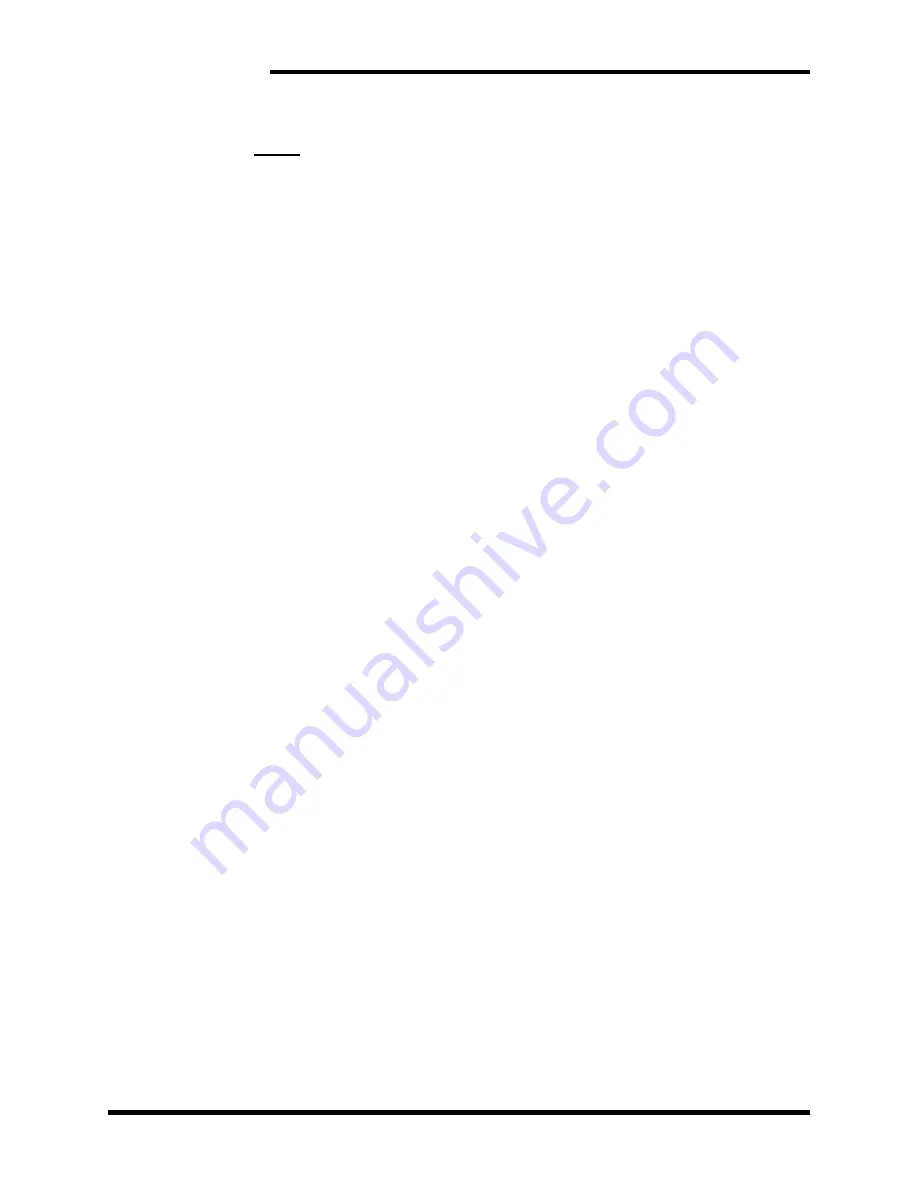
M3534R 20A
30
5.1.2. P
ERIODIC
M
AINTENANCE
P
ROCEDURES FOR
M3534R
M
ODULE
W
ITH
O
PTIONAL
DP10
D
ISPLAY
P
ANEL
1.
Check Active cycle counters.
More than 10 counts per month may mean the Ride-Thru is
improperly adjusted. Refer to Section 4.4.1 for adjustment details.
Note count for factory records.
Report count to Bonitron via your local service representative.
2.
Monitor front panel LEDs.
For the DP10 Display Panels:
Power LED should be
ON
.
Ride-Thru Active LED should be
OFF
.
Over-temperature LED should be
OFF
.
3.
Verify DC bus current meter. (DP17 only)
Meter should read zero amps under normal conditions.
4.
Verify DC bus voltage meter. (DP17 only)
Ride-Thru bus should be a few volts below the inverter bus.
5.
Verify Threshold by opening the AC disconnect to the Ride-Thru module
(if equipped). Refer to Section 4.4.1.
The DC bus voltage should drop until it reaches the threshold.
Ride-Thru Active LED should begin to
flash
.
DC bus should hold for a second at the threshold.
This threshold level should be approximately 10-12% below the
nominal loaded inverter bus.
Each Bonitron Ride-Thru should be tested under load during initial start up to
verify the functionality of the test circuit and that the test does not negatively
affect the process. However, Bonitron recommends that, if the process is
critical, the TEST cycle be initiated only during a shutdown to avoid unforeseen
problems.
6.
Verify switching circuits by pressing the TEST button while running the
inverter at full load.
Ride-Thru DC bus current should flow during the 2-second test cycle.
Inverter input current should drop.
Ride-Thru DC bus voltage should rise above the threshold. (+17% if
lightly loaded, less if fully loaded.)
Inverter DC bus voltage should rise above the threshold. (+17% if
lightly loaded, less if fully loaded.)
Ride-Thru Active LED should turn
ON.
Motor speed should remain constant.
Active cycle counter (if used) should count test cycles.
This completes the maintenance procedure.
Summary of Contents for M3534B
Page 6: ...M3534R 20A 6 This page intentionally left blank ...
Page 18: ...M3534R 20A 18 This page intentionally left blank ...
Page 44: ...M3534R 20A 44 NOTES ...
Page 45: ...User s Manual 45 ...
Page 46: ...M3534R 20A 46 ...
Page 47: ......