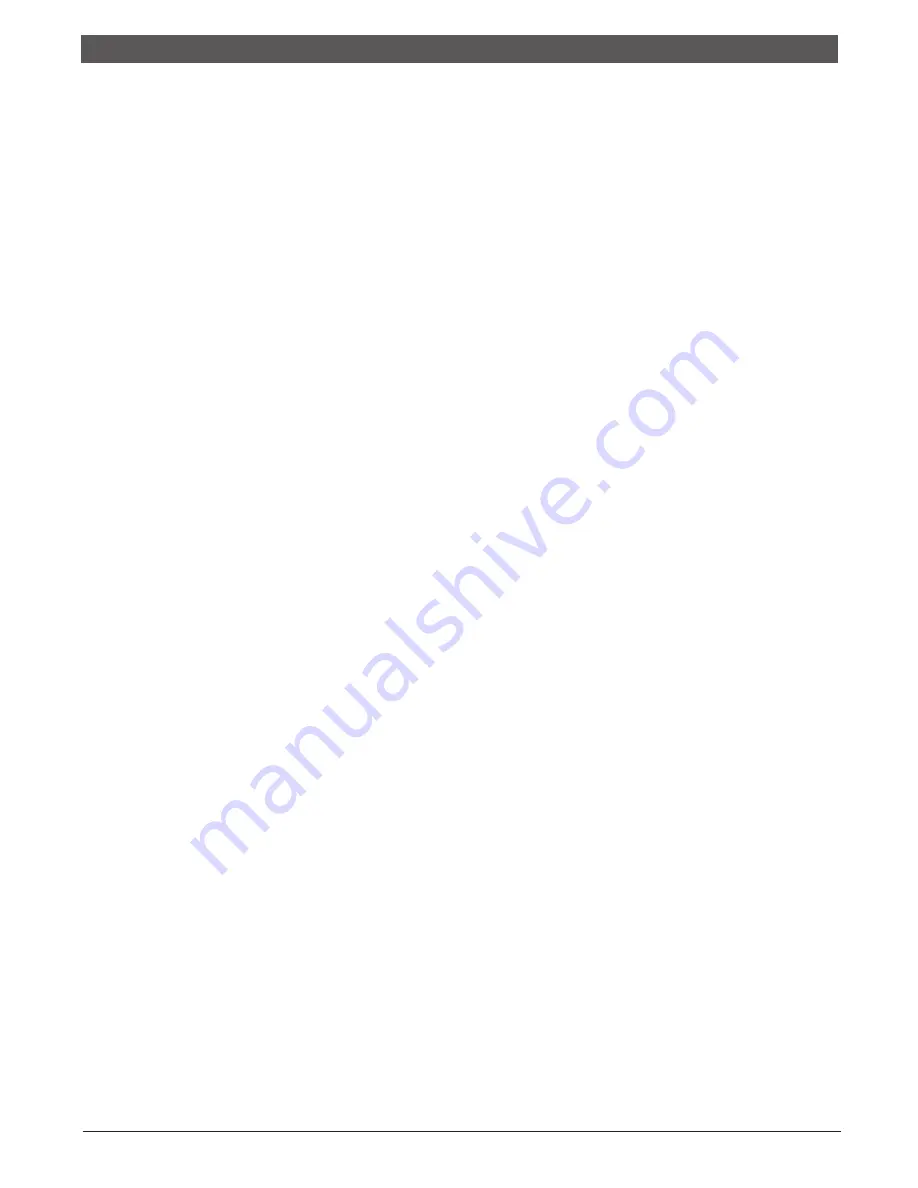
5 | EP Series
970-293 (2014/06)
CA Series
Subject to change without prior notice
Console Model
utilizing open cooling towers chemical water treatment
is mandatory to ensure the water is free from corrosive
elements. A secondary heat exchanger may also be used
between the unit and the cooling tower water. In closed
loop systems such as this it is imperative that all air be
removed from the closed side of the system to insure
against fouling of the heat pump water-to-refrigerant
heat exchanger.
In the heating mode, heat is absorbed from the loop by
the console unit. A boiler may be used to maintain the
loop at the desired temperature.
No unit should be connected to the supply or return
piping until the water system has been completely
cleaned and flushed to remove any dirt, piping chips or
other foreign material. Supply and return hoses should
be connected together during this process to ensure the
entire system is properly flushed. After the cleaning and
flushing has taken place the unit may be connected to
the water loop and should have all valves wide open.
EARTH COUPLED SYSTEMS:
Closed loop and pond applications require specialized
design knowledge. No attempt at these installations
should be made unless the contractor has received
specialized training.
Anti freeze solutions are utilized when low evaporating
conditions are expected to occur (I.E.: low loop
temperatures in heating). Typical temperatures are 30°F
fluid temperature in heating and 100°F in cooling.
MAINTENANCE:
1. Filter changes or cleanings are required at regular
intervals. The time period between filter changes will
depend upon type of environment the equipment is
used in. In a single family home, that is not under
construction, changing or cleaning the filter every 60
days is sufficient. I n other applications, such as
motels, where daily vacuuming procedures a large
amount of lint, filter changes may need to be as
frequent as biweekly.
2. An annual “checkup” is recommended by a licensed
refrigeration mechanic. Recording the performance
measurements of volts,amps, and water temperature
differences (both heating and cooling) is
recommended. This data should be compared to the
information on the unit’s data plate and the data
taken at the original startup of the equipment.
3. Lubrication of the blower motor is not required.
4. The condensate drain should be checked annually by
cleaning or flushing to insure proper drainage.
5. Periodic lockouts almost always are caused by air or
water flow problems. The lockout (shut down) of the
unit is a normal protective measure in the design of
the equipment. If continual lockouts occur call a
mechanic immediately and have them check for:
water flow problems, water temperature problems,
air flow problems or air temperature problems. Use of
the pressure and temperature charts for the unit may
be required to properly determine the cause.
SYSTEM CHECKOUT:
•
After completing the installation, and before
energizing the unit, the following system checks
should be made:
•
Verify that the supply voltage to the heat pump is in
accordance with the nameplate ratings.
•
Make sure that all electrical connections are tight and
secure.
•
Check the electrical fusing and wiring for the correct
size.
• Verify that the low voltage wiring bet ween the
thermostat and the unit is correct.
•
Verify that the water piping is complete and correct.
•
Check that the water flow is correct, and adjust if
necessary.
•
Check the blower for free rotation, and that it is
secured to the shaft.
• Verify that vibration isolation has been provided.
•
Unit is serviceable. Be certain that all access panels
are secured in place.
UNIT START-UP:
1. Set the thermostat to the highest setting.
2. Set the thermostat system switch to “COOL”, and the
fan switch to the “AUTO” position. The reversing valve
solenoid should energize. The compressor and fan
should not run.
3. Reduce the thermostat setting approximately 5
degrees below the room temperature.
4. Verify the heat pump is operating in the cooling
mode.
5. Turn the thermostat system switch to the “OFF”
position. The unit should stop running and the
reversing valve should de-energize.
6. Leave the unit off for approximately (5) minutes to
allow for system equalization.
7. Turn the thermostat to the lowest setting.
8. Set the thermostat switch to “HEAT”.
9. Increase the thermostat setting approximately 5
degrees above the room temperature.
10. Verify the heat pump is operating in the heating
mode.
11. Set the thermostat to maintain the desired space
temperature.
12. Check for vibrations, leaks, etc...
Earth Coupled Systems | 5