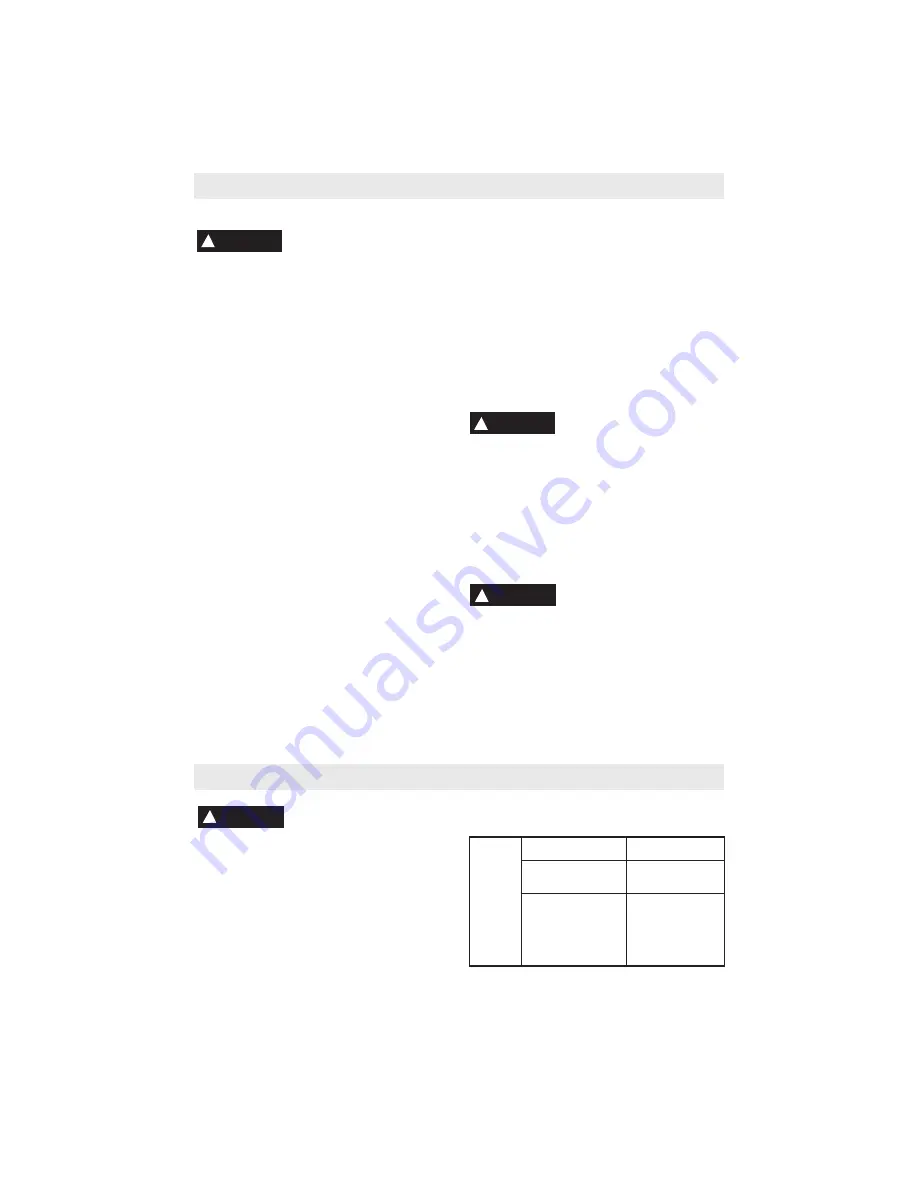
-16-
Service
Preventive maintenance
performed by unauthorized
personnel may result in misplacing of
internal wires and components which
could cause serious hazard.
We
recommend that all tool service be performed
by a Bosch Factory Service Center or Autho-
rized Bosch Service Station.
TOOL LUBRICATION
Your Bosch tool has been properly lubricated
and is ready to use. It is recommended that
tools with gears be regreased with a special
gear lubricant at every brush change.
CHUCK LUBRICATION
The wrenchless chuck has been properly
lubricated and is ready to use. If the chuck's
jaws begin to stick during use, the chuck
requires lubrication. To lubricate the chuck,
first remove debris from the inside of the
chuck with compressed air. Apply a pea-
sized amount of general-purpose grease to
the sides of the jaws, and adjust the chuck
through its full range of motion to distribute
the grease.
CARBON BRUSHES
The brushes and commutator in your tool
have been engineered for many hours of
dependable service. To maintain peak
efficiency of the motor, we recommend every
two to six months the brushes be examined.
Only genuine Bosch replacement brushes
specially designed for your tool should be
used.
BEARINGS
After about 300-400 hours of operation, or at
every second brush change, the bearings
should be replaced at Bosch Factory Service
Center or Authorized Bosch Service Station.
Bearings which become noisy (due to heavy
load or very abrasive material cutting) should
be replaced at once to avoid overheating or
motor failure.
Cleaning
To avoid accidents always
disconnect the tool from
the power supply before cleaning or
performing any maintenance.
The tool may
be cleaned most effectively with compressed
dry air.
Always wear safety goggles when
cleaning tools with compressed air.
Ventilation openings and switch levers must
be kept clean and free of foreign matter. Do
not attempt to clean by inserting pointed
objects through openings.
Certain cleaning agents
and solvents damage
plastic parts.
Some of these are: gasoline,
carbon tetrachloride, chlorinated cleaning
solvents, ammonia and household
detergents that contain ammonia.
!
WARNING
!
WARNING
Maintenance
!
CAUTION
If an extension cord is
necessary, a cord with
adequate size conductors that is capable
of carrying the current necessary for your
tool must be used.
This will prevent
excessive voltage drop, loss of power or
overheating. Grounded tools must use 3-
wire extension cords that have 3-prong plugs
and receptacles.
NOTE:
The smaller the gauge number, the
heavier the cord.
RECOMMENDED SIZES OF EXTENSION CORDS
120 VOLT ALTERNATING CURRENT TOOLS
!
WARNING
Tool’s
Ampere
Rating
Cord Size in A.W.G.
Wire Sizes in mm
2
3-6
6-8
8-10
10-12
12-16
18
16
16
14
0.75 0.75 1.5
2.5
18
16
14
12
0.75 1.0
2.5
4.0
18
16
14
12
0.75 1.0
2.5
4.0
16
16
14
12
1.0
2.5
4.0
—
14
12
—
—
—
—
—
—
25
50
100 150
15
30
60
120
Cord Length in Feet
Cord Length in Meters
Extension Cords