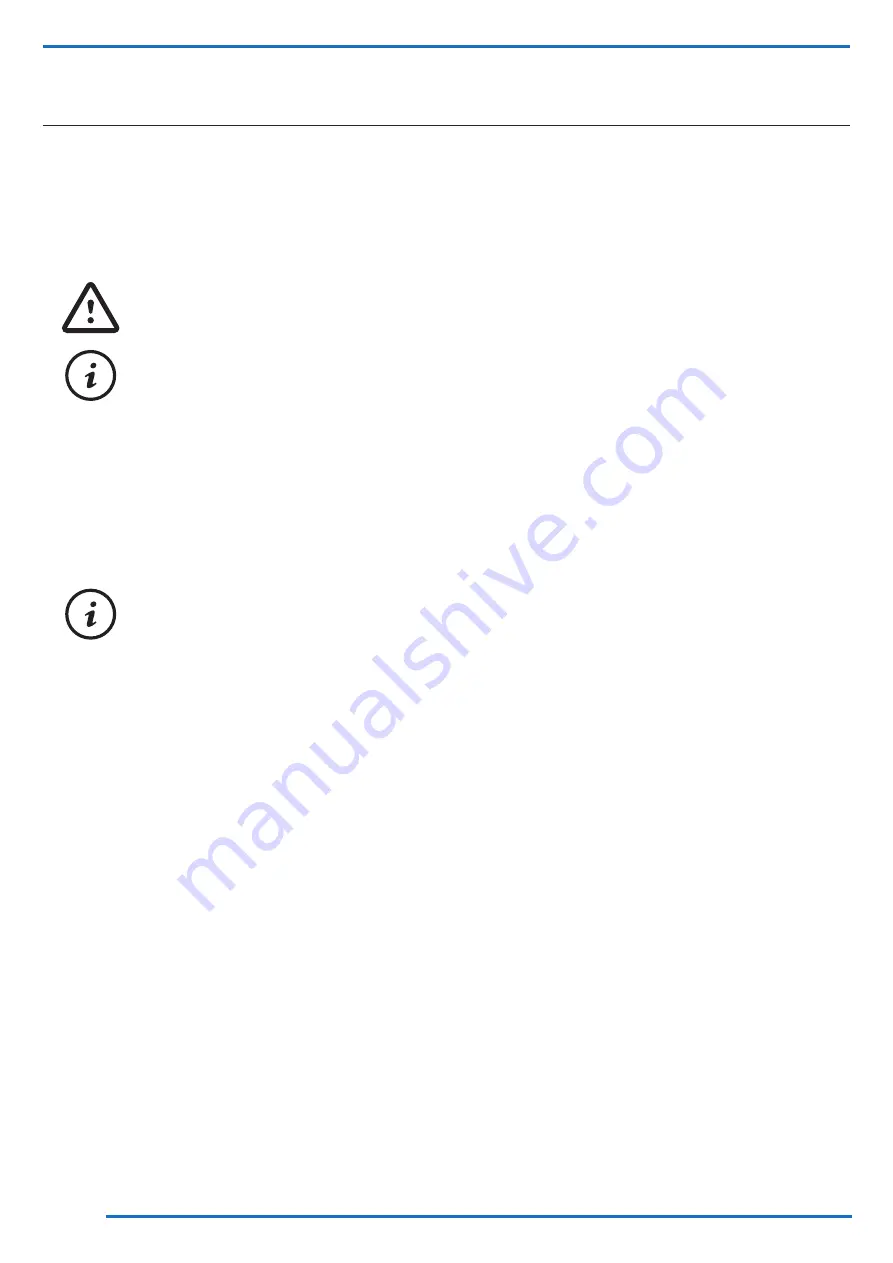
44
We reserve the right to make changes without any prior notice.
Translation from original instructions
6.2 First starting
When the unit is started for the first time, some important tests and checks must be done.
6.2.1 Hydraulic tests
So that the unit can operate, the external OK signal device must be closed (refer to the wiring diagram provided with the
unit).
The external OK signal device must be short-circuited if not needed for system requirements.
Water circulation can be managed by the control of the unit or by a control outside the unit.
If water circulation is controlled by an external control, the pump must be started before the unit starts and
stopped after the unit stops.
We advise an advance on starting and a delay on stopping of at least 5 minutes.
Start the unit by acting on the user interface of the control.
Check that the water flow switch/differential pressure switch is working correctly by closing the shut-off valve at the outlet of
the unit; this should cause the alarm to be displayed on the user interface of the unit.
If not, restore correct operation.
Reopen the valve, reset the alarm and restart the unit.
For units equipped with pump unit, if the pump is noisy, close the delivery valve until normal operation has been restored.
This can occur when the head loss of the system differs considerably from the discharge head of the pump.
If there is a water leak on first start-up, it could be a problem with bedding in of the mechanical seal. We
therefore advise pressurizing the pump body 2 or 3 times by closing and opening the delivery valve so as to
correctly bed in the seal.
If this operation does not solve the problem, contact the technical support department.
6.2.2 Functional tests
With the starting of the unit, a few seconds after the starting of the pump, if managed by the control, the compressors will
start according to the request of the thermoregulation.
After a few hours of operation of the compressors, check that the liquid sight glass has a green ring: if it is yellow, there is
moisture in the circuit. In this case, the circuit must be dried by qualified authorised personnel.
Check that bubbles do not appear at the liquid sight glass. The continuous passage of bubbles can indicate there is insuffi-
cient refrigerant and it needs to be topped up. In this case, check that the subcooling value is at least 5°C. But the presence
of a few bubbles is allowed during transients.
The end user is required to keep a register of the unit (not supplied), which will allow a record to be kept of the work carri-
ed out on the unit. This will make it easier to appropriately organize the work to facilitate the checks and the prevention of
malfunctions.
State the following in the register: the type of refrigerant, the date and type of work done (routine maintenance or repair),
description of the work with any parts replaced, measures implemented, the operator who carried out the work and his
qualification.