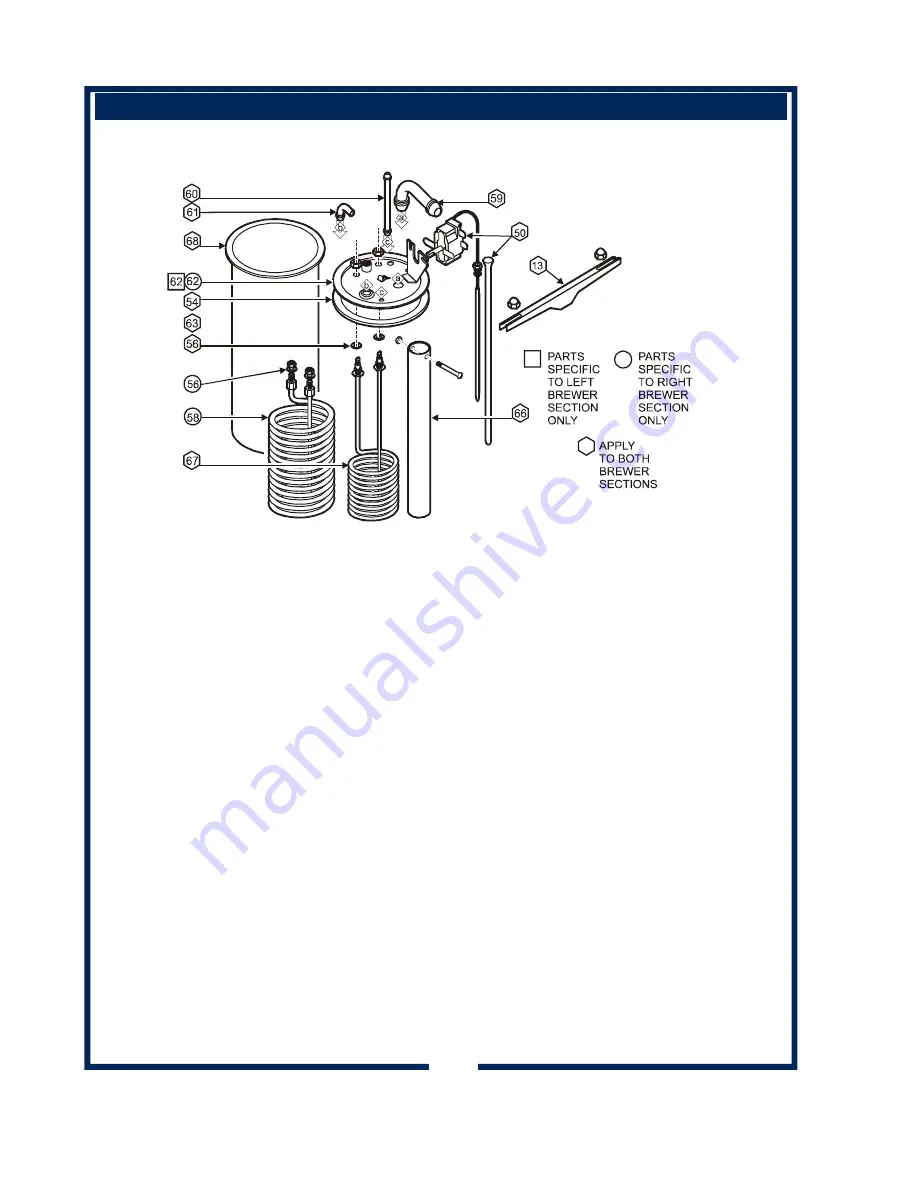
EXPLODED VIEW & PARTS LIST
HOT WATER TANK ASSEMBLY
ITEM
PART NO. DESCRIPTION
USED ON
13
8043-5
Hold Down Strap
All
50
86280
Thermostat w/Thermo Well
All
54 8043-12
Tank
Cover
Gasket
All
56 8043-30
Seal
Gasket
All
58
8540-6
Hot Water Coil
Right Side Only
59 8043-8
Inlet
Elbow
All
60 8043-15
Vent
Tube
All
61 8043-11
Outlet
Elbow
All
62
8512-45
Tank Cover (Plate Only, 6 holes)
Left Side Only
8514-68
Tank Cover (Plate Only, 8-holes)
Right Side Only
66
8043-24
Water inlet Tube
All
67
8549-1
Heating Element (120V 2000W)
8790, 8792
8716-1
Heating Element (230V 3500W)
8791, 8793
68
8043-10
Tank
Body
All
COMPLETE SPARE TANK COVER
8549 WF-300 Spare Cover Assembly (120V, 2000W
8790, 8792
With Coil - all parts mounted to cover)
8716-300 Spare Cover Assembly (230V, 3800W
8791, 8793
With Coil - all parts mounted to cover)
18
625
75873
Owner
s M
anual G
ourmet
1000 Dual
Airpo
t Br
ewers