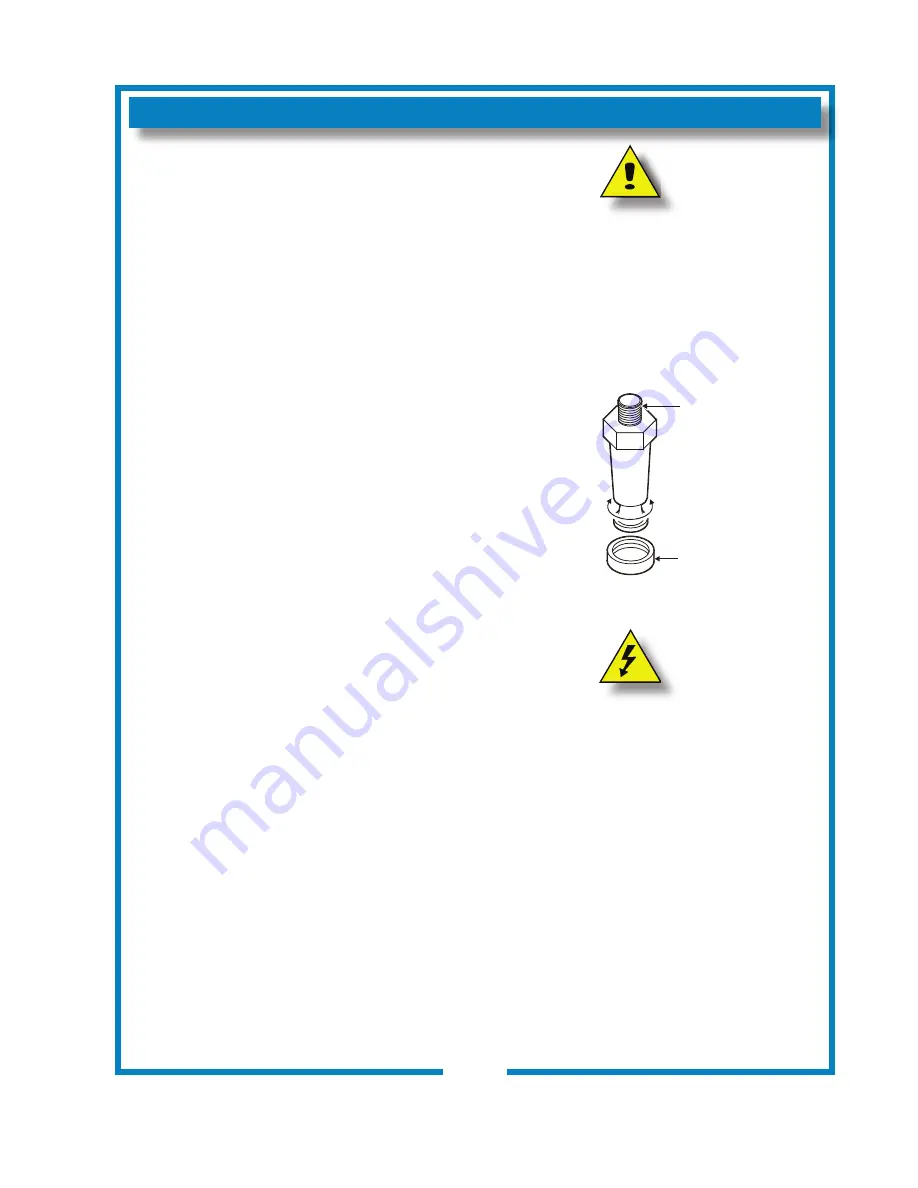
671EX p/n 2M-76624 9221EX Dual Satellite Owmers Manual
5
INSTALLATION INSTRUCTIONS
INSTALL LEGS & LEVEL THE UNIT
The brewer is provided with 4” (100 mm) adjustable legs and
rubber feet. Be sure the legs are securely screwed into the base
of the brewer, and that the rubber feet are properly installed.
The adjustable legs allow the brewer to be leveled. Set the brewer
in its ultimate operating location and check for level with a spirit
level Adjust the brewer for level from front-to-rear, and from side-
to-side. Be sure all four feet rest firmly on the counter.
PLUMBER’S INSTALLATION INSTRUCTIONS
IMPORTANT:
Brewer must be installed on a potable water supply line with a
full-flow pressure between 20 psi (138 kPa) and 90 psi (620 kPa).
NOTE:
If water pressure varies greatly, or exceeds 90 psi (620 kPa) at any
time, a water pressure regulator must be installed. Plumbing
installer must supply the regulator.
Brewer must be connected to a potable water supply. Bloomfield
recommends not less than 1/4” (6 mm) inside diameter copper
tubing for installations of 12’ (4 meters) or less, and not less than
3/8” (10 mm) I.d. copper tubing for installations exceeding 12’ (4
meters).
Brewer must be connected to a COLD water line.
NOTE:
DO NOT use a saddle tap for this water line connection.
A shut-off valve must be installed between the main water supply
and the brewer. Plumbing installer must supply the shut-off valve.
A 1/4-turn ball valve is recommended.
Flush the water line before connecting to the brewer.
Bloomfield highly recommends the use of the provided water
strainer to help prevent deposits in the brewing system.
CAUTION:
Hazard from
Unstable Equipment
Rubber feet must be installed
on each leg of the brewer. Legs
must be adjusted so that all four
feet rest firmly on the counter.
Failure to properly install the
feet can result in movement of
the brewer, which can cause
personal injury and/or damage
to the brewer.
Fig. 2 Adjustable Leg
CAUTION:
Electric Shock
Hazard
Brewer must be properly
grounded to a reliable earth
ground to prevent possible
shock hazard. Do not assume
a plumbing line will provide
such a ground. Electrical shock
may cause serious injury.
SCREW INTO
BREWER
FRAME
ADJUST
FOR
HEIGHT
ATTACH
RUBBER
FEET