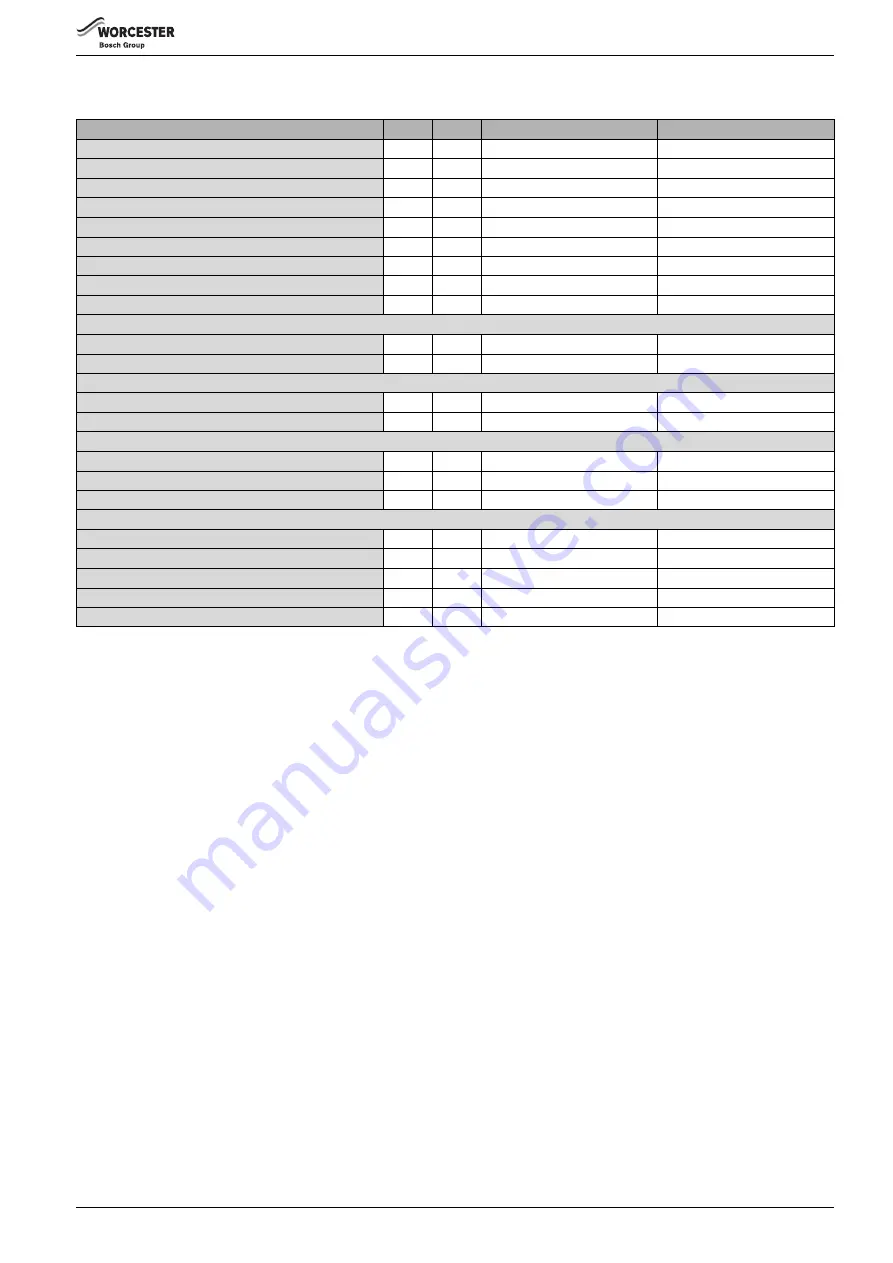
Appliance information
Greenstar Utility
ErP -
6 720 821 751 (2018/04)
7
3.3
Energy efficiency
The following product data satisfy the requirements of the EU Regulations No. 811/2013 and No. 812/2013 supplementing Directive 2010/30/EU.
Product data
Symbol
Unit
7 731 600 171
7 731 600 172
Product type
–
–
Greenstar Utility ErP+ 32/50
Greenstar Utility ErP+ 50/70
Condensing boiler
–
–
Yes
Yes
Low temperature boiler
–
–
No
No
B1 boiler
–
–
No
No
Cogeneration space heater (CHP)
–
–
No
No
Combination heater
–
–
No
No
Rated heat output
P
rated
kW
50
70
Seasonal space heating energy efficiency
η
s
%
90
91
Energy efficiency class
–
–
A
A
Useful heat output
At rated heat output and high temperature regime
1)
1) High-temperature regime means 60 °C return temperature at heater inlet and 80 °C feed temperature at heater outlet.
P
4
kW
50.1
71.8
At 30% of rated heat output and low temperature regime
2)
2) Low temperature means for condensing boilers 30 °C, for low-temperature boilers 37 °C and for other heaters 50 °C return temperature (at heater inlet).
P
1
kW
15.99
22.90
Useful efficiency
At rated heat output and high temperature regime 1)
η
4
%
97.3
97.5
At 30% of rated heat output and low temperature regime 2)
η
1
%
101.7
101.7
Auxiliary electricity consumption
At full load
el
max
kW
0.192
0.182
At part load
el
min
kW
0.065
0.061
In standby mode
P
SB
kW
0
0
Other items
Standby heat loss
P
stby
kW
0.272
0.278
Ignition burner power consumption
P
ign
kW
0
0
Emissions of nitrogen oxides
NOx
mg/kWh
94
94
Annual energy consumption
Q
HE
kWh
44,444
61,539
Sound power level, indoors
L
WA
dB(A)
61
60
Table 2 Product data for energy consumption