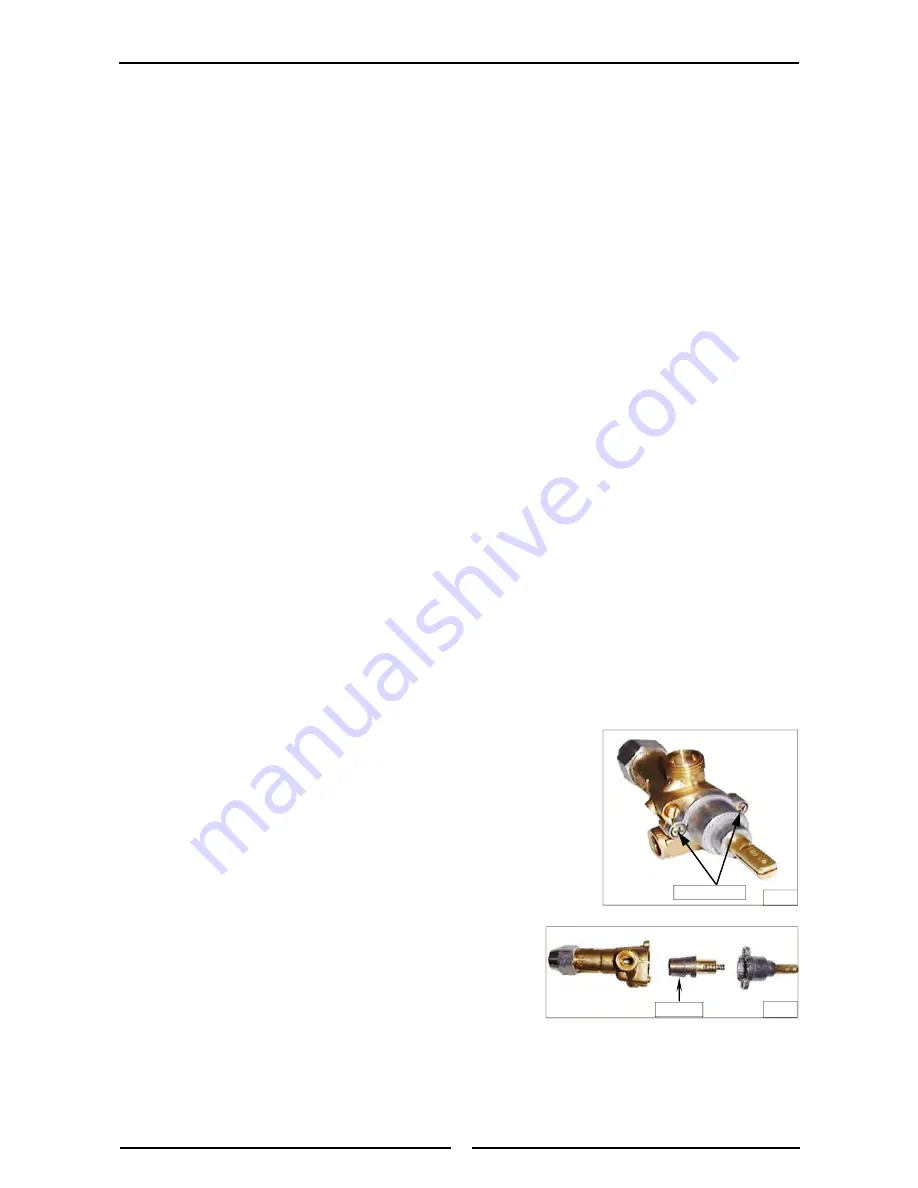
16
Cleaning and Maintenance
Target Top
a. This should be kept clean of any build up of food spillage’s. Provided cast iron work surface is
regularly used it will maintain itself in good condition with no special cleaning required.
b. Clean any food residue and spillage from channels around centre casting and main plates before
use.
c. DO NOT use water on castings while they are still hot as cracking may occur. Should it
be necessary to clean castings, allow castings to cool and then remove for cleaning. Clean using
a soft cloth moistened with a mild detergent and hot water solution and a scrubbing brush. Dry
thoroughly with a dry cloth.
d.
Remove drip tray and clean with a mild anti bacterial detergent and hot water solution using a
soft bristled brush.
Dry drip tray thoroughly with a dry cloth.
Stainless Steel Surfaces
a. Clean exterior surfaces of target top / range with hot water, a mild detergent solution and a soft
scrubbing brush. Note that gas control knobs are a push fit onto gas control valve spindles and
can be removed to allow cleaning of front control panel.
b. Baked on deposits or discolouration may require a good quality stainless steel cleaner or stainless
steel wool. Always apply cleaner when appliance is cold and rub in direction of grain.
c. To remove any discolouration, use an approved stainless steel cleaner or stainless steel wool.
Always rub in direction of grain.
d. Dry all components thoroughly with a dry cloth and polish with a soft dry cloth.
Periodic Maintenance
NOTE: All maintenance operations should only be carried out by a qualified service person.
To achieve best results cleaning must be regular and thorough and all controls and mechanical parts
should be checked and adjusted periodically by a qualified service person. If any small faults occur, have
them attended to promptly. Don't wait until they cause a complete breakdown. It is recommended that
appliance is serviced every 6 months.
Gas Control Valve Re-Greasing
Gas control valve should be dismantled and greased every 6 months to ensure correct operation.
To carry out this operation;-
a. Remove gas control knobs from gas tap spindles by pulling
knobs away from control panel.
b. Remove drip tray from appliance.
c. Remove two screws on underside of control panel, securing
control panel to hob.
d. Remove control panel from front of appliance.
e. Remove 2 screws holding shaft plate to gas control body and
remove control shaft and plate.
(See Fig 7).
Note orientation of
shaft for correct re-assembly.
f. Using needle nose pliers or similar, pull out gas control
spindle, again noting its orientation.
g. Apply a suitable high temperature gas cock grease or
lubricant such as ROCOL - A.S.P (Anti scuffing paste)/
Dry Moly Paste to outside of spindle.
(See Fig 8).
h. Replace spindle and re-assemble gas control in reverse
order.
i. Refit control panel to appliance and secure with 2
screws.
j. Refit knobs to gas control valve spindles.
Two Screws
Fig 7
Spindle
Fig 8
Summary of Contents for GE570
Page 9: ...7 Dimensions Dimensions GE570 GE576 ...
Page 20: ...18 Wiring Schematic Static Oven Schematic GE570 ...
Page 21: ...19 Wiring Schematic Static Oven Wiring Diagram GE570 ...
Page 22: ...20 Wiring Schematic Convection Oven Schematic GE576 ...
Page 23: ...21 Wiring Schematic Convection Oven Wiring Diagram GE576 ...
Page 32: ......