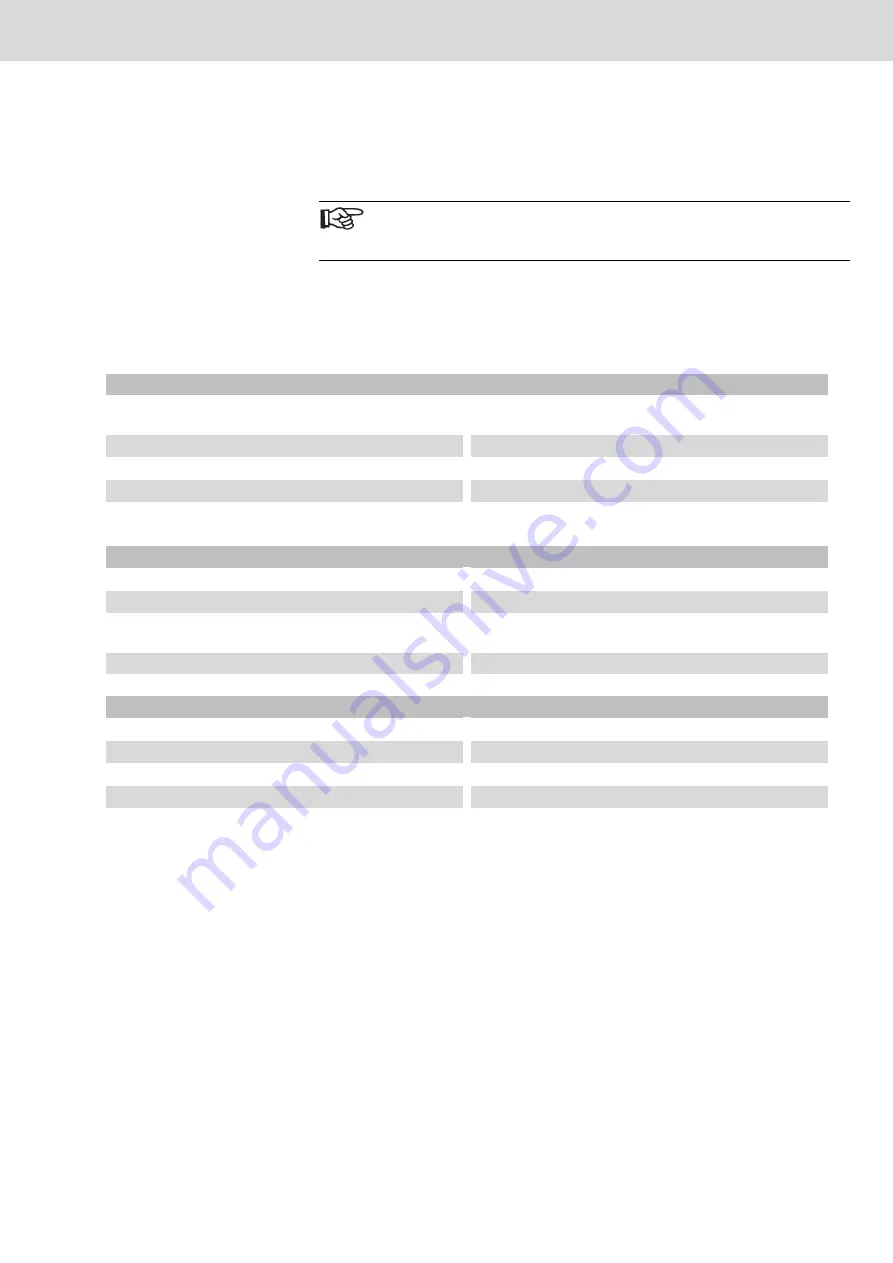
Technical Data and Ordering Data
Application Description
|
Inline
Electric Drives |
Bosch Rexroth AG
and Controls
9
Technical Data and Ordering Data
The technical data does not claim to be complete. Technical modifications
reserved.
9.1
INTERBUS System Data
The following values are standard values for the preferred mounting
position (horizontal DIN rail). For different values, please refer to the
terminal-specific data sheets.
INTERBUS system
Number of I/O points
4096, maximum (firmware version 4.4x or later)
8192, maximum (firmware version 4.6x or later)
Number of data words
256, maximum
Transmission speed
500 kbps or 2 Mbps
Transmission reliability
CR check (hamming distance: 4)
Protocol
IEC 61158
Number of devices
Total number of bus devices
512, maximum
Number of remote bus devices
254, maximum
Number of PCP devices
62, maximum (firmware version 4.4x or later)
126, maximum (firmware version 4.6x or later)
Number of remote bus levels
16, maximum
Distances
From the controller board to the last bus coupler
12.8 km, maximum (copper)
From the controller board to the first device
400 m, maximum (copper)
Between two remote bus devices
400 m, maximum (copper)
Between two installation remote bus devices
50 m, maximum (copper)
Between a bus coupler and installation remote bus device
50 m, maximum (copper)