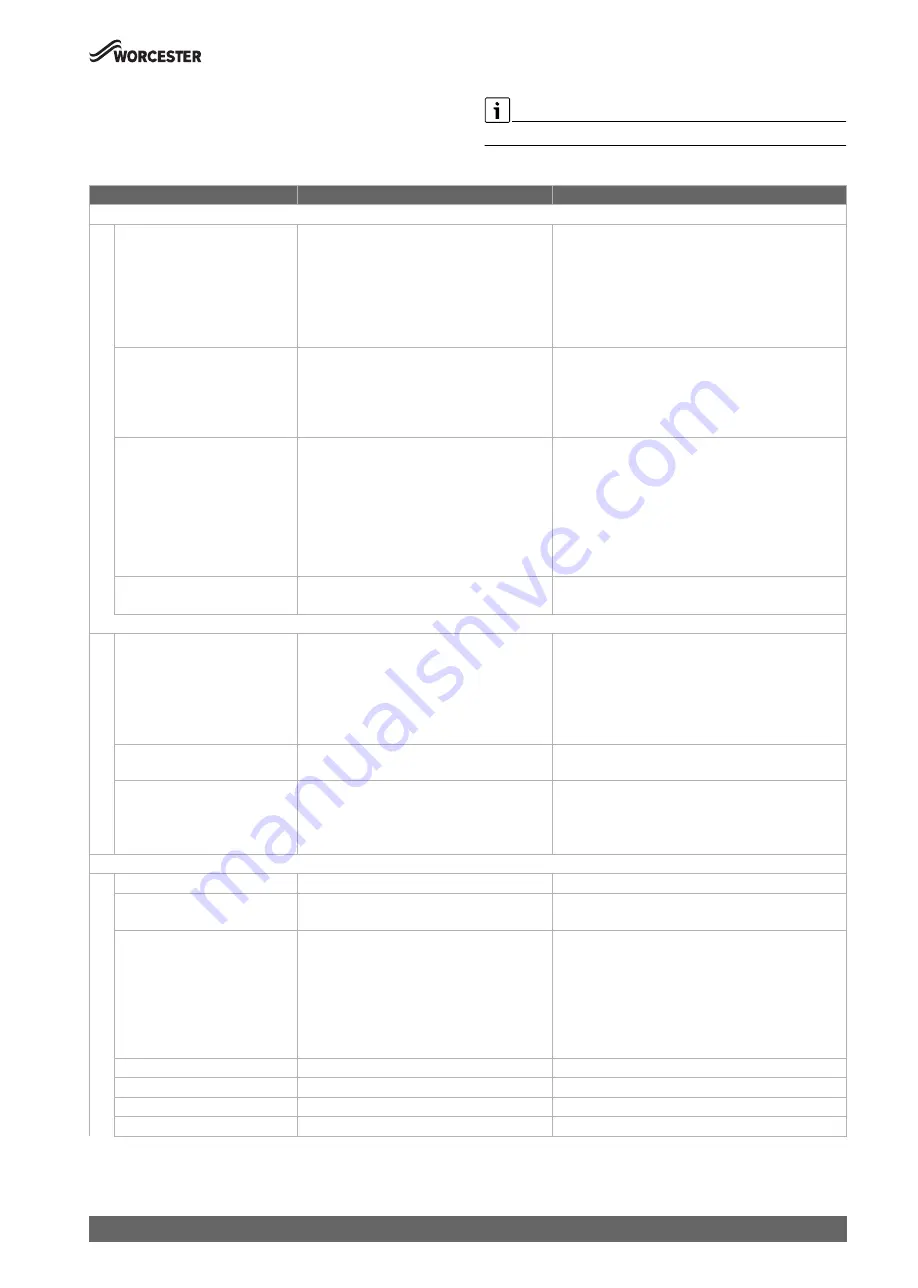
Settings in the service menu
51
Greenstar 8000 Style – 6720883855 (2019/01)
7.2.3
Settings menu
The menu is adapted to your system automatically. Some menu items are
only available if the system has been set up accordingly. The menu items
are only displayed in systems in which the corresponding system
components are installed, e.g. Key Timer.
The factory settings are
highlighted
in the following table.
Menu item
Settings/adjustment range
Comment/restriction
Hydraulics
Low-loss header
• Low loss header not installed in the system
• Low loss header installed, temperature sensor
connected to the wall mounted boiler
• Low loss header installed, temperature sensor
connected to the heating circuit module
• Low loss header installed, but no temperature
sensor is connected
Position of the low loss header temperature sensor
DHW configuration
• Not installed
• 3-way valve installed
• System?: Cyl. prim. pump inst. after low loss
hdr.
• System?: Cyl. primary pump installed
HC1 configuration
• No heating circuit 1 (HK1) on the appliance
(HK1 not available or not connected via the
heating circuit module)
• No own pump (flow rate for HK1 is realised by
the heating pump)
• Own HC1 pump downstream the low loss
header
• Dedicated pump installed
Pump config.
• None
• Heating pump
Heating
Max. heat output
Maximum released thermal output [%].
On natural gas applainces:
▶ Measure the gas rate.
▶ Compare the measurement with the setting tables
(
▶ Correct deviations.
Standby time
• 3…
10
…60 minutes
The time interval determines the minimum delay between
starting and restarting the burner.
Clock inh. T. off
Clock inh. T. on
• 2 …
6
… 15 Kelvin
• -15...
-6
...-2 Kelvin
Temperature standby period.
The difference between the current flow temperature and
the set flow temperature until the burner is switched on or
off.
Hot water
Max. DHW output
• 10...
100
%
Maximum power on hot water
DHW circ. pump
•
Off
• On
Activation of hot water circulation pump
Cycle circ. pump
•
1 x 3 minutes/h
• 2 x 3 minutes/h
• 3 x 3 minutes/h
• 4 x 3 minutes/h
• 5 x 3 minutes/h
• 6 x 3 minutes/h
• Permanent
Number and duration of starts of hot water circulation
pump per hour
TD-Temperature
• 60...
70
…80 °C
Max. TD duration
•
10
…30 minutes
Max. duration of legionella protection cycle in minutes
Start TD
Start now?
Start legionella protection cycle
Stop TD
Cancel now?
Stop legionella protection cycle