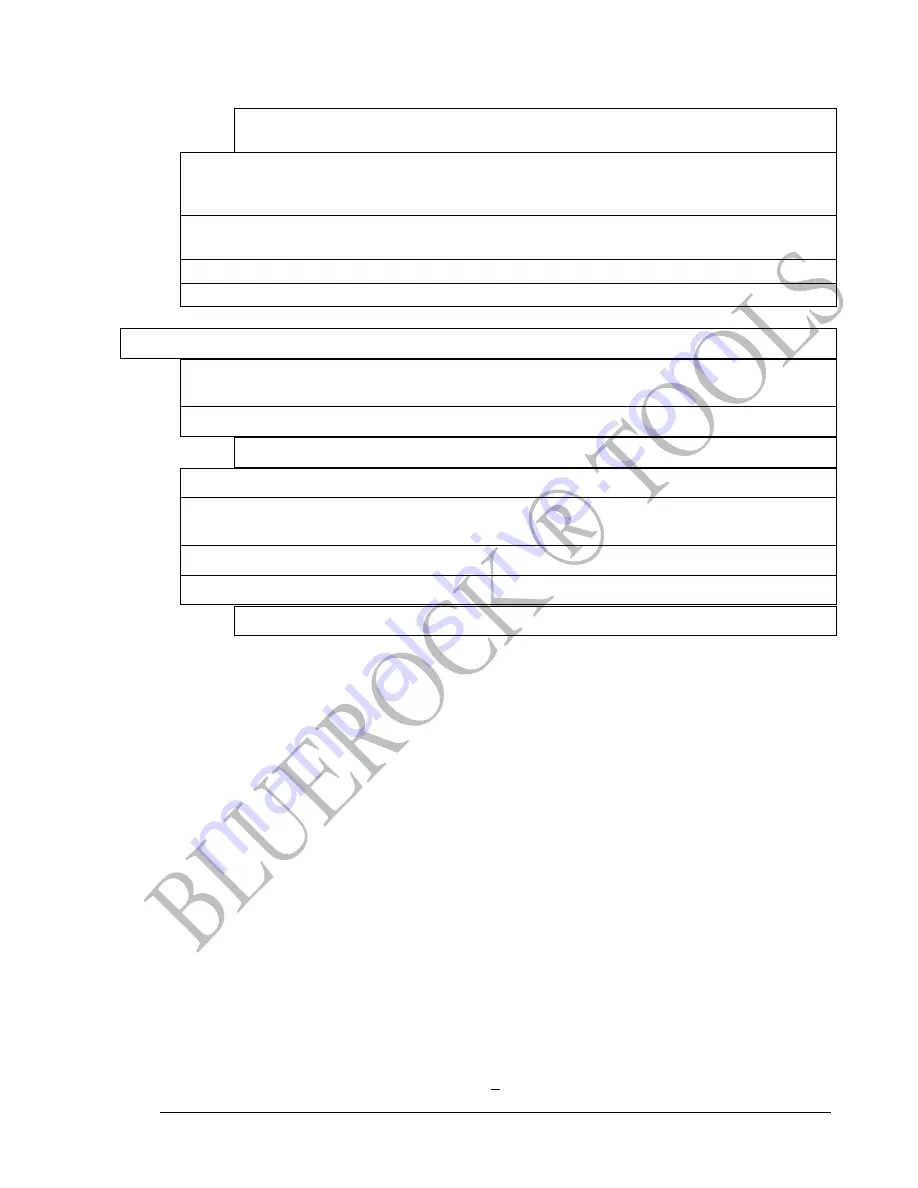
G D C 4 C O R E D R I L L
9
o
If drilling completely through the material, stop drilling after breaking through
the bottom, stop bit rotation and slowly pull out the bit and the core.
Ø
If drilling to a specified depth (and not breaking all the way through the material)
leave the drill bit rotating until you reach your desired depth. Continue to leave the
drill bit rotating as you pull the bit completely out of the material.
Ø
Once the drill is safely back to the non-drilling position, adjust the throttle valve to
enable the engine back to the idle state.
Ø
Switch engine to “off” position.
Ø
Turn water valve off. Turn off main water supply as well.
INSTALLING CORING BITS
Ø
WARNING: Core bits can be sharp and should only be handled with gloves so as not
to cut the user during installation or removal.
Ø
Check that the bits are not damaged.
o
NOTE: Coring bits that are damaged should not be used.
Ø
Make certain the machine is turned off.
Ø
Apply grease to the spindle thread to prevent corrosion and allow easier core bit
removal.
Ø
Insert the coring bit and screw it onto the drill spindle.
Ø
Tighten the bit until fully tightened.
o
Use wrenches that fit the spindle and coring bit to fully tighten.