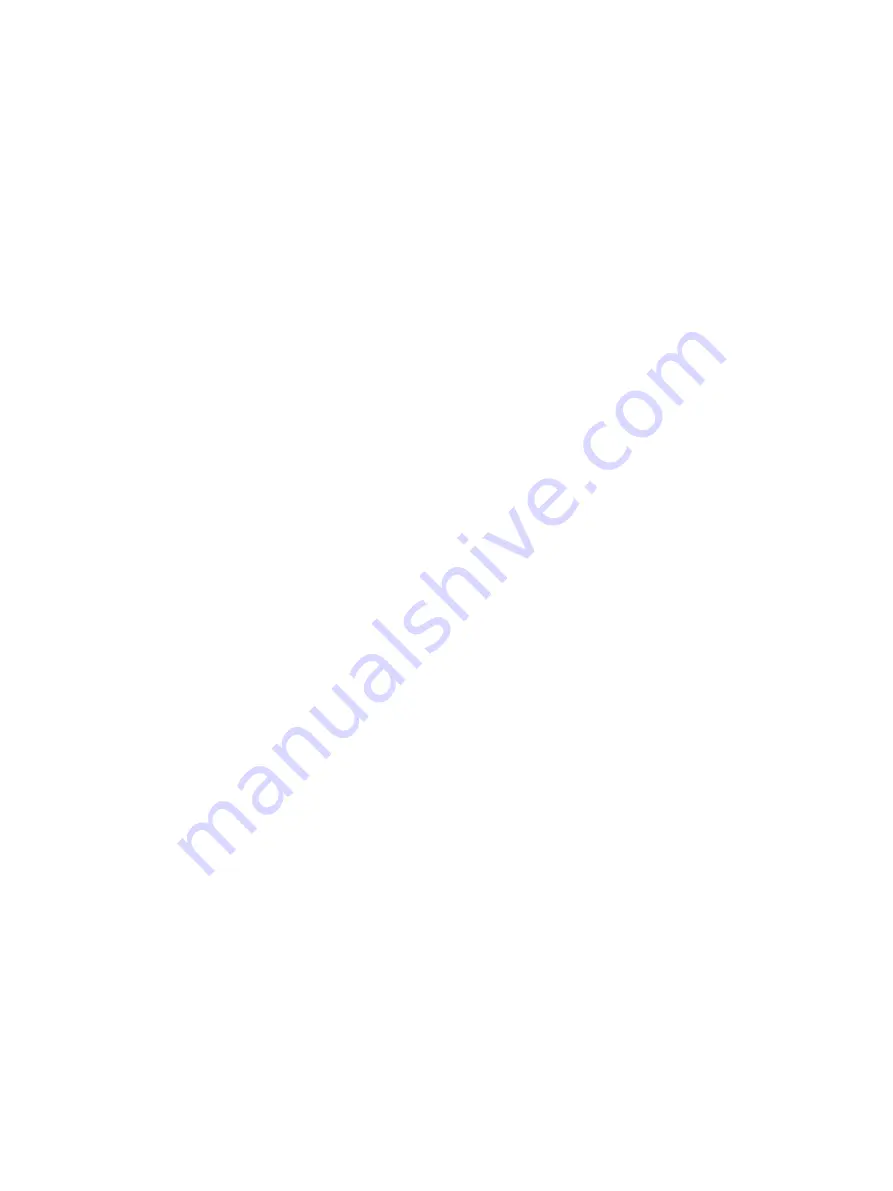
Bosch Rexroth AG
, RE 95528/05.2016
14
BVD/BVE Series 52
| Counterbalance valve
Project planning notes
Type selection (type code)
Control range
The control range defines the pressure range at which the
counterbalance spool starts to open. The control range of
the counterbalance spool is to be chosen so that the
mechanical holding brake is fully open before the counter-
balance spool starts to open.
Brake release
The integrated pressure reducing valve is necessary when
the mechanical brake on the gearbox cannot handle the full
system pressure. The maximum permissible brake release
pressure must be agreed with the gearbox manufacturer.
The counterbalance valve reduces the high pressure to the
value stated.
Counterbalance spool version
The counterbalance spool version depends on the maxi-
mum flow required through the counterbalance valve.
Selection of the counterbalance spool for the required flow
in accordance with characteristic curves on page 5.
If the desired flow is not within the range of the counterbal-
ance spool supplied, please contact us.
Residual opening in counterbalance spool
In winch drive and track drive applications, any residual open-
ing is prohibited, since otherwise the load would not stay
suspended. For that reason, version “K00” is prescribed.
Damping
The throttle pin from D1 (inlet) and the orifice D2 (reservoir
outlet), plus the counter pressure at the counterbalance
spool, determine the actual cracking pressure of the counterbal-
ance spool at the working port.
The damping D1 (outlet) and D2 determine the closing speed
of the counterbalance spool. The larger the comparative diam-
eter D1 (outlet), the faster the counterbalance spool will close
(see table on page 4).
For the initial equipment (prototype), we recommend
damping D1 = D4599 and D2 = T03 for winch drives.
For the initial equipment (prototype), we recommend
damping D1 = D4599 and D2 = T00 for track drives.