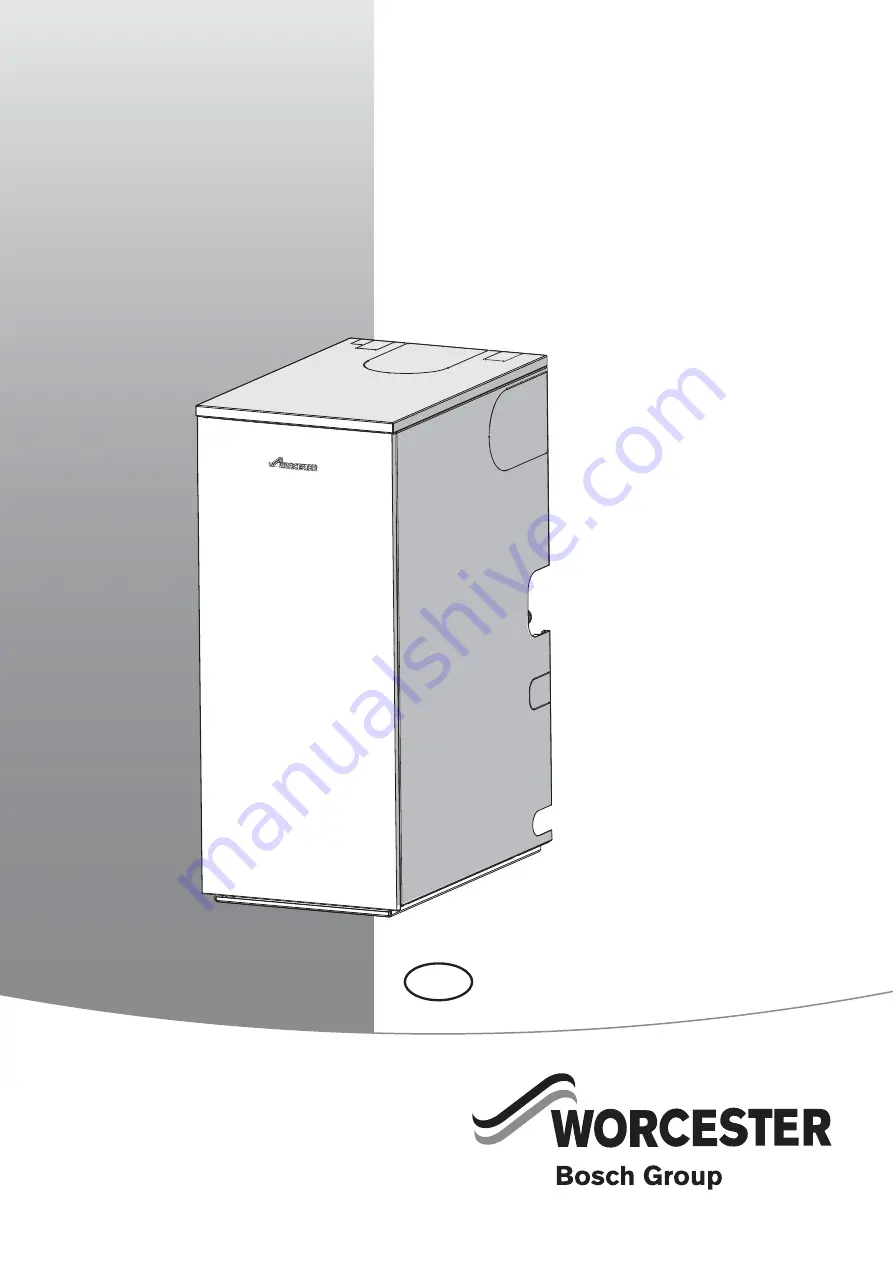
UK
Installation, Commissioning and Servicing instruction manual
Floor Standing oil-fired Condensing Boiler Conventional Flue & Room Sealed Flue
Greenstar Danesmoor Utility Regular
ErP+
& Utility System
ErP+
12/18, 18/25, & 25/32
6720809436-00.1W
o
For fully pumped open vent or sealed central heating systems and domestic hot water cylinders
These appliances are for use with Kerosene (Class C2) only.
6 72
0 821 720 (2018/04)