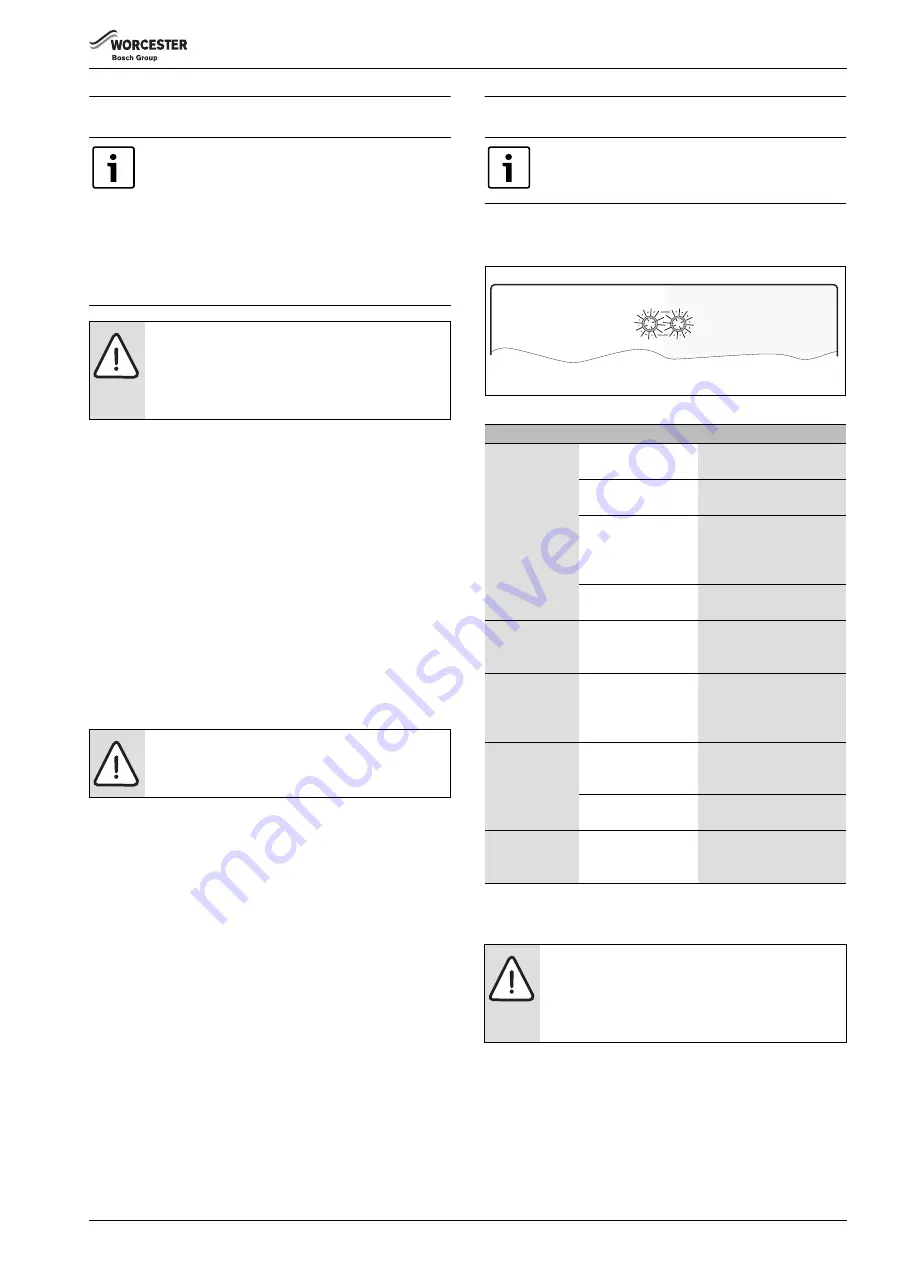
COMMISSIONING
6 720 804 107 (2012/10)
13
4
COMMISSIONING
CODE SWITCH I
The system type is set on the module using
code switch I
:
• Mid-position (Y-plan) system: code switch I set to
Y
• 2-port valve (S-plan) system: code switch I set to
S
• Three central heating circuits without electronic mixing valves:
– Module for heating circuits 1, 2 and 3 = set code switch I to
2
– Module for heating circuits 4, 5 and 6 = set code switch I to
3
• Two central heating circuits without electronic mixing valves and one
domestic hot water cylinder circuit:
– Module for heating circuit 2, 3 and domestic hot water cylinder
circuit (only one module is permissible in the system) = set code
switch I to
1
– Module for heating circuits 7, 8 and domestic hot water cylinder
circuit (one of a maximum of three modules in the system) = set
code switch I to
4
TEMPERATURE SWITCH II
The
target domestic hot water cylinder temperature
is adjusted at
the
temperature switch II
:
• The target domestic hot water cylinder temperature can be set in
increments of 5 °C between 40 °C and 70 °C: set temperature switch
to
40 to 70
as required by the customer.
