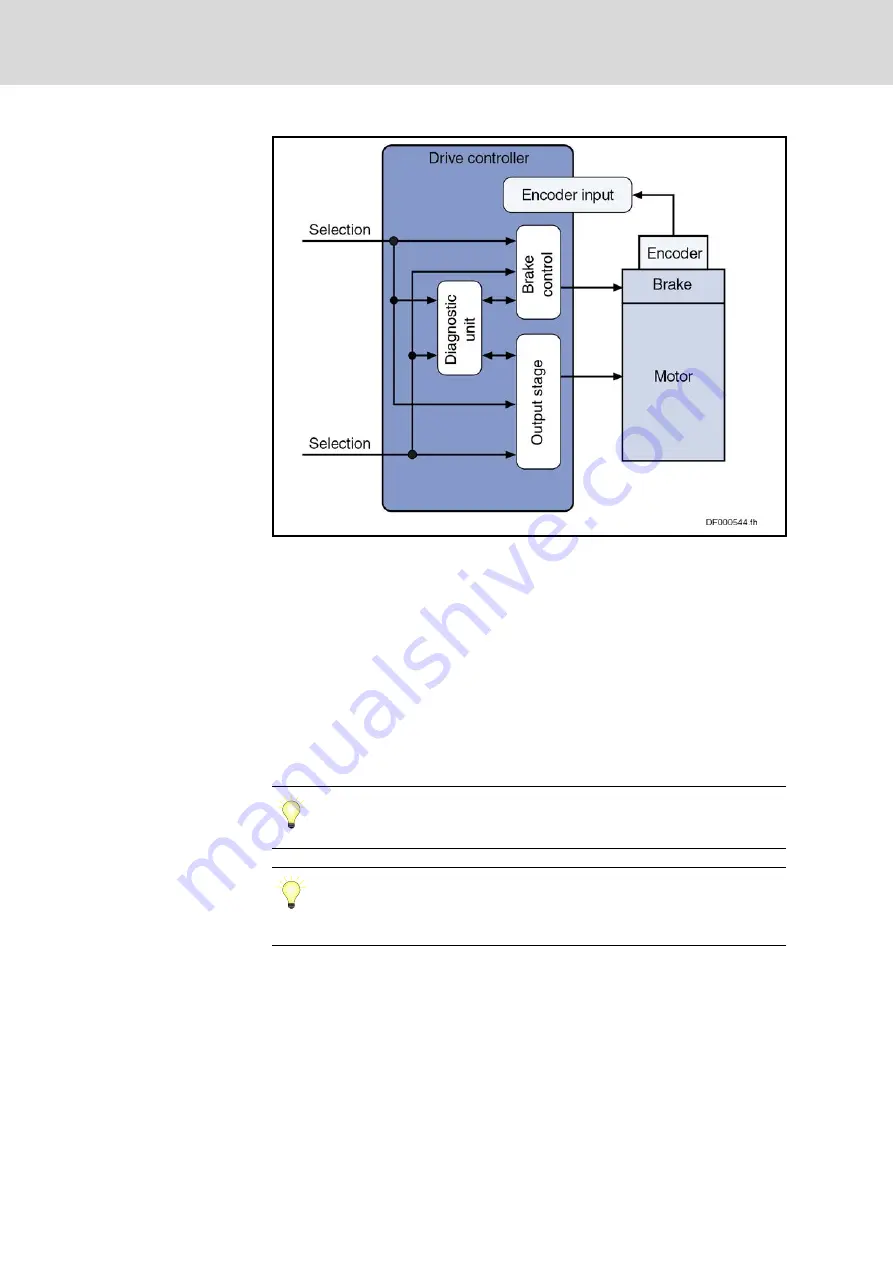
Fig. 5-1:
Schematic diagram of IndraDrive Cs with integrated safety technology
5.1.2
Dynamization
Brief description
Dynamization is to detect static error states in the safety-relevant circuits.
Dynamization takes place automatically in the background without having an
effect on the safety function or the standard drive functions.
Functional principle of dynamization
A safety function is selected via an N/C-N/C combination, i.e. a "0" signal at
both inputs is evaluated when the safety functions are selected. Therefore,
the dynamization of the external selection channels can only take place in the
deselected state (normal operation).
Dynamization in the case of selec‐
tion via an active safety unit
An active safety unit is a safety switching device which selects the
safe function via OSSD outputs. The active safety unit tests its
outputs on its own.
The "OSSD" (Output Signal Switching Device) is that part of a
safe selection unit which has been connected to the machine
control and which goes to the OFF state, when the safe selection
unit triggers during the intended operation.
When the safety functions are selected via an active safety unit, the
dynamization pulses of the OSSD outputs of the active safety unit are
evaluated and monitored; therefore, other dynamization signals are not
required.
The active safety unit must detect the following errors via its OSSD outputs:
●
Short circuit of one or both selection signals with 24 V
●
Short circuit of one or both selection signals with 0 V
Bosch Rexroth AG
DOK-INDRV*-SI3-**VRS**-AP06-EN-P
Rexroth IndraDrive Integrated Safety Technology "Safe Torque Off" (as of MPx-16)
44/149
Functional principle of integrated safety technology
LSA Control S.L. www.lsa-control.com [email protected] (+34) 960 62 43 01