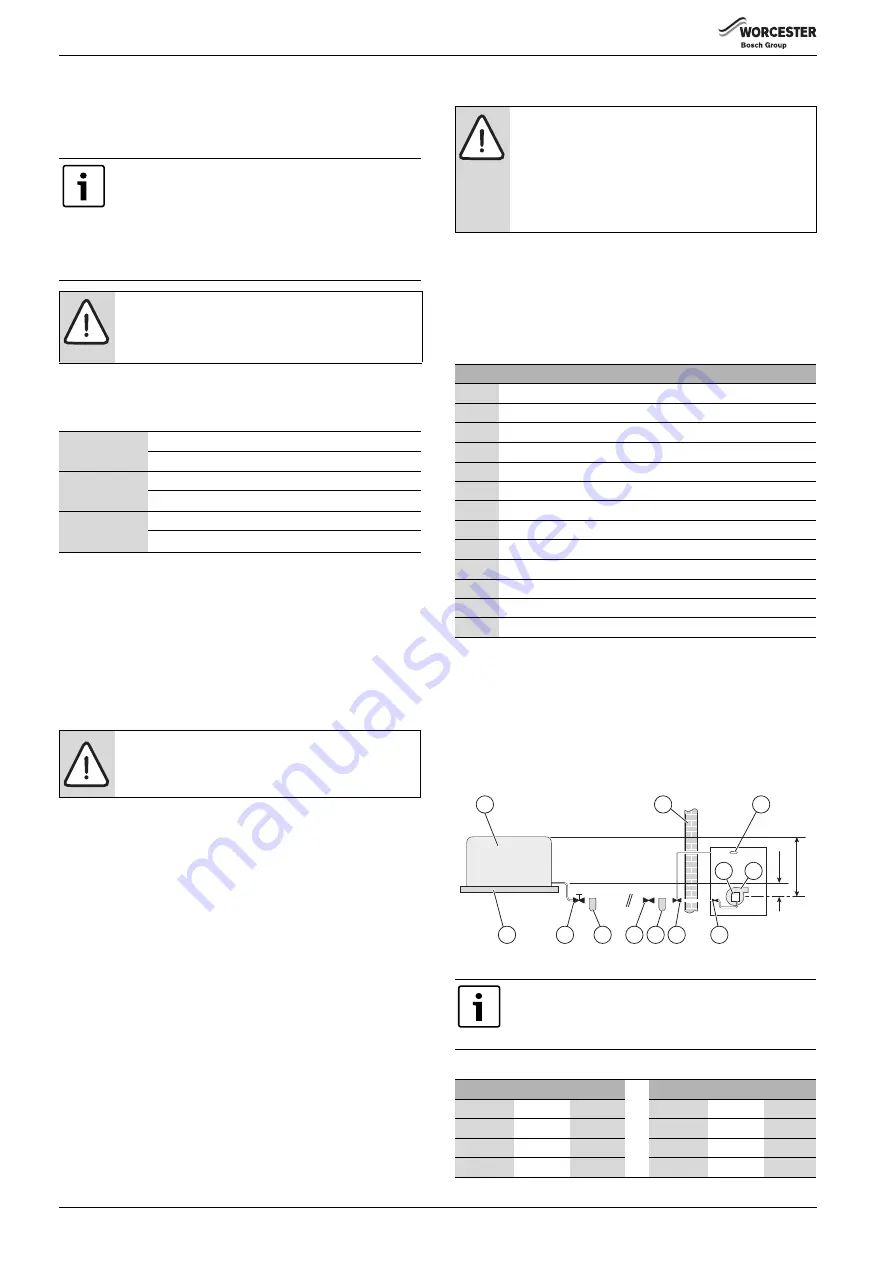
Pre-Installation
Greenstar Danesmoor Utility
ErP+
and Utility System
ErP+
- 6 720 821 720 (2018/04)
12
4.1.5
Inhibitor
Add a suitable inhibitor or combined inhibitor/anti-freeze, if the system
is exposed to freezing conditions, to the heating system in accordance
with the DWTA code of practice and manufacturer‘s guidelines.
