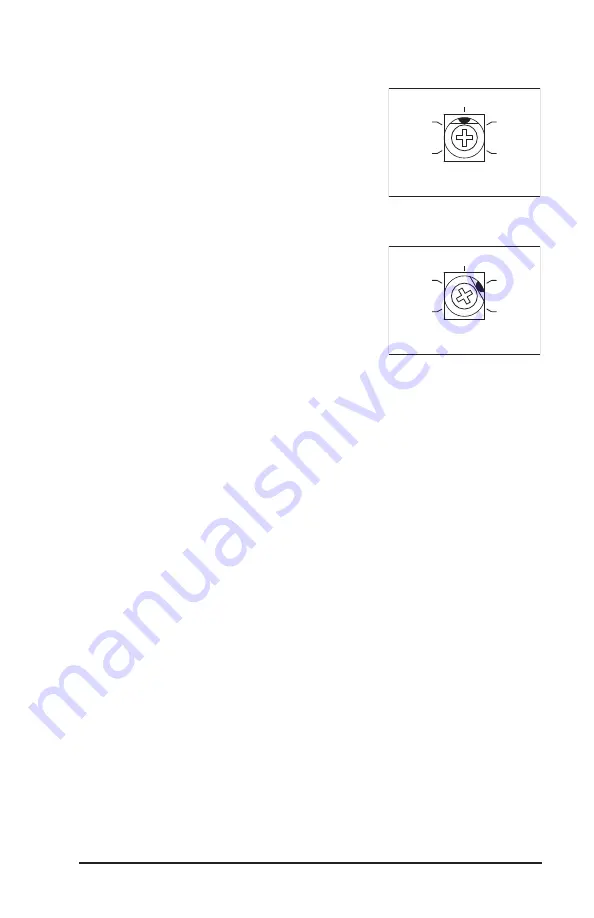
24
13.5 DC Injection Brake (DECEL) –
The drive is factory set
for Regenerative Braking (Jumper J7 set to the “RG”
position). When the drive is set for DC Injection Brake
(Jumper J7 set to the “INJ” position), the DECEL trimpot
is used to set the DC Injection Brake voltage and time.
See Figure 33. Also see Section 6.6 on page 18.
The DC Injection Brake voltage and time range is 10%
of full drive output voltage for 3 seconds with the trim-
pot fully clockwise and 25% of full drive output voltage
for 1 second with the trimpot fully counterclockwise.
The drive is factory set for 49 Volts for 1.2 seconds.
Adjust the trimpot so that the load stops within the
required time.
13.6 Slip Compensation (COMP) –
Sets the amount of Volts/
Hz to maintain set motor speed under varying loads.
The COMP Trimpot is factory set to 1.5 Volts/Hz, which
provides excellent speed regulation for most motors. To
increase the slip compensation, rotate the COMP Trimpot
clockwise. To decrease the slip compensation, rotate the
COMP Trimpot counterclockwise. See Figure 34.
The slip compensation may be adjusted as follows:
1.
Wire an AC RMS ammeter in series with one motor phase.
2.
Run the motor and set the unloaded speed to approximately 50% (900 RPM on 4-pole
1500/1725 RPM motors).
3.
Using a tachometer, record the unloaded speed.
4.
Load the motor to the nameplate rated current (AC Amps).
5.
Adjust the COMP Trimpot until the loaded RPM is equal to the unloaded RPM.
6.
The motor is now compensated to provide constant speed under varying loads.
13.7 Motor Overload (I
2
t) With RMS Current Limit (CL)* –
Sets the current limit (overload), which
limits the maximum current to the motor, which prevents motor burnout and eliminates
nuisance trips. The CL Trimpot is factory set to 160% of the drive rated current. To increase
the current limit, rotate the CL Trimpot clockwise. To decrease the current limit, rotate the
CL Trimpot counterclockwise. See Figure 35 and Figure 36.
*UL approved as an electronic overload protector for motors.
CAUTION!
Adjusting the current limit above 160% of the motor nameplate rating can cause
overheating of the motor. Consult the motor manufacturer. Do not leave the motor in a
locked rotor condition for more than a few seconds since motor damage may occur.
In order to ensure that the motor is properly protected with the I
2
t feature, it is required
that the CL Trimpot be set for 160% of the motor nameplate rated current, as described
below.
Note:
This adjustment must be made within 6 seconds or the I
2
t Trip will occur.
The current limit may be adjusted as follows:
1.
Connect an AC RMS ammeter in series with one motor phase.
2.
Set the CL Trimpot fully counterclockwise.
3.
Adjust the speed setting to 30%.
4.
Lock the motor shaft and adjust the CL Trimpot to 160% of the motor nameplate rated
current.
COMP
(Shown Factory Set to 1.5 Volts/Hz)
0
0.8
3
2.3
1.5
Figure 34 – Slip
Compensation Trimpot Range
CL
(Shown Factory Set to 160% Full Load)
40
200
80
160
120
Figure 35 – Current Limit
Trimpot Range