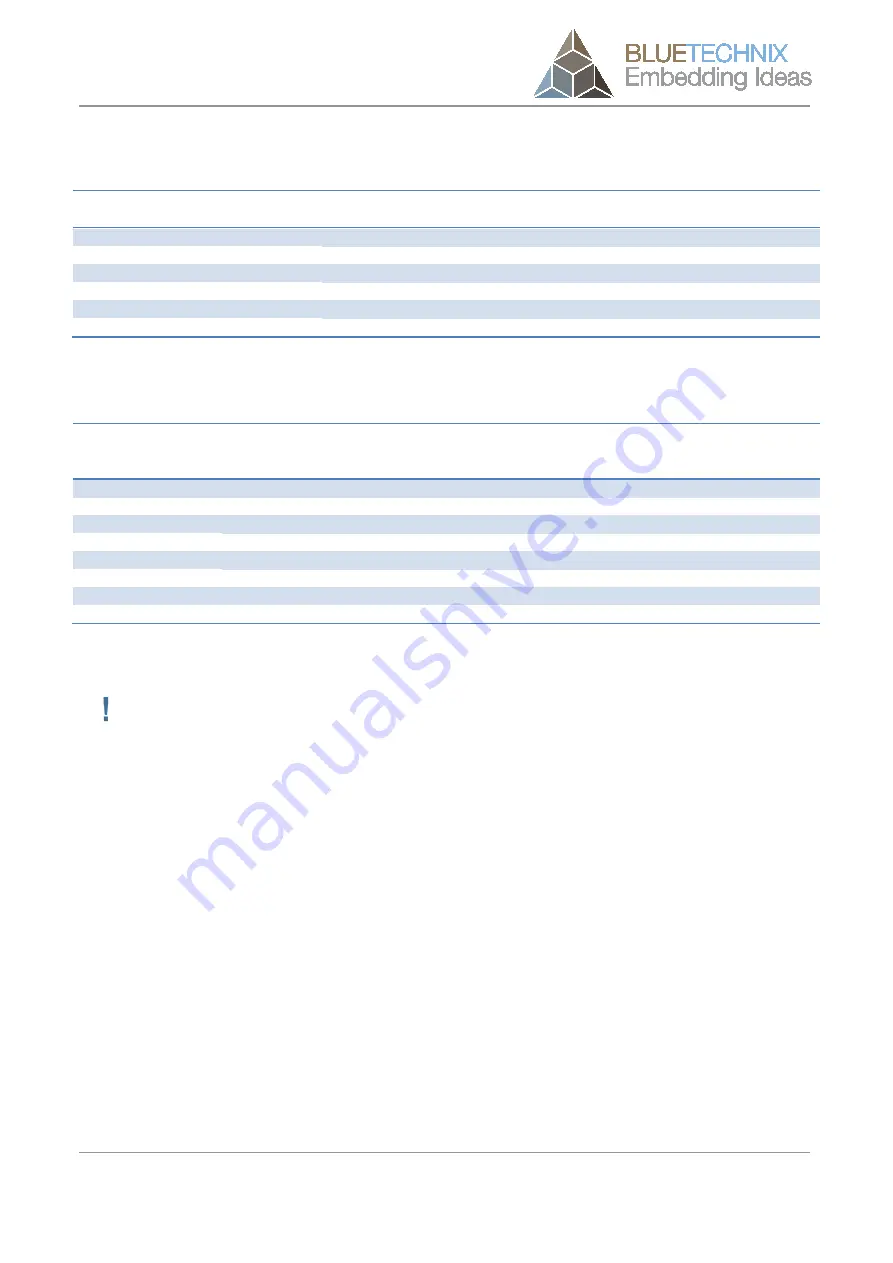
Hardware User Manual - Argos3D – P100
Last change: 22 August 2013
Version
1.5
7.3.3
Typical Integration Time
Measuring range [mm]
Integration time for white target
(90%) [ms]
Integration time for gray target
(18%) [ms]
500
1,0
1,0
1000
1,0
1,5
1500
1,5
2,0
2000
1,5
3,0
2500
2,0
5,0
1)
3000
2,5
10,0
1)
Table 7-4: Typical Integration Time
7.3.4
Typical Range
Integration time
[ms]
Minimum distance
for white target
(90%) [mm]
Maximum
distance for white
target (90%) [mm]
Minimum distance
for gray target
(18%) [mm]
Maximum
distance for gray
target (18%) [mm]
0,5
300
1500
100
500
1,0
300
2000
100
1000
1,5
300
2000
300
1500
2,0
500
3000
1)
300
2000
2,5
500
3000
1)
300
2000
3,0
1)
500
3000
1)
300
2000
5,0
1)
500
4000
1)
300
3000
1)
10,0
1)
500
6000
1)
500
3000
1)
Table 7-5: Typical Range
1) Note
The integration time limit can be disabled with the source command
DisableIntegrationTimeCheck
. Otherwise the max integration time is limited to 2,7ms. Refer to
our support internet site for information how to apply this command (see 7.7.1).
© Bluetechnix 2013
Page | 16