• A maximum target domestic hot water cylinder temperature of 75 °C
is available: set temperature switch to
max
(two valid switch
positions)
SYSTEM AND MODULE COMMISSIONING
1. Set the system type for the module using the code switch
I
.
2. Set the cylinder temperature using temperature switch
II
.
-or-
Set temperature switch
II
to
off
3. If applicable, adjust the positions of code switch and temperature
switch at the other modules.
4. Switch on the power supply (230 V AC) of the entire system, the
Greenstar Wiring Centre and the boiler.
When the status indicator of module lights up green:
5. Commission and set up the boiler and control accessory in
accordance with the installation instructions supplied with those
products.
5
TROUBLESHOOTING
5.1
STATUS INDICATOR
The indicator shows the operating condition of the module.
Fig. 24 Module status indicator
5.2
REPLACING THE FUSE
To replace the fuse the cover of the module has to be removed.
1. Release fuse.
2. Take defective fuse out of fuse socket.
3. Dispose of defective fuse.
4. Replace fuse into fuse socket.
5. Secure fuse.
First make all electrical connections and then carry out
the commissioning!
▶ Follow all installation instructions of all components
and assemblies belonging to the system.
▶ Ensure that no two modules share the same coding.
▶ If several modules are used, ensure that the code
switch I of none of the module is set to
1
.
▶ Do not switch on the power supply until all modules
are set up.
NOTICE:
When switching the system on, the connected
pump may start immediately, this is part of the start-up
process and does not indicate an error.
▶ Ensure that the system is filled before switching the
system on to ensure that the pump does not run dry.
WARNING:
Risk of scalding!
▶ A mixer device must be installed if water
temperatures higher than 60 °C are set.
Only use original spare parts. Damage caused by the use
of spare parts not approved for this product by the
manufacturer are excluded from our guarantee.
Indicator
Possible cause
Remedy
lights off
continuously (at
code switch I)
Code switch set to
0
▶ Set code switch
(
Power supply
interrupted.
▶ Switch ON power supply.
Fuse is defective
▶ Ensure that power supply
is isolated and replace
fuse (
Short circuit in the
BUS connection
▶ Check BUS connection
and repair if required.
Lights up red
continuously (at
code switch I)
Internal fault
▶ Replace module.
Flashes red
(at code switch I
or temperature
switch II)
Code switch in invalid
position or in
intermediate position
▶ Set code switch
(
Flashes green (at
code switch I)
Maximum cable length
for BUS connection
exceeded.
▶ Make shorter BUS
connection.
Temperature sensor is
faulty.
▶ Replace temperature
sensor.
Lights up green
continuously (at
code switch I)
No fault
Standard operation.
Table 4 Troubleshooting
DANGER:
Risk of electric shock!
▶ Electrically isolate the boiler and system
components. Secure against unintentional
reconnection and make sure the power supply is
disconnected.
0
1
2
3
4
S
Y
I
off
40
50
60
70
max
II
II
6 720 804 106-23.1O