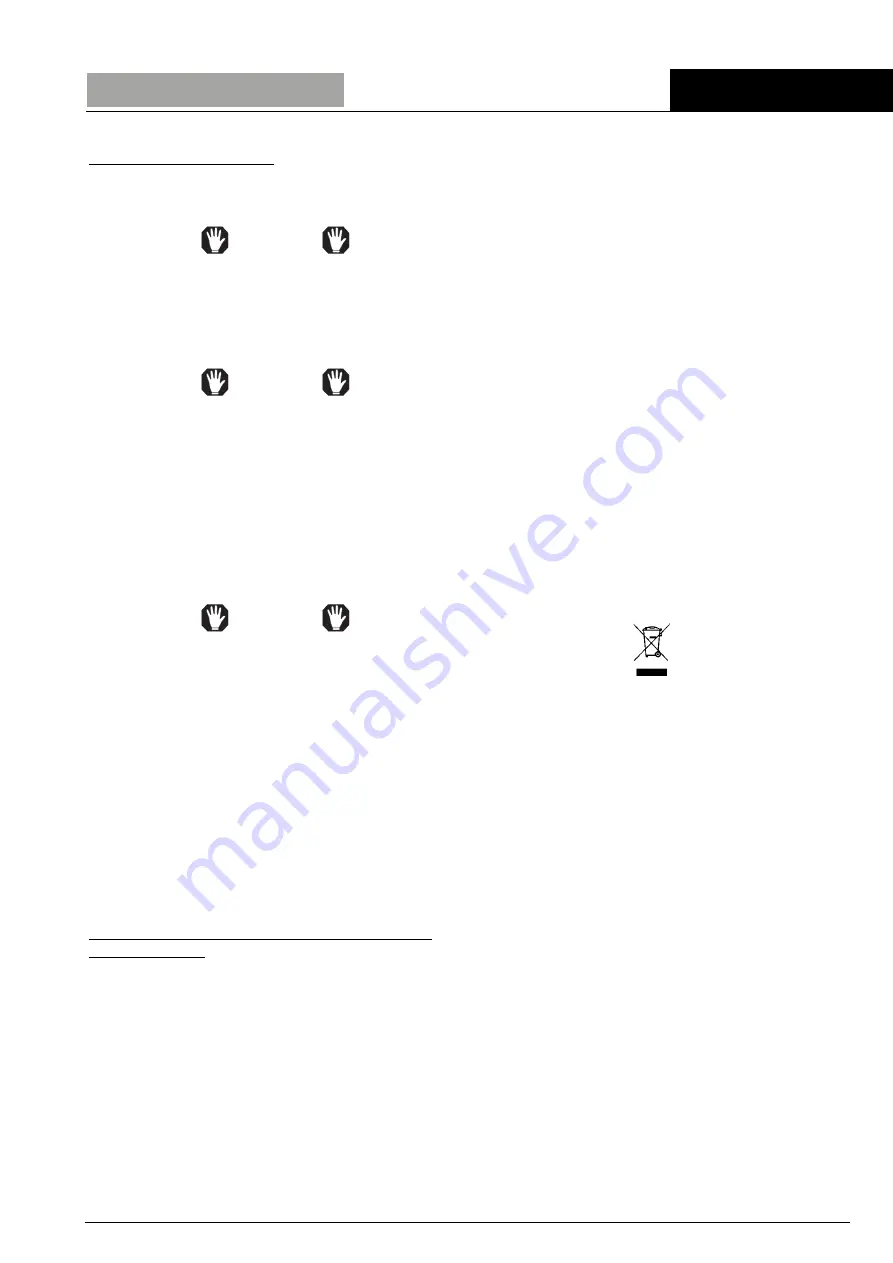
13
ENGLISH
Part 2: For the operator
2.2 CLEANING (Fig. 10)
2.2.a General information
Strict compliance with the maintenance instructions in this
section will keep your machine in a good working condition
and will notably reduce the need for repairs.
ATTENTION
If any machine component becomes faulty, FIRST CHECK
that all the instructions given in the previous paragraphs
have been complied with during use.
Repairs must be carried out immediately, as soon as the
fault occurs. This will prevent the trouble from becoming
worse and damaging other parts.
ATTENTION
Daily operations to carry out when work has ended, with
the machine OFF , the main circuit-breaker disconnected,
the water cocks off and the washing tub empty.
1. Thoroughly clean the inside parts of the machine.
2. Remove the filter (22) from the bottom of the machine
by releasing the overflow (21).
3. Remove the suction protection (23).
4. Wash the filters under running water and fit them
correctly back in their housings.
ATTENTION
Frequently check and clean the spraying units, removing
them from their housings and eliminating any dirt and
fouling. The frequency with which this operation must be
carried out depends on the quantity of dirt or on the
unsatisfactory washing results. Never use corrosive
products like sodium hypochlorite (bleach) or hydrochloric
acid, wire wool or steel brushes to clean either the inside
or outside parts of the machine.
2.3. PREVENTION MAINTENANCE (Fig. 10)
The preventive maintenance operations must be carried
out with the machine OFF, the main circuit-breaker
disconnected, the water delivery cocks off and the washing
tub empty.
2.3.a Checking and cleaning the spray arms and
nozzles (Fig. 10)
Periodically check to make sure that the lower washing
arm and rinsing arm (24) and their relative nozzles are not
clogged (26/27).
Cleaning the lower/upper unit
1. Unscrew the ring nut and lift the arm (24).
2. Wash the washing and rinsing arm.
If the nozzles (27) are clogged, unscrew them to
demount and clean, taking care to prevent the shape of
the nozzle from being deformed. After cleaning, fit the
nozzles exactly back in their original positions.
3. Remount all parts by complying with the above
instructions in reverse.
2.4 DESCALING
Where hard water is present lime scale deposits will for
in the machine and on dishes, which must, for reasons of
hygiene, be removed by descaling.
Advice on operation procedures and frequency for this
treatment are generally given by the detergent supplier,
who can provide suitable products.
In order to avoid damaging the machine, do not
exceed recommended doses, follow the detergent
producer’s directions scrupulously and, having
finished operations, rinse thoroughly.
2.5 TEMPORARY STOPPAGE
If the machine is to be left inactive for a period of some
weeks, it is advisable beforehand to load the tank and run
a few empty cycles with clean water then drain, so as to
avoid the formation of unpleasant odours.
If necessary, repeat the process several times until the
water is still clean after washing.
If the stoppage is to be very long, it is advisable to
drain the water from the boiler and from the electric
pump.
2.6 DEMOLITION and DISPOSAL
When the machine is to be scrapped, drain the water
from the tank and from the boiler, as indicated in the
points above, and disconnect the machine from the water
and electricity supply networks, then dispose of the
components according to current regulations, respecting
national and local ecological and environmental
legislation, and taking care to separate the parts as
follows:
- metallic parts: body work, surfaces, panels, filters;
- electrical parts: motors, remote switches, micro-
switches, cabling;
- plastic parts: connectors, baskets;
- rubber parts: tubes, couplings
The producer declines all responsibility for any
printing errors contained in this booklet.
The instructions, drawings, tables and everything
else in this manual are of a confidential technical
nature. For this reason, none of the information may
be either completely or partially duplicated or disclosed
to third parties without prior written authorization
from BLUE SEAL which is the sole proprietor and
which reserves the right to make any modifications as
may be considered necessary without advance
warning.