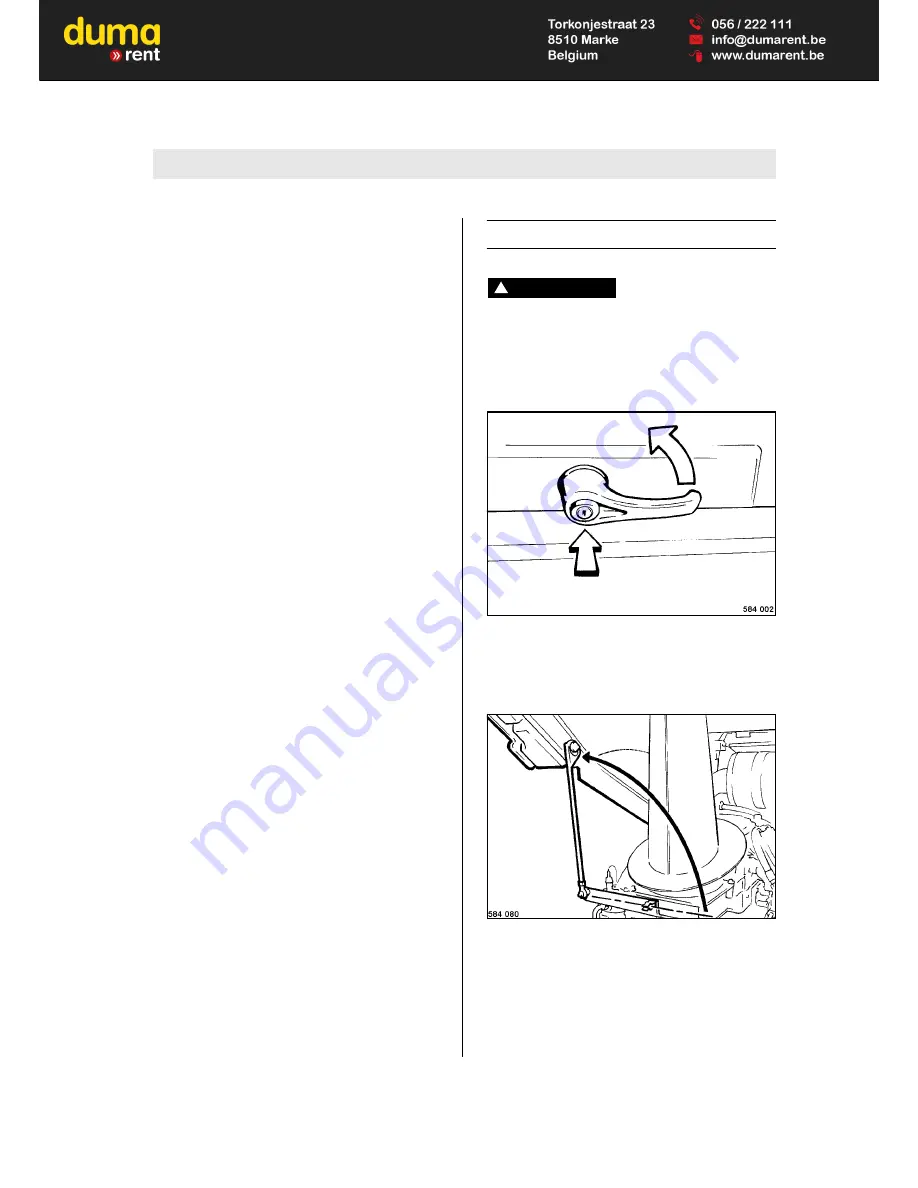
Operation
BOMAG
57
BW 177 D-4
Cooling the interior
l
Close all windows completely.
l
Direct the air flow towards the body/face (a).
l
Switch on the fan (c).
l
If necessary switch off the heating (b).
l
Switch on the air conditioning system with ro-
tary switch (d) and regulate the temperature.
Reducing the humidity
l
In case of damp weather direct the air flow to-
wards the windscreen and door screens.
l
Switch on the fan with the rotary switch (c).
l
Regulate the temperature to "Max" with the ro-
tary switch (b).
l
Switch the air conditioning (d) on.
5.14 Operating the hood
Danger
!
Danger of accident!
If the hood needs to be opened further for
maintenance or repair work, support it safely.
Bottom position
Fig. 75
l
Unlock the lock (Fig. 75).
l
To open the hood press in the button and turn
the handle.
Fig. 76
l
Pull the support out of the bracket and support
the hood (Fig. 76).
Top position
l
Push the hood to top position.
Summary of Contents for BW 177 D-4
Page 2: ......
Page 8: ...Table of Contents BOMAG 8 BW 177 D 4...
Page 9: ...BOMAG 9 BW 177 D 4 2 Technical Data...
Page 13: ...BOMAG 13 BW 177 D 4 3 Safety regulations...
Page 24: ...Safety regulations BOMAG 24 BW 177 D 4...
Page 25: ...BOMAG 25 BW 177 D 4 4 Indicators and Controls...
Page 26: ...Indicators and Controls BOMAG 26 BW 177 D 4 Fig 12...
Page 41: ...Indicators and Controls BOMAG 41 BW 177 D 4 4 5 Line diagram1 EVIB Fig 44 1 only BTM prof...
Page 44: ...Indicators and Controls BOMAG 44 BW 177 D 4...
Page 45: ...BOMAG 45 BW 177 D 4 5 Operation...
Page 72: ...Operation BOMAG 72 BW 177 D 4...
Page 73: ...BOMAG 73 BW 177 D 4 6 Maintenance...
Page 86: ...Every 10 operating hours BOMAG 86 BW 177 D 4...
Page 94: ...Every 250 operating hours BOMAG 94 BW 177 D 4...
Page 106: ...Every 500 operating hours BOMAG 106 BW 177 D 4...
Page 114: ...Every 1000 operating hours BOMAG 114 BW 177 D 4...
Page 118: ...Every 2000 operating hours BOMAG 118 BW 177 D 4...
Page 120: ...Every 3000 operating hours BOMAG 120 BW 177 D 4...
Page 122: ...Every 5000 operating hours BOMAG 122 BW 177 D 4...
Page 130: ...As required BOMAG 130 BW 177 D 4...
Page 131: ...BOMAG 131 BW 177 D 4 7 Trouble shooting...
Page 136: ...Trouble shooting BOMAG 136 BW 177 D 4...
Page 137: ...BOMAG 137 BW 177 D 4 8 Cab assembly before initial start up...
Page 147: ...BOMAG 147 BW 177 D 4 9 Disposal...
Page 149: ......
Page 150: ......