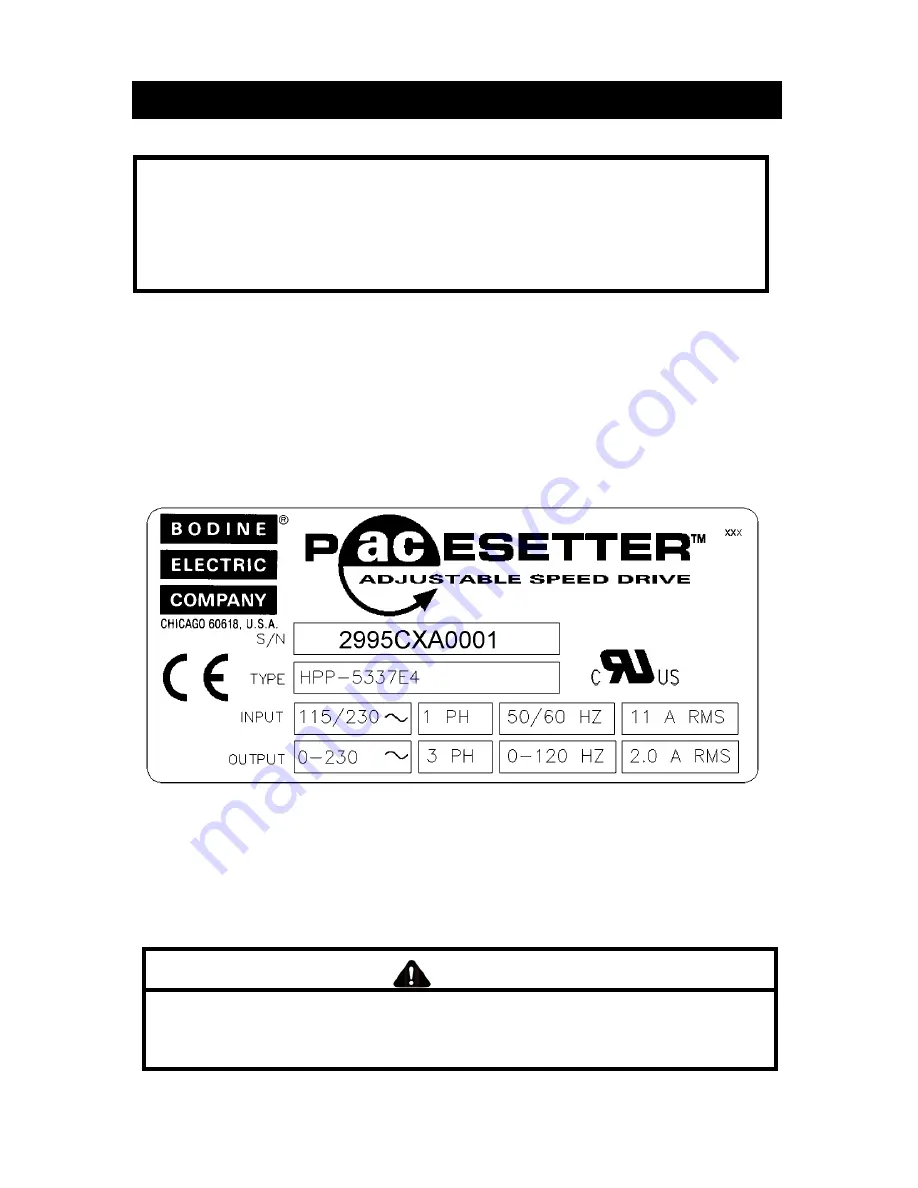
6
INSTALLATION
This control should only be installed by a qualified person familiar
with its operation and associated hazards. The National Electrical
Code (NEC), local electrical and safety codes, and when
applicable, the Occupational Safety and Health Act (OSHA) should
be observed to reduce hazards to personnel and property.
Step 1. Examine before installation
Check that the model number on the control matches the model number
ordered. The control model number is printed as part of the serial number on an
adhesive label on the outside bottom surface of the control enclosure. Carefully
examine the control for shipping damage. Parts errors should be reported to
Bodine. Shipping damage claims should be made to the freight carrier.
Figure 2 – The model number is the first four digits of the serial number
(S/N) on the control’s nameplate.
CAUTION
Do not connect the control to the power supply if there is
any sign of damage. Notify the carrier and your distributor
immediately.