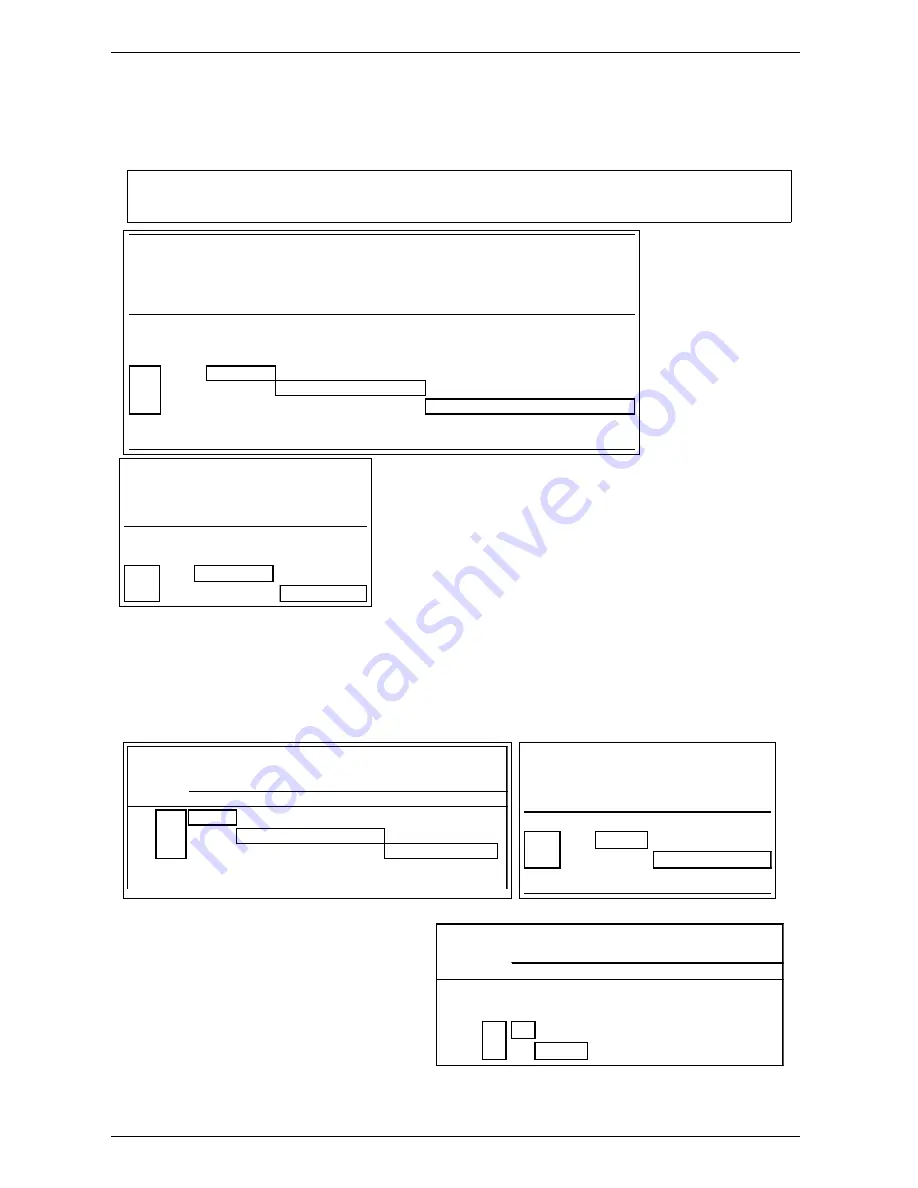
6 720 607 072
16
Appliance details
FOR NATURAL GAS
Maximum Capacity of pipe in Cubic Feet of Gas per Hour for Gas Pressure of 0.5 Psig or less and a Pressure drop
of 0.3 in Water Column (0.75mbar).(Based on a 0.60 Specific Gravity Gas) Btu numbers given in thousands.
Fig. 22
Follow boxed numbers for piping just one 635-ES (example: ¾” B.I. Natural Gas pipe for 20 ft (6.1m). will
handle 190,000 btu’s (55.7 kWh). For multiple appliances combine the total btu input load and then refer to
applicable chart below.
Nominal
Iron
Length of Black Iron Pipe, Feet
Pipe
Internal
Size,
Diameter
inches inches
10
20
30
40
50
60
70
80
90
100
125
150
175
200
1/4
0.364
32
22
18
15
14
12
11
11
10
9
8
8
7
6
3/8
0.493
72
49
40
34
30
27
25
23
22
21
18
17
15
14
1/2
0.622
132
92
73
63
56
50
46
43
40
38
34
31
28
26
3/4
0.824
278
190
152
130
115
105
96
90
84
79
72
64
59
55
1
1.049
520
350
285
245
215
195
180
170
160
150
130
120
110
100
1 1/4
1.380
1050
730
590
500
440
400
370
350
320
305
275
250
225
210
1 1/2
1.610
1600
1100
890
760
670
610
560
530
490
460
410
380
350
320
2
2.067
3050
2100
1650 1450
1270 1150 1050
990
930
870
780
710
650
610
* EHD = Equivalent Hydraulic Diameter. The greater the
value of EHD, the greater the gas capacity of the tubing
.
Maximum Capacity of Semi-Rigid (flexible, non
corrugated) Tubing in Thousands of BTU per Hour of
Undiluted Liquefied Petroleum Gases (at 11 inches
Water Column Inlet Pressure).
(Based on a Pressure Drop of 0.5 Inch Water Column)
* Source National Fuel Gas Code NFPA 54, ANSI
Z223.1 - No Additional Allowance is necessary for an
ordinary number of fittings
FOR LP GAS
Maximum Capacity of Pipe in Thousands of BTU per Hour of Undiluted Petroleum Gases (at 11 inches Water Column Inlet
Pressure) (Based on a Pressure Drop of 0.5 Inch Water Column).
Copper
Outside
Length of Tubing, Feet
diameter
Inch
10
20
30
40
50
60
70
80
90 100
3/8
39
26
21
19
_
_
_
_
_
_
1/2
92
62
50
41
37
35
31
29
27
26
5/8
199 131
107
90
79
72
67
62
59
55
3/4
329 216
181 145 131
121 112 104 95
90
Nominal
Iron Pipe
Black Iron Pipe
Size,
Length of Pipe, Feet
Inches
10
20
30
40
50
60
70
80
90
100
125
150
1/2
275 189 152 129 114 103 96
89
83
78
69
63
3/4
567 693 315 267 237 217 196 185 173 162
146
132
1
107 732 590 504 448 409 378 346 322 307
275
252
1 1/4 220 149 121 103 913 834 771 724 677 630
567
511
1 1/2 330 229 185 155 141 127 118 108 102 976
866
787
* EHD = Equivalent Hydraulic Diameter. The greater the
value of EHD, the greater the gas capacity of the tubing.
Tube
size,
inches
EHD*
10
20
30
40
50
60
1/2
18 EHD 82
58
47
41
37
34
3/4
23 EHD 161
116
96
83
75
68
1
30 EHD 330
231
188
162
144
131
1 1/4 37 EHD 639
456
374
325
292
267
Length of Flexible Corrugated Stainless Steel Tubing (CSST), Feet
Tube
size
inches
EHD*
10
20
30
40
50
60
1/2
18 EHD 129
91
74
64
58
53
3/4
23 EHD 254
183
151
131
118
107
1
30 EHD 521
365
297
256
227
207
1 1/4 37 EHD 971
661
528
449
397
359
Length of Flexible Corrugated Stainless Steel Tubing (CSST), Feet