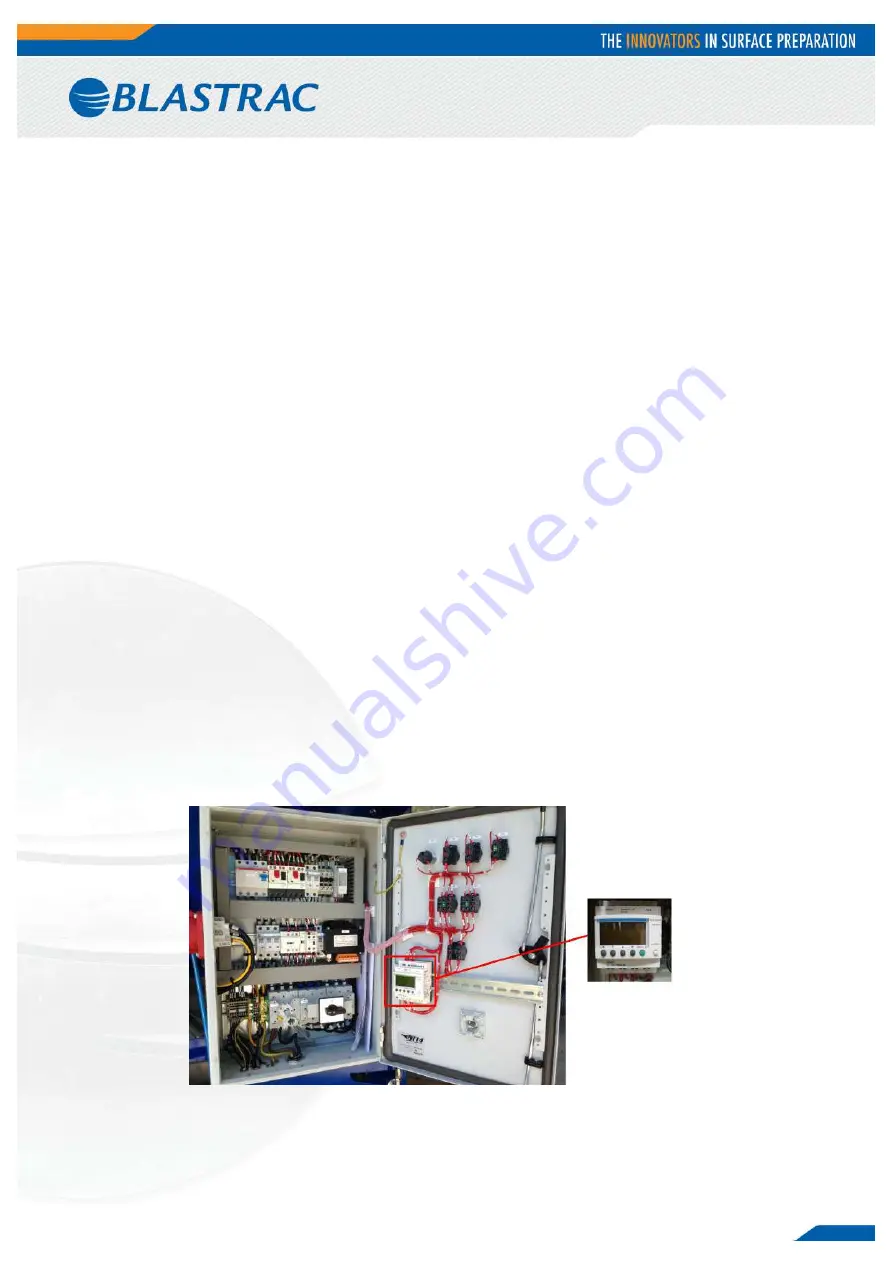
19
6.3
HEPA-filter*
*Only if the machine is fitted with the HEPA-filter option.
The HEPA filter should always be covered when the machine is not in use.
Cover the HEPA filter in such a manner that dust, dirt and moisture cannot get inside the HEPA-filter.
The easiest way is to just wrap the HEPA-filter box in plastic stretch foil. Use tape to ensure the stretch foil
stays in place.
An efficiency test of the dust collector must be performed at least every 12 months, which include:
-HEPA-filter must be replaced if the efficiency of the filter element is not adequate (leakage test
performed with a photometer), or if the airflow of the machine is reduced to 75% of the factory
value due to clogging of the filter(s).
-Testing that the maximum permissible filter surface load of the placed filter is not exceeded.
-An electro technical safety test, performed by a competent person. (NEN 3140 or something similar. Check
the national regulations.)
6.4
Pulse system
The Dust collector is provided with an air pulse cleaning system which increases the life of the filter cartridges
and ensures a constant suction power.
The system works by use of pressurized air, built up by a compressor
The cooled air passes a control valve, which regulates the systems pressure , and then builds up pressure in
the pulse tank.
Normally the pressure in the system lies between 6 and 7 bar. The control valve is activated above 7 bar.
The safety valve mounted on the compressor is activated at approximately 10 bar.
This provision is to ensure that when there is a defect in the Control valve, the pressure in the pulse tank
remains within safe limits.
If the pressure of 6 bar is not reached, it is possible that either there is too much water in the pressure tank or
the air filter of the compressor is dirty.
If inspection of the compressor and draining of the pressure tank shows no abnormalities, it is possible that
either there is a leakage in the air tubing, or the control valve is defect. In that case replace the defective
parts or have it checked by Blastrac.
When there is pressure but the pulse system does not function, there might be a problem in the electrical
system which controls the pulsing system. Check the wiring and the PLC-settings.
Advised is to take contact with Blastrac Support in order to prevent operational problems.