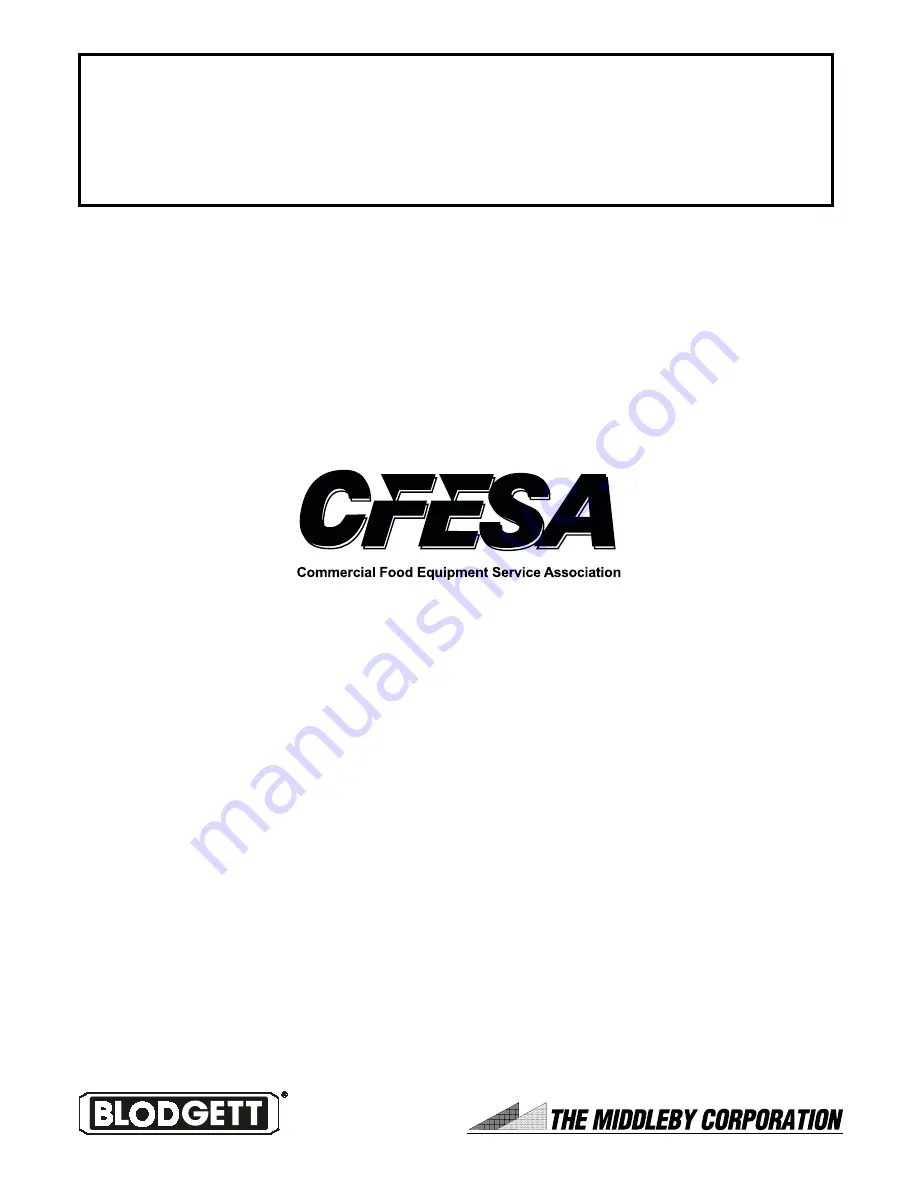
Blodgett is proud to support the Commercial Food Equipment
Service Association (CFESA). We recognize and applaud
CFESA's ongoing efforts to improve the quality of technical
service in the industry.
WARNING
Improper installation, adjustment, alteration, service or maintenance
can cause property damage, injury or death. Read the installation,
operating and maintenance instructions thoroughly before
installing or servicing this equipment.
NOTICE
During the warranty period, ALL parts replacement and servicing should be performed by
your Blodgett Authorized Service Agent. Service that is performed by parties other than
your Blodgett Authorized Service Agent may void your warranty.
NOTICE
Using any parts other than genuine Blodgett factory manufactured parts relieves the manu-
facturer of all warranty and liability.
NOTICE
Blodgett reserves the right to change specifications at any time.
G.S. Blodgett Corporation • 50 Lakeside Avenue, Box 586 • Burlington, Vermont 05402 • USA
Telephone (800) 331-5842, (802) 860-3700 • Fax: (802) 864-0183
www.blodgettcorp.com
Summary of Contents for BG2136 Double
Page 1: ......
Page 4: ...iv ...
Page 6: ...vi NOTES ...
Page 24: ...18 ENGLISH NOTES SECTION3 OPERATION ...
Page 30: ...24 ENGLISH ...
Page 32: ...26 ENGLISH page 1 FRANÇAIS page 57 ESPAÑOL página 85 DEUTSCH seite 29 ...
Page 34: ...28 ENGLISH page 1 FRANÇAIS page 57 ESPAÑOL página 85 DEUTSCH seite 29 ...
Page 36: ...30 ENGLISH page 1 FRANÇAIS page 57 ESPAÑOL página 85 DEUTSCH seite 29 ...
Page 38: ...32 ENGLISH page 1 FRANÇAIS page 57 ESPAÑOL página 85 DEUTSCH seite 29 ...
Page 40: ...34 ENGLISH page 1 FRANÇAIS page 57 ESPAÑOL página 85 DEUTSCH seite 29 ...
Page 42: ...36 ENGLISH page 1 FRANÇAIS page 57 ESPAÑOL página 85 DEUTSCH seite 29 ...
Page 44: ...38 ENGLISH page 1 FRANÇAIS page 57 ESPAÑOL página 85 DEUTSCH seite 29 NOTES ...
Page 46: ...Fig 6 2 Wiring diagram BG2136 Gas Oven 208 240V 50 60 Hz 1 Ph ...
Page 48: ...NOTES ...
Page 49: ...NOTES ...