Water treatment products
Suitable water treatment products can be obtain from the following
manufacturers:
4.1.6
Artificially softened water
It is possible to have an ion exchange water softener fitted to the cold
water system of the property. However, the boiler requires an untreated
cold water connection taken from the mains supply, before the water
softener, to the primary water filling point of the heating system.
Alternatively there are water softening/treatment devices that do not
adjust or alter the pH levels of the water. With these devices it may not
be necessary to provide an untreated water by-pass to the primary water
filling point of the heat system.
4.2
Mains supply
4.2.1
Electrical supply
• Supply: 230V - 50 Hz
• Cable: PVC insulated 0.75 mm2 (24 x 0.2mm) temperature rated to
90°C.
• External 5A fuse to BS1362.
• The appliance must be earthed.
• This appliance must not be connected to a three phase supply.
• Wiring must comply with the latest IET wiring regulations.
• It must be possible to isolate the appliance from the electrical supply
with at least a 3mm contact separation in both poles supplying the
appliance.
• Wiring between the appliance and the electrical supply must comply
with IET wiring regulations and any local regulations that may apply
for fixed wiring to a stationary appliance.
• Any additional components that are connected to the boiler with
mains electrical supply must not have a separate supply.
4.3
Oil supply
•
This appliance is suitable for Kerosene (Class C2) only, no other
fuel must be used.
• Plastic or steel tanks should be installed to BS 5410.
A steel tank should conform to BS 799: part 5 and have a slope of
1:24 away from the outlet with a sludge cock at the lower end.
•
Do not use galvanised steel tanks or pipework for the oil system.
•
Do not use soldered joints on the oil supply pipework.
4.3.1
Single pipe gravity feed system:
The oil storage tank [1] must be positioned so that the oil level does not
exceed 4 metres above the level of the burner oil pump [9] and in
addition the oil level must be at least 300mm above the oil pump [9].
Where the maximum oil level in the oil storage tank exceeds 4 metres, a
head breaking device must be installed between the tank [1] and the
burner oil pump [9].
Fig. 7
Single pipe feed
Maximum pipe run for single pipe gravity fed system
The inhibitor or combined inhibitor/anti-freeze must not
cause damage to the materials within the boiler (mild
steel, stainless steel, copper and brass) and any other
materials/components within the system.
▶ The concentration level of inhibitor in the system
should be checked every 12 months or sooner if
system content is lost.
WARNING:
Sealing agents
▶ In cases where all attempts to find a system micro
leak have failed, Worcester, Bosch Group supports
the use of Fernox F4 leak sealer.
ADEY
01242 546717
www.adey.com
FERNOX
0870 601 5000
www.fernox.com
SENTINEL
0800 389 4670
www.sentinel-solutions.net
NOTICE:
▶ Salt based, softened water must not be used to fill
the central heating system.
NOTICE:
Contaminated oil supplies can damage the
appliance.
Failure to ensure that the oil supply is clear of
contaminants may invalidate the appliance warranty.
▶ Ensure the oil supply is free of contaminates and
measures are taken to prevent contamination of the
appliance.
Key to Oil supply illustrations, figures 7, 8 & 9
1
OIl storage tank
2
Full base (plastic tank)
3
Isolating valve
4
Oil strainer and water separator
5
Fire valve to BS 5410
6
External wall
7
Oil filter (70μm max filtration size)
8
Fire valve sensor
9
Oil pump
10
Oil burner
11
Non-return valve
12
De-aerator
13
Appliance isolation valves
Table 4 Key to oil supply feed system
All dimensions are in metres unless otherwise stated.
The maximum pipe run figures are based on using
copper pipe with an inside diameter of 2mm less than
the outside diameter.
Head (m) 10mmØ 12mmØ
Head (m) 10mmØ 12mmØ
0.5
12
30
2.5
62
100
1.0
25
69
3.0
74
100
1.5
37
91
3.5
87
100
2.0
49
100
4.0
99
100
6720813284-08.2Wo
1
2
3
4
300mm
Min.
4m Max.
6
8
5
3
10
9
13
7