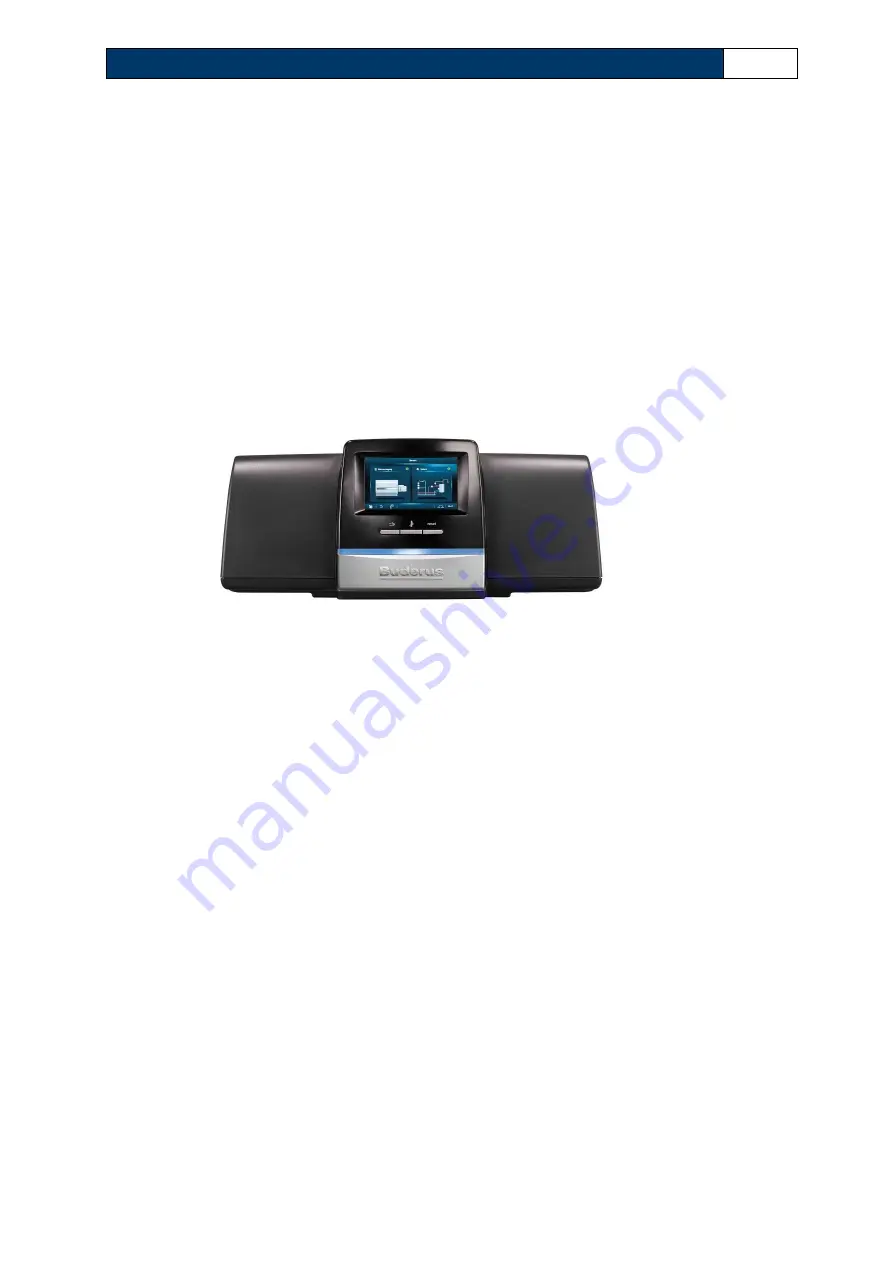
User Documentation
1|33
© All rights with Robert Bosch GmbH, also for the case of protected rights applications
EN_User_documentation_Instructions_for_controlling_the_Logamatic_5000_controller_series_via_Modbus_TCP_I
P_20210203.docx | 10.02.2021
Guideline on controlling the Logamatic
5000/Control 8000 controller series via Mod-
bus TCP/IP
This document helps you to realize the connection and control of the Logamatic
5000/Control 8000 controller series via Modbus TCP/IP with your building control
system.