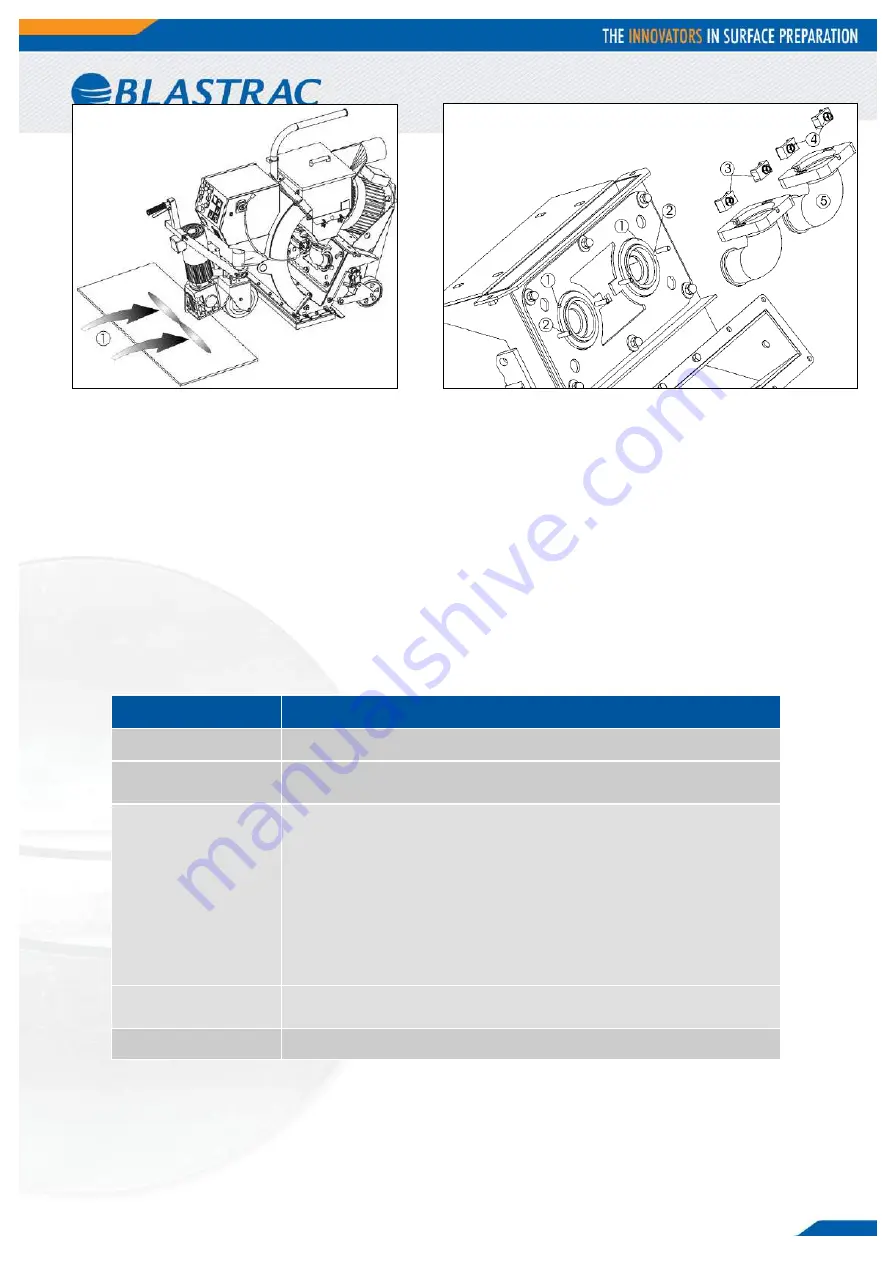
20
WARNING! Never loosen the cage clamps lever or try to adjust the blast
wheel cover when the machine is in operation!!
6. Maintenance
Pay attention to Chapter 3
"Safety"
during maintenance and repair works.
Failures due to inadequate or incorrect maintenance may generate very
high repair costs
and long standstill
periods of the machine.
Regular
maintenance therefore is imperative.
Operational safety and service life of the machine depends, among other things, on proper maintenance.
The following table shows recommendations about time, inspection and maintenance for the normal use of the
machine.
Operating hours/
time period
Inspection points, maintenance instructions
12 h after repairing
Check all accessible screw connections for tight seat.
Every 3 hour
Check the separator tray, the hopper, the feed spouts and blast
wheels unit for foreign matter and large contaminants.
Daily and prior to
starting work
Check that all safety devices working adequate.
Check the feed spouts, magnet- and brush sealing.
Check the blastwheels, control cages and liners.
Check the electric connections for sediments of dirt or foreign bodies.
Check the electric motors for dirt and other contaminants.
Check all safety devices working adequate.
Check the function of the residual current operated device.
Check the hose connections for tightness and fixed seat.
Check all hoses on the machine for damages or leakage.
Make sure that the dust bin is emptied
Every 3 months
Check the tension of the V-belts
Clean the chain drive of the drive unit and check the tension.
Annually
Full overhaul and cleaning of the complete machine.
The time indications are based on uninterrupted operation. When the indicated number of working hours is not
achieved during the corresponding period, the period can be extended. However a full overhaul must be
carried out at least once a year. This technical inspection shall be carried out by the manufacturer or an
instructed person.