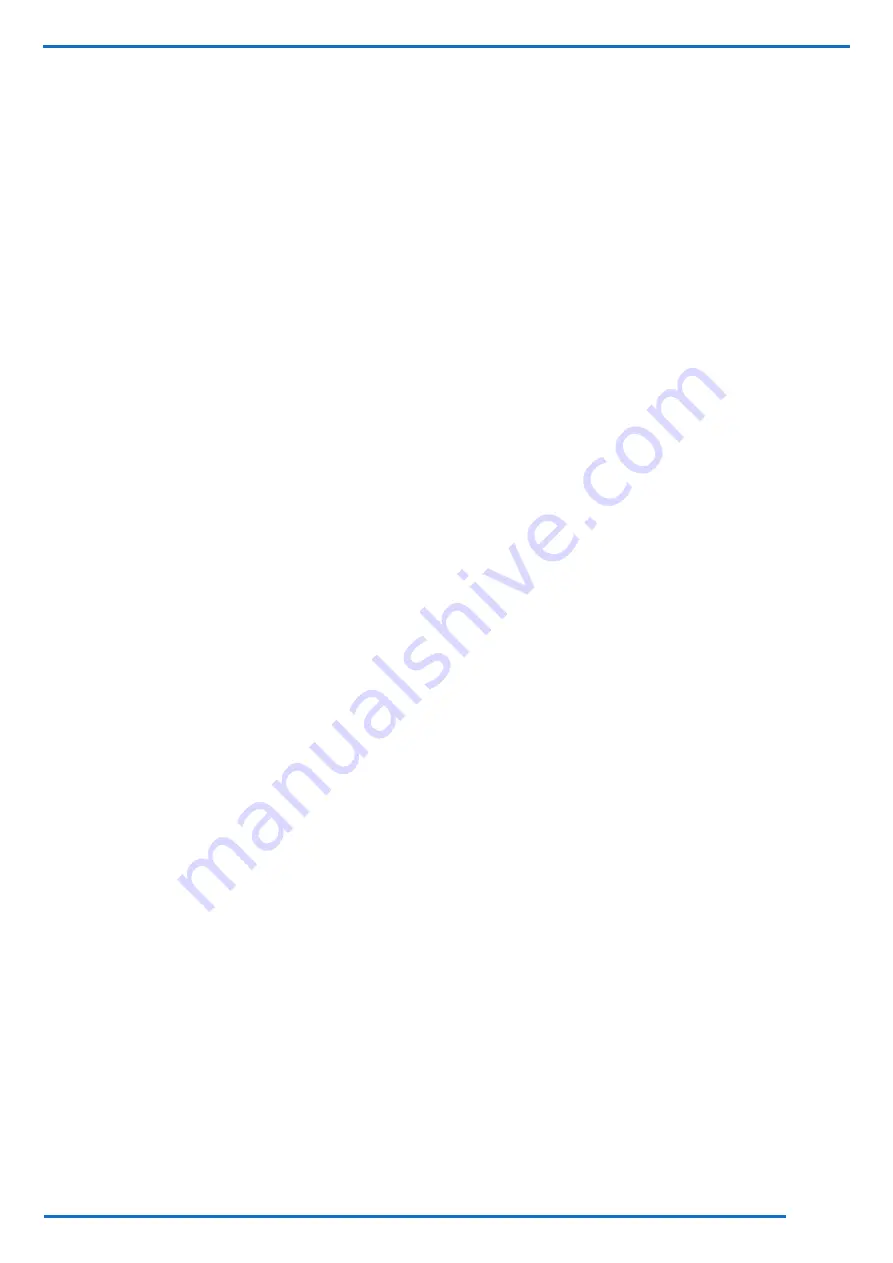
31
We reserve the right to make changes without any prior notice.
Translation from original instructions
5.3.2 Noise attenuation
The units are designed and built paying particular attention to keeping down noise emission during operation.
In addition to the standard versions, there are “LN” (Low Noise) and “SLN” (Super Low Noise) versions for which further
devices are used for lower noise emission.
Correct installation for both the place and the components, as shown in the relevant chapter, prevents resonances,
reflections and vibrations that can be particularly bothersome.
If, after following the instructions above, further attenuation is required, the use of acoustic barriers is a valid solution.
It is essential to be careful that any work done to soundproof the unit does not affect its correct installation or its correct
operation.
That is why it is necessary to avoid restricting the service spaces and installing covers that create recirculation between air
supply and exhaust.
5.3.3 Minimum distances
The service spaces to comply with are shown on the dimensional drawings attached to the documentation of the unit.
It is essential to ensure an adequate volume of air on the suction side and on the delivery side of the condensing coil.
It is very important to avoid recirculation between suction and delivery, as this would lower the performance of the unit or
even stop its normal operation.
The presence of very high walls near the unit will impair its correct operation.
Units should be installed a minimum of three metres apart.
It is, in any case, advisable to leave sufficient space between the units to allow removal, if necessary, of their larger compo-
nents such as the exchangers, compressors or pumps.