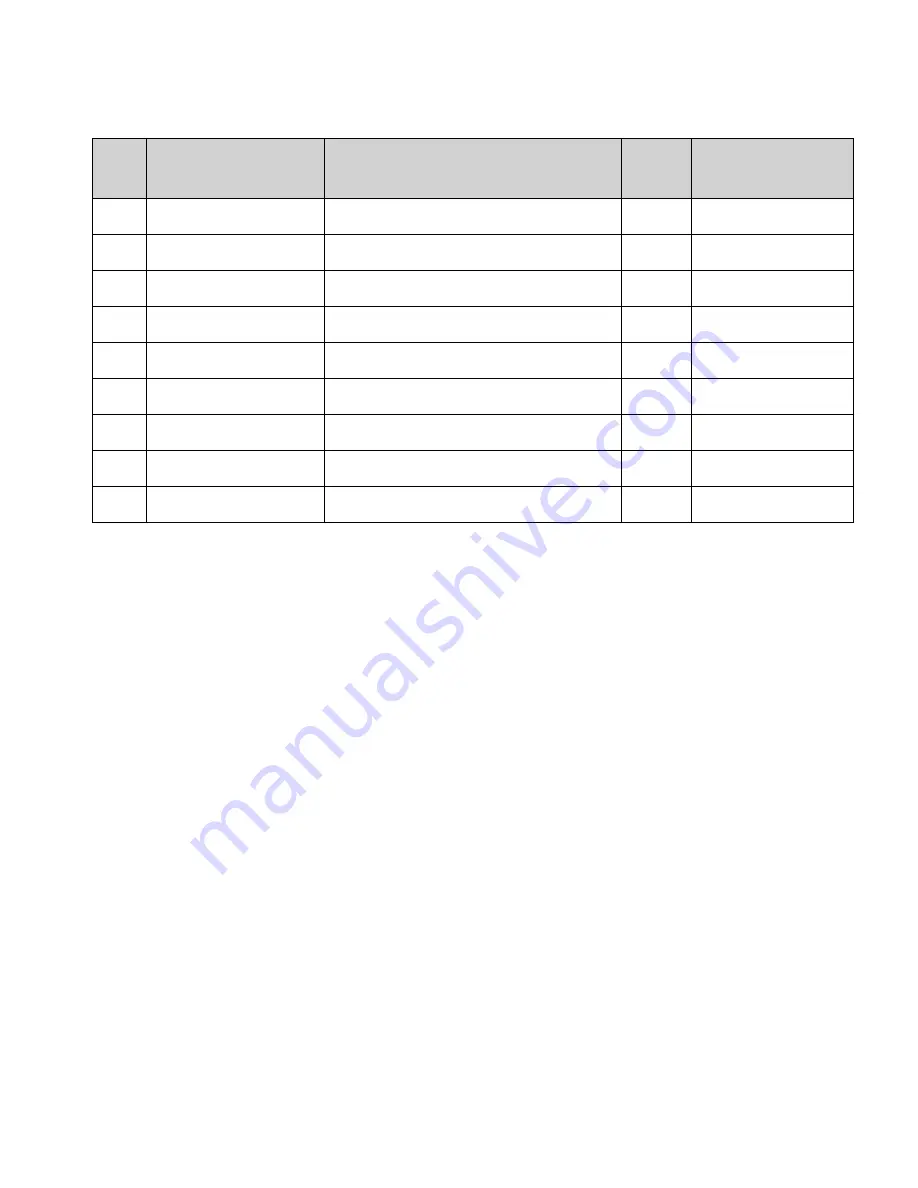
LIFT CARRIAGE (Three Stage Mast)
Pos.
Part Number
Description
Qty.
Reqd.
Notes
1
0000-000221-00
BOLT, M12 X 30
4
2
0000-000060-00
WASHER, LOCK, M12
4
3
0000-000373-00
WASHER, FLAT, M12
4
4
2320-631000-00
BACKREST
1
5
2125-641000-30
LIFT CARRIAGE
1
6
2125-630001-00
FORK
2
7
2125-630001-10
PIN ASSEMBLY
2
8
2125-612000-00
ROLLER ASSEMBLY
4
9
0000-000030-00
SCREW, M10 X 16
1
111
Summary of Contents for BGL-33
Page 9: ...Figure 2 2 Sample of Operator Check List R6479 9...
Page 12: ...NOTES 12...
Page 18: ...NOTES 18...
Page 38: ...NOTES 38...
Page 44: ...NOTES 44...
Page 46: ...Figure 6 1 Drive Assembly R7220 46...
Page 48: ...Figure 7 1 Drive Assembly R7220 48...
Page 49: ...Figure 7 2 Load Wheels R7223 49...
Page 50: ...NOTES 50...
Page 52: ...Figure 8 2 Elevation System Telescopic R7224 52...
Page 54: ...Figure 8 3 Mast Three Stage Mast R7225 54...
Page 56: ...NOTES 56...
Page 58: ...Figure 9 1 Hydraulic System R7228 58...
Page 60: ...Figure 9 3 Elevation System Telescopic R7224 60...
Page 66: ...Figure 9 8 Secondary Lift Cylinder Three Stage Mast R7234 66...
Page 69: ...Figure 9 10 Tilt Cylinder R7236 69...
Page 70: ...NOTES 70...
Page 72: ...Figure 10 1 Electrical System R6478 R7237 72...
Page 73: ...Figure 10 2 Electrical Panel R6478 R7238 73...
Page 75: ...Figure 10 3 Transmission Motor Brake Assembly R6879 75...
Page 76: ...NOTES 76...
Page 77: ...SECTION 11 OPTIONAL EQUIPMENT 77...
Page 78: ...NOTES 78...
Page 80: ...Figure 12 1 Control Arm R7217 80...
Page 82: ...Figure 12 1 Control Arm Continued R7217 82...
Page 84: ...Figure 12 2 Control Head R7218 84...
Page 86: ...Figure 12 3 Drive System R7219 86...
Page 88: ...Figure 12 4 Drive Assembly R7220 88...
Page 90: ...Figure 12 5 Compartment R7221 90...
Page 92: ...Figure 12 6 Frame R7222 92...
Page 94: ...Figure 12 6 Frame Continued R7222 94...
Page 96: ...Figure 12 7 Load Wheels R7223 96...
Page 98: ...Figure 12 8 Elevation System Telescopic R7224 98...
Page 100: ...Figure 12 8 Elevation System Telescopic Continued R7224 100...
Page 102: ...Figure 12 9 Elevation System Three Stage Mast R7225 102...
Page 104: ...Figure 12 9 Elevation System Three Stage Mast Continued R7225 104...
Page 106: ...Figure 12 9 Elevation System Three Stage Mast Continued R7225 106...
Page 108: ...Figure 12 10 Lift Carriage Telescopic R7226 108...
Page 110: ...Figure 12 11 Lift Carriage Three Stage Mast R7227 110...
Page 112: ...Figure 12 12 Chain Assembly R6818 112...
Page 114: ...Figure 12 13 Hydraulic System R7228 114...
Page 116: ...Figure 12 14 Tilt System R7235 116...
Page 118: ...Figure 12 15 Lift System Telescopic R7230 118...
Page 120: ...Figure 12 16 Lift System Three Stage Mast R7231 120...
Page 122: ...Figure 12 17 Lift Cylinder Telescopic R7232 122...
Page 124: ...Figure 12 18 Free Lift Cylinder Three Stage Mast R7233 124...
Page 126: ...Figure 12 19 Secondary Lift Cylinder Three Stage Mast R7234 126...
Page 128: ...Figure 12 20 Tilt Cylinder R7236 128...
Page 130: ...Figure 12 21 Pump and Motor R7229 130...
Page 132: ...Figure 12 22 Electrical System R7237 132...
Page 134: ...Figure 12 23 Electrical Panel R7238 134...
Page 136: ...Figure 12 24 Battery Assembly Optional R7001A 136...
Page 138: ...Figure 12 25 Wire Harness R7240 138...